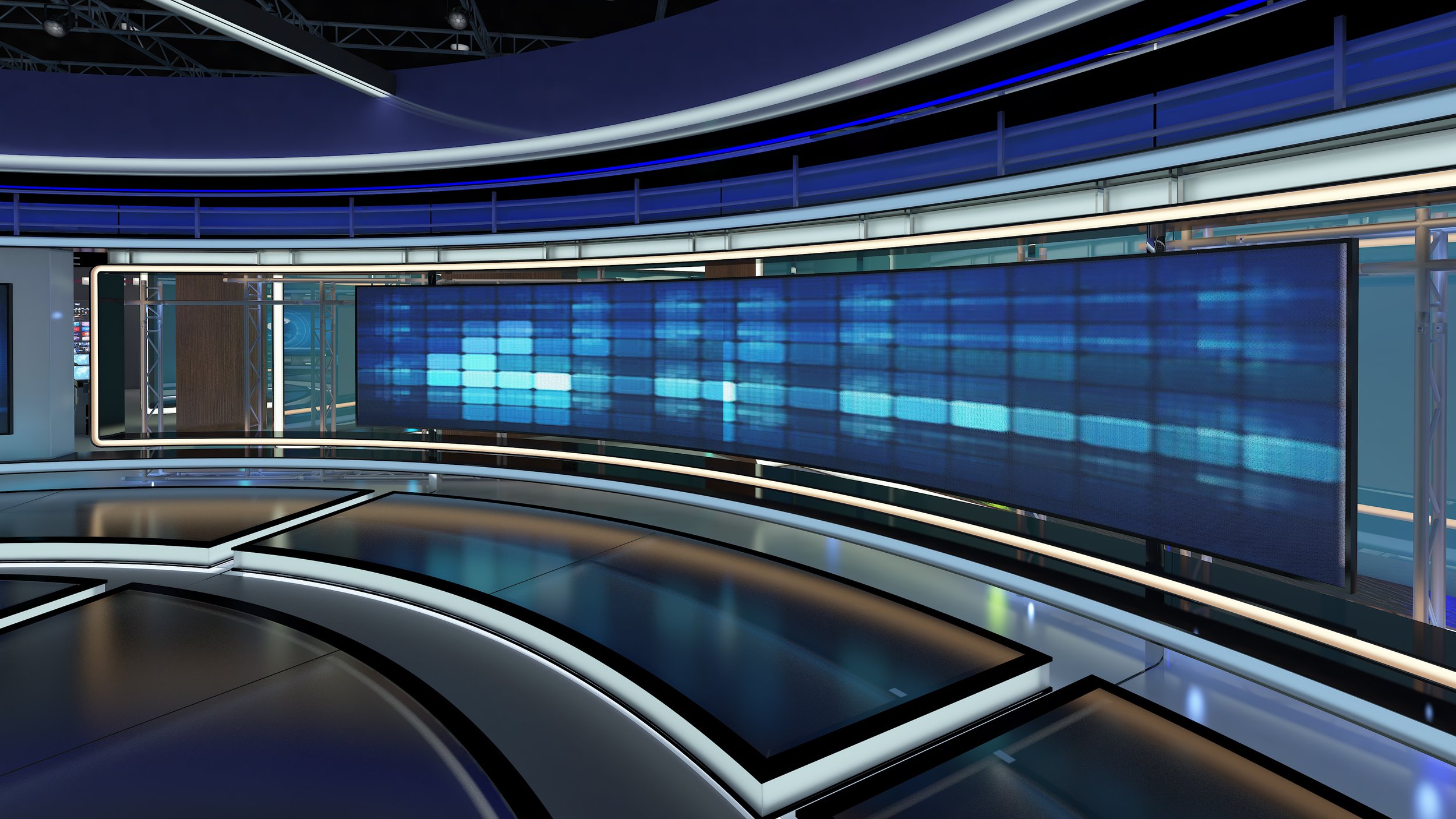
Industry News
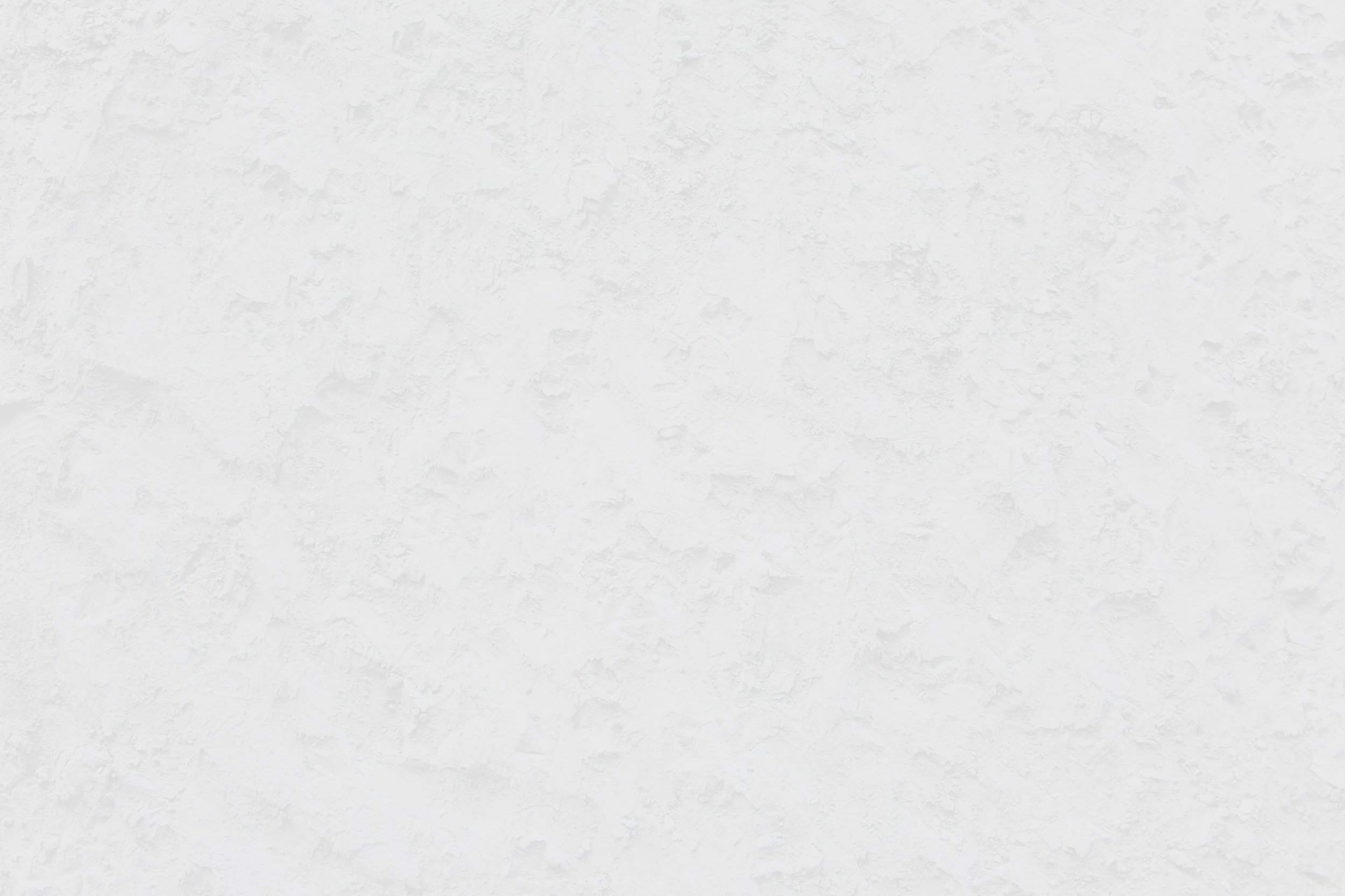
OSHA Tips to Protect Workers During the Holiday Season
Author, Jadyn Brandt, Client Communications Coordinator, Rancho Mesa Insurance Services, Inc.
As the holiday season approaches, many businesses will experience an increase in demand that can put an extra strain on a workplace and its employees. The surge in work often means more safety challenges for an employer. To deal with the additional strain, employers may be hiring new or seasonal employees, bringing in additional volunteers, and/or expanding their hours. Despite these changes, safety should still remain a top priority.
Author, Jadyn Brandt, Client Communications Coordinator, Rancho Mesa Insurance Services, Inc.
As the holiday season approaches, many businesses will experience an increase in demand that can put an extra strain on a workplace and its employees. The surge in work often means more safety challenges for an employer.
To deal with the additional strain, employers may be hiring new or seasonal employees, bringing in additional volunteers, and/or expanding their hours. Despite these changes, safety should still remain a top priority. Employers must work to train and prepare their employees and volunteers to recognize and prevent job hazards and enact safe work practices.
The Occupational Safety and Health Administration (OSHA) has shared a list of nine safety tips that employers should implement for the holiday season. Here’s what they recommend:
1. Train workers on safe practices in a language they speak and understand
It’s important that all workers are aware of necessary safety practices, rules and regulations. This can include basic safety policies or industry-specific safety trainings. Communicating these policies clearly and effectively is equally as important. Employers should regularly remind employees of safe practices in meetings and give trainings when needed.
2. Provide hands-on training for young and new workers on properly using equipment
New or seasonal workers should be given thorough explanations on all tasks they will perform. This is especially important if a worker will be operating equipment in a warehouse or will be sent out on deliveries. Encourage workers to look out for one another and assist newer hires if needed.
3. Delivery services and warehouse workers should wear bright, visible clothing
Longer hours could mean more workers will work late nights or early mornings. For some workers, that could mean part or all of their shifts are done in the dark. Be sure all workers are wearing the proper clothing and safety gear in order to be sure they are visible in all conditions.
4. Prevent injuries by properly stacking materials and making sure workers stand clear when doors are opened for unloading
Stocking inventory or loading and unloading delivery trucks can be dangerous if workers are unaware of proper lifting and handling techniques. Workers should be trained on these proper techniques before handling heavy items. Remind workers to stand clear of opening doors when unloading delivery trucks, to prevent any materials that may have shifted around in transit from falling on and injuring a person.
5. Create a detailed and flexible staffing plan to help reduce workplace stress
Accommodating everyone’s time-off requests during the holidays can be difficult. And workers may experience heightened stress due to the increased workloads and tight deadlines. Be mindful of each person’s wellbeing, and avoid overworking them during the holidays. Encourage taking regular breaks, and provide access to mental health resources. Keeping a detailed schedule will also help avoid any confusion on busy or unusual days.
6. When large crowds are expected, prepare an emergency plan
The holiday season means many businesses—especially in the retail or community services industry—may experience an increase in visitors. Whether you are a landscaper at a shopping mall or providing meals and health services to the community, larger crowds bring unique safety hazards, from crowd control to fire or medical emergencies. It is important to have a clear and well-communicated emergency plan in place to deal with these situations.
7. Make sure entrance and exit location signs are visible
Employers should ensure that all workers are familiar with emergency exits and evacuation routes. An evacuation plan should also account for disabled individuals, so that everyone can leave safely if necessary. Use clear signage to mark first aid stations, entrances, and exits. A communication system—like an intercom—should also be put in place to quickly convey information in place of emergency.
8. Encourage workers to report any safety and health concerns
Foster a workplace culture that is open to the reporting of any workplace accidents or health concerns. Create a clear and accessible reporting process, and be sure all workers are made aware of that process at the start of their employment. Make it clear to workers that they will not suffer retaliation if they do report an issue. If an issue is reported, act on it promptly and effectively. Staying aware of and prepared for any potential hazards or health problems can be a huge benefit to you and your team in the long run.
9. Remember: Seasonal workers have the same rights as full-time workers
During this time, many businesses may hire seasonal employees to meet increased demand. But it is important to remember that seasonal workers are entitled to the same rights and protections as permanent employees. Seasonal workers should not be excluded from safety trainings or benefits, and should be treated the same as full-time workers.
By following OSHA’s nine tips for holiday worker safety, businesses can help keep employees safe, healthy, and organized through the holiday season. Proper safety training, emergency preparedness and fostering a climate of safety can help keep a business running smoothly through the holidays. More safety resources and trainings can be found on Rancho Mesa’s SafetyOne™ Platform.
OSHA Form Submission Time: A Refresh
Author, Megan Lockhart, Client Communications Coordinator, Rancho Mesa Insurance Services, Inc.
It's that time of the year again, when employers review their work-related injuries and illnesses from the past year and fill out their OSHA 300A Form. Companies in designated industries must electronically submit the 300A Form to OSHA by March 2nd, 2024. As this deadline swiftly approaches, let’s review further details of these requirements.
Author, Megan Lockhart, Client Communications Coordinator, Rancho Mesa Insurance Services, Inc.
It's that time of the year again, when employers review their work-related injuries and illnesses from the past year and fill out their OSHA 300A Form. Companies in designated industries must electronically submit the 300A Form to OSHA by March 2nd, 2024. As this deadline swiftly approaches, let’s review further details of these requirements.
In addition to the 300A, companies with 100 or more employees in high-hazard industries must also submit information from their form 300-Log of Work-Related Injuries and Illnesses and Form 301-Injury and Illness Incident Report to OSHA annually.
Furthermore, the 300A Form must also be posted in the workplace, visible to employees, from February 1st to April 30th. The Form 300A does not include personal information such as employee names for confidentiality.
Rancho Mesa clients can utilize the RM365 HRAdvantage™ portal to track their incidents and generate their OSHA 300A Summary along with generate a .csv file that can be used to upload their incident information to OSHA’s Injury Tracking Application (ITA).
Employers can electronically submit their injury and illness information via OSHA’s ITA. OSHA changed their login format as of January 2023, so those who have not logged in last year will need to create a new Login.gov account, using their same email address, to access the application.
The forms 300A, 300-Log of Work-Related Injuries and Illnesses and 301-Injury and Illness Incident Report, as well as instructions on how to fill them out can be found in the OSHA Forms for Recording Work-Related Injuries and Illnesses document.
For additional information and detailed instructions on creating a new account, please visit OSHA’s Injury and Reporting webpage.
Top 5 OSHA Violation Trends and Solutions
Author, Sam Clayton, Vice President, Construction Group, Rancho Mesa Insurance Services, Inc.
Every year, Federal OSHA conducts thousands of inspections and issues costly citations to companies. So, it is imperative for business owners and safety managers to be aware of the most common citations and how to avoid them through effective safety programs.
Author, Sam Clayton, Vice President, Construction Group, Rancho Mesa Insurance Services, Inc.
Every year, Federal OSHA conducts thousands of inspections and issues costly citations to companies. So, it is imperative for business owners and safety managers to be aware of the most common citations and how to avoid them through effective safety programs.
Back in September 2021, Rancho Mesa highlighted the top Cal/OSHA citations issued during the 2019/2020 reporting period in podcast Episode 136. Now that the 2023 Federal OSHA data is available, we can analyze the citations that were most common across the United States to see what’s changed and evaluate our safety programs to avoid being another statistic.
Although OSHA violations can be issued for numerous reasons, the most common five violation in 2023 were:
1. Fall Protection-General Requirements (Standard 1926.501)
This standard outlines where fall protection is required, which systems are appropriate for given situations, the proper construction installation of safety systems, and the proper supervision of employees to prevent falls. It is designed to protect employees on walking/working surfaces (horizontal or vertical) with an unprotected side or edge above 6ft.
There were 7,271 fall protection violations in 2023 up from 5,260 in
2022. To help avoid fall protection citations, take advantage of Rancho Mesa’s proprietary SafetyOne™ mobile app and website’s fall protection resources like the online awareness course, multiple toolbox talks, various risk observation checklists, and sample Fall Protection Program that is designed to reinforce the company’s policies.
2. Hazard Communication (Standard 1910.1200)
This standard addresses chemical hazards, both those chemicals produced in the workplace and those brought into the workplace. It also governs the communication of those hazards to workers.
There were 3,213 hazard communication violations in 2023. Proper hazard communication in construction environments can save lives. Consider utilizing the variety of hazard communication resources in our SafetyOne platform with online trainings, toolbox talks, and sample policies and checklists.
3. Ladders (Standard 923.1053)
This standard covers general requirements for all ladders.
There were 2,978 ladder violations in 2023, more than 800 more than 2022’s 2,143 violations. The RM365 Advantage Safety Star™ Program’s Ladder Safety module provides an in-depth practical overview of ladder safety from seasoned risk control experts. Utilize the SafetyOne platform’s online training courses, toolbox talks, risk observations and sample policies to ensure your employees are compliant with your company policy.
4. Scaffolding (Standard 1926.451)
This standard covers general safety requirements for scaffolding, which should be designed by a qualified person and constructed and loaded in accordance with that design. Employers are bound to protect construction workers from falls and falling objects while working on or near scaffolding at heights of 10ft or higher.
There were 2,859 scaffolding violations in 2023. Safety is everyone’s responsibility, so utilizing Rancho Mesa’s SafetyOne sample scaffold policy to provide a framework of best practices to help comply with OSHA Standard 1926.451. Reinforce your policy through toolbox talks, online courses and help prevent unsafe conditions with scaffold risk observations.
5. Powered Industrial Trucks (Standard 1910.178)
This section contains safety requirements relating to fire protection, design, maintenance and use of fork trucks, tractors, platform lift trucks motorized hand trucks and other specialized trucks powered by electric motors or internal combustion engines.
There were 2,561 violations in 2023. OSHA mandatory guidelines include operator training and certification, pre-shift inspections and operating environment restrictions. The best way to avoid these types of citations, is by using the risk observations in SafetyOne to document your equipment inspections. Ensure employees are trained by utilizing the toolbox talks and online training courses.
Rancho Mesa knows these top five citations can be avoided by reviewing safety programs often and ensuring they are effective. Clients can take advantage of the RM365 Advantage Safety Star™ Program that specifically addresses some of the most common citations.
To discuss your safety program, workers’ compensation or other insurance needs, contact me at (619) 937-0167 or sclayton@ranchomesa.com.
The Final Chapter: Addressing Training, Access and Recordkeeping in the IIPP
Author, Jack Marrs, Associate Account Executive, Rancho Mesa Insurance Services, Inc.
In this third installment of exploring an Injury and Illness Prevention Program (IIPP), we will be taking a closer look at: Providing employee training and instruction, procedures to allow employee access to the program, and recordkeeping and documentation.
Author, Jack Marrs, Associate Account Executive, Rancho Mesa Insurance Services, Inc.
In this third installment of exploring an Injury and Illness Prevention Program (IIPP), we will be taking a closer look at: Providing employee training and instruction, procedures to allow employee access to the program, and recordkeeping and documentation.
Providing Employee Training and Instruction
Providing clear and effective training for both employees and supervisors is essential for the success of an IIPP. All employees are required to be fully aware of the workplace hazards they may face. Comprehensive and well-conducted trainings can help reduce the likelihood of work-related injuries and illnesses. An article from The State Fund suggests “If you are unable to conduct your own required trainings, you should reach out to an outside consultant, Cal/OSHA consultation, vendors, your insurance carrier, and/or broker for assistance.” The more knowledgeable and prepared employees are, the safer the work environment becomes.
Take a look at the training resources that are available to your organization. Rancho Mesa clients can access the online safety training courses in the SafetyOne™ platform.
Procedures to Access the IIPP
All employees are required to have access to the written IIPP. This will ensure that all employees are fully aware of the safety protocols and hazard prevention strategies used to minimize workplace accidents and illnesses and thus, maintain a safe workplace.
According to Cal/OSHA, employers can meet this requirement by:
1. Unobstructed access through a company server or website, which allows employees to review, print, or email a copy of the IIPP
2. When requested, provide a printed copy of the IIPP (unless the employee agrees to receive an electronic copy)
The IIPP can be made accessible to users of the SafetyOne mobile app. It allows organizations to upload digital files into a file cabinet that is available only to their users. For employees who aren’t SafetyOne app users, they could scan a QR code or complete a webform to request the IIPP from their administrator. However your organization decides to distribute the IIPP, it should be easy for employees to access or request.
Recordkeeping and Documentation
Recordkeeping and proper documentation are crucial components of the IIPP. By maintaining accurate records, employers can learn from past incidents and identify injury and illness trends. This knowledge allows for necessary corrections and improvements in future operations, which will improve overall workplace safety. There are 5 steps required by the OSHA for a compliant recordkeeping system:
Each employer (unless exempt by size or industry) must record each fatality, injury, or illness that is work-related, is a new case, or meets one or more of the general recording criteria specified in Title 8, Section 14300.
Record each injury or illness on the Cal/OSHA Log of Occupational Work Related Injuries and Illnesses (Form 300) according to its instructions.
Prepare an Injury and Illness Incident Report (Form 301), or equivalent.
Annually review and certify the Cal/OSHA Form 300 and post the Summary of Work-Related Injuries and Illnesses (Form 300A) no later than February 1 and keep it posted where employees can see it until April 30.
Maintain the last five years of these records in your files.
A simple way to collect the incident information required for the OSHA logs (Form 300, 300A and 301) can be obtained by utilizing SafetyOne’s mobile forms. Either through the mobile app or via a QR Code or web link, employees can complete accident investigation forms and witness statements digitally. Then, the person responsible for documenting and maintaining the OSHA logs, can review the reports that came in through the mobile app and document the OSHA logs in the RM365 HRAdvantage Portal.
Rancho Mesa will host several webinars in the coming months to assist clients with understanding the best practices for completing their OSHA logs using SafetyOne™ and the RM365 HRAdvantage Portal.
Cal/OSHA has a Guide to Developing Your Workplace Injury and Illness Prevention Program that is helpful for organizations that need some assistance with getting started.
Rancho Mesa also has a 6-page Sample Injury and Illness Prevention Overview for California Employers available through our RM365 HRAdvantage Portal.
Following these steps is a proactive approach to building a safer working environment for all employees. The bottom line, it’s all about mitigating accidents before they happen and building a safe work environment.
Please contact me with any questions regarding the IIPP at (619)-486-6569 or via email at jmarrs@ranchomesa.com.
Safety Evolution: General Contractors Begin Requiring Safety Helmets Over Hard Hats
Author, Megan Lockhart, Client Communications Coordinator, Rancho Mesa Insurance Services, Inc.
The hard hat has long been a staple for construction-site safety. However, a new contender has entered the industry in 2023 as more and more general contractors are requiring safety helmets.
Author, Megan Lockhart, Client Communications Coordinator, Rancho Mesa Insurance Services, Inc.
The hard hat has long been a staple for construction-site safety. However, a new contender has entered the industry in 2023 as more and more general contractors are requiring safety helmets.
The safety helmet, while similar in form to the normal hard hat, includes added protection such as chin strap, face shield, and ear muffs. These new features allow for the helmet to sit more securely on the head while also protecting the ears from dangerously high noise levels and the eyes from possible debris.
“Since we made the switch to the new style hard hat, our employees don’t want to go back to the old-style hard hat,” Gilbane Building Company said. “This technology successfully removes the hazard of the hard hat falling off during a task, and wearing the face shield eliminates the possibility of forgetting to wear eye protection.”
While OSHA does not officially require the switch from hard hats to safety helmets, the topic was brought up at the Nation Association of Home Builders (NAHB) Spring Leadership Meeting in June 2023 in which director of OSHA’s Office of the Directorate of Construction, Scott Ketcham, granted insight on OSHA’s plans to improve jobsite safety with elevated standards for Personal Protective Equipment (PPE) in the near future.
“One initiative shared at the meeting is a pilot program for safety helmets meant to eventually replace hardhats as the preferred head protection in construction,” NAHB’s article about the meeting said. “Ketcham noted that 20% of head injuries in construction are the result of slips, trips, and falls and that hardhats do not protect against such injuries while helmets with chinstraps may stay on the head during a fall and offer protection.”
As PPE continues to evolve in the construction industry, it's important for subcontractors to be aware of what might be required of them on their job sites. Although no current laws require safety helmets over hard hats, Rancho Mesa will continue to offer updates as standards change.
OSHA Officially Rules for Expanded Recordkeeping Requirements for High-Hazard Industries
Author, Megan Lockhart, Client Communications Coordinator, Rancho Mesa Insurance Services, Inc.
Recently, the Occupational Safety and Health Administration (OSHA) made its final ruling to expand recordkeeping requirements for high-hazard industries, such as construction. The new requirements will take effect January 1, 2024 and will expand on what injury and illness information is needed to be electronically submitted to OSHA.
Author, Megan Lockhart, Client Communications Coordinator, Rancho Mesa Insurance Services, Inc.
Recently, the Occupational Safety and Health Administration (OSHA) made its final ruling to expand recordkeeping requirements for high-hazard industries, such as construction. The new requirements will take effect January 1, 2024 and will expand on what injury and illness information is needed to be electronically submitted to OSHA.
The requirements state that businesses with 100 or more employees in certain high-hazard industries must now electronically submit information from their Form 300-Log of Work-Related Injuries and Illnesses, as well as Form 301-Injury and Illness Incident Report to OSHA annually. This is in addition to Form 300A-Summary of Work-Related Injuries and Illnesses, which is already required.
Additionally, establishments are required to include their legal company name when making these submissions to OSHA from their injury and illness records.
Companies in high-hazard industries are already required to keep records of their work-related injuries and illnesses; however, this data is now to be submitted to OSHA, and the information gathered will be published on the OSHA website.
“OSHA will use these data to intervene through strategic outreach and enforcement to reduce worker injuries and illnesses in high-hazard industries,” Doug Parker, Assistant Secretary for Occupational Safety and Health, said in OSHA’s press release. “The safety and health community will benefit from the insights this information will provide at the industry level, while workers and employers will be able to make more informed decisions about their workplace's safety and health."
California businesses currently submit their recordkeeping information directly to Federal OSHA. Although the Cal/OSHA board has yet to release information regarding these new requirements, they must choose to uphold the standards set by Fed/OSHA or create stricter requirements. We will keep clients informed as further guidelines are announced.
Identifying Proper Procedures for the Injury and Illness Prevention Program
Author, Jack Marrs, Associate Account Executive, Rancho Mesa Insurance Services, Inc.
In this second installment of exploring an Injury and Illness Prevention Program (IIPP) we will be taking a closer look at the procedures for identifying and evaluating workplace hazards, investigating occupational injury or illnesses, and correcting unsafe or unhealthy conditions, work practices and procedures.
Author, Jack Marrs, Associate Account Executive, Rancho Mesa Insurance Services, Inc.
In this second installment of exploring an Injury and Illness Prevention Program (IIPP) we will be taking a closer look at the procedures for identifying and evaluating workplace hazards, investigating occupational injury or illnesses, and correcting unsafe or unhealthy conditions, work practices and procedures.
Identifying and Evaluating Workplace Hazards
Employers need to have proper measures in place to identify potential health and safety risks like unsafe conditions and practices within the workplace. These measures involve conducting regular inspections to identify any areas of the workplace that may be hazardous. Also, conducting interviews with employees is a great way to identify any potential workplace hazards. During this process it is important to document any identified hazards and create a plan of action to fix them.
According to California’s State Fund “Inspections should be conducted by personnel who, through experience or training, are able to identify actual and potential hazards and understand safe work practices. They should be knowledgeable in the Cal/OSHA safety orders that apply to your workplace to better help you identify potential hazards.”
Investigating Occupational Injuries or Illnesses
Referring now to the investigation that should take place after an accident or near miss has occurred. The investigation should be done by a trained employee who is able to identify the cause of the accident and understands what solutions need to be put in place to prevent a similar incident from happening in the future. When doing an investigation, it is crucial to fill out an investigation report containing the details about what happened. This information is used to not only identify root causes but much of the data that is collected will need to be documented on the OSHA logs. CAL/OSHA lists five important steps for proper recordkeeping:
Each employer (unless exempt by size or industry) must record each fatality, injury, or illness that is work-related, is a new case, or meets one or more of the general recording criteria specified by OSHA.
Record each injury or illness on the OSHA Form 300, according to its instructions.
Prepare an Injury and Illness Incident Report known as Form 301, or its equivalent.
Annually review and certify the OSHA Form 300 and post the Summary of Work-Related Injuries and Illnesses known as the Form 300A no later than February 1 and keep it posted where employees can see it until April 30.
Maintain the last five years of these records in your files.
Lastly, building an inventory of investigation reports can lead to a stronger ability to identify developing trends and root causes that could lead to additional incidents, if not corrected.
Correcting Unsafe or Unhealthy Conditions, Work Practices and Procedures
Once your safety team becomes aware of a hazard, it is imperative to take immediate action. If the hazard is not easily fixable, employees should vacate the work area until a solution is implemented. Once the solution is in place, only trained staff members should enter the hazardous area to address the issue. This approach ensures effective hazard management while minimizing the risks associated with its correction.
By implementing an effective Injury and Illness Prevention Program, workplaces will begin to fulfill their regulatory obligation of maintaining a safe workplace, but also create a culture of safety and accountability.
Our next installment will cover the last 3 critical components of the IIPP: providing employee training and instruction, procedures to allow employee access to the program, and recordkeeping and documentation.
Please contact me with any questions about managing your risk at (619) 486-6569 or via email at jmarrs@ranchomesa.com.
Implementing Best Practices when Hiring in the Construction Industry
Author, Casey Craig, Account Executive, Rancho Mesa Insurance Services, Inc.
With unemployment rates settling near 4 percent, it is becoming increasingly difficult to find the right employees to help grow your construction company. With most able-bodied workers having secure employment, this leads to having either apprentice-type employees that come with unique challenges or pulling from an aging workforce that can bring cumulative injuries and risks. Navigating these issues can be complex and there is not a perfect solution, but employer’s hiring practices need to change in order to keep up with the current state of the industry.
Author, Casey Craig, Account Executive, Rancho Mesa Insurance Services, Inc.
With unemployment rates settling near 4%, it is becoming increasingly difficult to find the right employees to help grow your construction company. With most able-bodied workers having secure employment, this leads to having either apprentice-type employees that come with unique challenges or pulling from an aging workforce that can bring cumulative injuries and risks. Navigating these issues can be complex and there is not a perfect solution, but employer’s hiring practices need to change in order to keep up with the current state of the industry.
When hiring new employees, consider:
Pre-hire drug testing
Pre-hire physicals
Targeted job postings with accurate description of daily work
Multiple levels of interviews
Simulating work at your office that potential new hires would be performing in the field
The US saw a unique shift in the workplace as a result of COVID-19 where employees felt their value skyrocket as fewer people were willing to work in-person. Employers were forced to increase wages to get bodies on jobsites. In prior years, it may have been enough to just rely on word of mouth and referrals to get new hires. Too often now, we are seeing new hires suffer “ghost injuries” that are quickly followed with letters of representation. These and similar types of cumulative trauma claims can have long term impacts on your experience rating (EMR). While these situations are difficult to prevent, using best practices and conducting thorough interviews with your prospective employees will allow you to make educated decisions which typically lead to better hires.
Taking advantage of the best practices listed above can help insulate your company from poor hiring decisions. Obviously, we would love for new hires to turn into long term employees, as onboarding and proper training can be a costly expense in both other employee’s time and payroll. In a recent survey conducted by Traveler’s Insurance, it was shown that 34% of workplace injuries occurred during the worker’s first year on the job. This can be from a combination of inexperience, overexertion, and/or lack of safety knowledge.
Consider these hiring and onboarding processes to assist in mitigating the glaring number of claims that are emanating from newer employees or employees that have limited experience on jobsites. The financial impact they can have on your company will impact your balance sheet for years and can be potentially avoided with implementing some of our recommended techniques
To learn more about improving your hiring practices or how Rancho Mesa can help to improve your process, reach out at (619) 438-6900 or ccraig@ranchomesa.com.
Properly Utilizing Tailgate Meetings
Author, Casey Craig, Account Executive, Rancho Mesa Insurance Services, Inc.
For many foremen and superintendents, weekly tailgate meetings can feel like a task that just needs to be checked off the list. However, while the purpose of these meetings is critical for the health and well-being of fellow field employees, the time required and repetitive nature of them can create challenges. To maximize the benefits of these meetings, construction firms must be proactive and thoughtful as they develop an inventory of topics.
Author, Casey Craig, Account Executive, Rancho Mesa Insurance Services, Inc.
For many foremen and superintendents, weekly tailgate meetings can feel like a task that just needs to be checked off the list. However, while the purpose of these meetings is critical for the health and well-being of fellow field employees, the time required and repetitive nature of them can create challenges. To maximize the benefits of these meetings, construction firms must be proactive and thoughtful as they develop an inventory of topics.
Identifying Tailgate Meeting Topics
Take ample time with your sales team to understand the scope of your backlog to see where hazards may appear within these projects. Plan training topics with an eye on the weather, paying close attention to historically warm or cold months. Consider connecting with your insurance broker as well on recent injury trends that you can address with the crew.
This will be pertinent as your company approaches their renewal window with underwriters looking at claims history. They commonly ask, “what has the insured done to make sure these claims don’t happen again?” Learning from your past is key to being proactive. Knowing you will have certain exposures coming up and addressing those with preventative training topics begins to build a Best Practice Safety Program.
Accessing Content for Training
Locating “Toolbox” trainings can be time consuming and, in some cases, costly. And very often, the trainings may not be applicable to your operation and/or the trends you may need to focus on. With an eye to the future, Rancho Mesa has recently introduced a proprietary SafetyOne™ App. Safety managers will be able to document safety inspections from their mobile device and assign required fixes to employees, while also tracking when they have been completed. Meeting content can also be distributed to supervisors through their mobile device all with a focus of making safety meetings more efficient and effective. These same supervisors can now access a vast library that can be customized to their operation.
Reach out to me to learn more about the SafetyOne™ App and how Rancho Mesa can partner with you and your team moving forward. You can reach me at (619) 438-6900 or email me at ccraig@ranchomesa.com
Construction Death Rate Not Decreasing as Expected
Author, Casey Craig, Account Executive, Rancho Mesa Insurance Services, Inc.
With the heightened safety regulations and OSHA guidelines over the past decade, many would think we are working in a much safer environment with fewer fatalities. Despite the rising number of employees and using a standard based off deaths per 100,000 employees, the data is showing that the number of fatalities are the same as they were a decade ago.
Author, Casey Craig, Account Executive, Rancho Mesa Insurance Services, Inc.
With the heightened safety regulations and OSHA guidelines over the past decade, many would think we are working in a much safer environment with fewer fatalities. Despite the rising number of employees and using a standard based off deaths per 100,000 employees, the data is showing that the number of fatalities are the same as they were a decade ago.
With a much larger workforce, OSHA is severely understaffed compared to the previous decade. The agency does not have enough inspectors to visit nearly enough jobsites. They have been more reactive in the sense that they are imposing fines on companies after they have had losses. These fines represent a fraction of what it would take to motivate construction companies to revamp their respective safety programs. Employers have factored these fines into the cost of business to a certain extent.
OSHA is now contemplating whether it is worth doubling the jobsite inspections annually and/or increase fines drastically. There is no solid data to link an increase in jobsite inspections to fewer fatalities, so the logical answer would be heavier fines and a push for more negligent death claims to be criminally prosecuted.
Either of these options will lead to more oversite or more fines for the construction industry as a whole. One critical approach you can take is to prepare yourself as a business owner. Be proactive. Consider working with the consultation branch of OSHA to visit your operation and jobsites. This division within OSHA does not issue fines or violations. They do, however, offer recommendations and advice on how to make your operation safer. With the potential of OSHA’s fines increasing, it is time to make sure that your company is on the forefront of safety. A great first step is reaching out to your insurance broker to help you meet requirements and push you to exceed. With a potential recession looming, it is important to make sure you have insulated your company from risk, so you have the best chance at thriving.
If you have any urgent questions on this topic, you can reach me directly at (619) 438-6900 or email me at ccraig@ranchomesa.com.
OSHA Proposes to Expand Electronic Form Submission Requirements
Author, Lauren Stumpf, Media Communications & Client Services Specialist, Rancho Mesa Insurance Services, Inc.
The Occupational Safety and Health Administration (OSHA) recently released a proposed rule that would increase electronic reporting requirements for businesses summiting OSHA logs.
Author, Lauren Stumpf, Media Communications & Client Services Specialist, Rancho Mesa Insurance Services, Inc.
The Occupational Safety and Health Administration (OSHA) recently released a proposed rule that would increase electronic reporting requirements for businesses summiting OSHA logs.
Currently, establishments with 250 or more employees, regardless of classification, and establishments with 20-249 employees, classified in certain high hazard industries, must electronically submit their Form 300A Summary to OSHA, annually.
The proposed rule changes would declare that only those in the classified high-hazard industries with 100 or more employees will be required to submit their Form 300A Summary electronically to OSHA. It would also require that Forms 300 and 301 be submitted electronically by these companies, when previously these two forms were to be kept confidential and only available to OSHA upon request.
Classified high hazard establishments with 20-99 employees would still only be required to submit the 300A Summary electronically to OSHA and would not need to electronically submit the 300 and 301 forms.
Under the proposed rule, OSHA would update the industries that are classified as high hazard and need to submit the data electronically.
OSHA has also proposed that company names be included on the electronic submissions. This, along with the injury and employee information that is included on the 300 and 301 forms, raises privacy concerns because this information would be available for public view via the Freedom of Information Act (FOIA).
The comment period for the public to voice their concerns ends on May 31, 2022. Information on how to submit comments on the proposed rule can be on the Federal Register.
Understanding the DART and TCIR Calculations
Author, Lauren Stumpf, Media Communications and Client Services Specialist, Rancho Mesa Insurance Services, Inc.
When a project owner asks you to provide the company’s DART or TCIR rate, it may seem a little overwhelming at first. But, the two numbers are really a score that can be used to compare contractors’ safety history. These numbers can be important during the bidding process when comparing multiple bids and could be a determining factor for who is awarded the contract.
Author, Lauren Stumpf, Media Communications and Client Services Specialist, Rancho Mesa Insurance Services, Inc.
When a project owner asks you to provide the company’s DART or TCIR rate, it may seem a little overwhelming at first. But, the two numbers are really a score that can be used to compare contractors’ safety history. These numbers can be important during the bidding process when comparing multiple bids and could be a determining factor for who is awarded the contract.
DART stands for days away, restricted, or transferred. A DART rate is used to track any OSHA recordable workplace injury or illness that result in days away from work, restricted duty, or transfer of duties.
On the other hand, the TCIR is the total case incident rate (also known as the Total Recordable Incident Rate or sometimes referred to as the OSHA Incident Rate). It measures a company's past safety performance based on their incident rate. A TCIR is found by looking at the number of work-related injuries per 100 full-time workers during a one-year period.
The TCIR will likely be higher than the DART because it includes all incidents, not just the ones that results in lost time.
Project owners are increasingly requesting these numbers along with the project bid. Not only do they want to see how much it’s going to cost them to build the project, but they want to know how safe their contractor is on the jobsite. These numbers show that.
OSHA also uses these calculations to monitor high-risk industries.
Rancho Mesa’s Risk Management Center features a tool that helps contractors generate their DARTs and TCIRs. Contractors can use the Incident Track application to enter and track an incident’s details. Once that incident has been saved, the system will allow them to generate OSHA logs based on that data and generate the DART and TCIR.
“It’s an easy-to-use tool that ensures the numbers are accurate and available whenever they’re needed,” said Alyssa Burley, Media Communications and Client Services Manager with Rancho Mesa Insurance Services, Inc.
To learn more about the Risk Management Center’s capabilities, sign up for an upcoming webinar at www.ranchomesa.com/workshops-and-webinars.
Top 5 OSHA Violations for 2021
Author, Sam Clayton, Vice President, Construction Group, Rancho Mesa Insurance Services, Inc.
Every year, Federal OSHA conducts thousands of inspections and issues costly citations to companies. So, it is imperative for business owners and safety managers to be aware of the most common citations and how to avoid them through effective safety programs.
Author, Sam Clayton, Vice President, Construction Group, Rancho Mesa Insurance Services, Inc.
Every year, Federal OSHA conducts thousands of inspections and issues costly citations to companies. So, it is imperative for business owners and safety managers to be aware of the most common citations and how to avoid them through effective safety programs.
Back in September 2021, Rancho Mesa highlighted the top Cal/OSHA citations issued during the 2019/2020 reporting period in podcast Episode 136. Now that the 2021 Federal OSHA data is available, we can analyze the citations that were most common across the United States to see what’s changed and evaluate our safety programs to avoid being another statistic.
Although OSHA violations can be issued for numerous reasons, there are 5 citations that continue to show up on the list year after year, though their order may change slightly.
Fall Protection, General Requirements (29 CFR 1926.501)
This Standard outlines where fall protection is required, which systems are appropriate for given situations, the proper construction installation of safety systems, and the proper supervision of employees to prevent falls. It is designed to protect employees on walking/working surfaces (horizontal or vertical) with an unprotected side or edge above 6ft.There were 5,295 fall protection violations in 2021. To help avoid fall protection citations, take advantage of Rancho Mesa’s fall protection resources like the online awareness course and safety videos, a webinar on how to implement a fall protection and prevention plan, along with a library of fall protection training shorts (i.e., tailgate talks) that are designed to reinforce the company’s policies.
Respiratory Protection, General Industry (29 CFR 1910.134)
This standard directs employers on establishing or maintaining a respiratory protection program. It lists requirements for program administration, worksite specific procedures, respirator selection, employee training, fit testing, medical evaluation, respirator use, cleaning, maintenance and repair.There were 2,527 respiratory protection violations in 2021. The best way to avoid these types of citations is through training and documentation. Rancho Mesa’s Personal Protection Equipment (PPE) for Management and Respiratory Protection courses address implementing and enforcing the PPE program and information the employee needs to know about their respiratory protection, respectively.
Ladders, Construction (29 CFR 1923.1053)
This standard covers general requirements for all ladders.There were 2,026 ladder violations in 2021. The RM365 Advantage Safety Star™ Program’s Ladder Safety module provides an in-depth practical overview of ladder safety from seasoned risk control experts.
Scaffolding, General Requirements, Construction (29 CFR 1926.451)
This standard covers general safety requirements for scaffolding, which should be designed by a qualified person and constructed and loaded in accordance with that design. Employers are bound to protect construction workers from falls and falling objects while working on or near scaffolding at heights of 10ft or higher.There were 1,948 scaffolding violations in 2021. Safety is everyone’s responsibility, so utilizing Rancho Mesa’s scaffolding online course and safety videos to provide a general awareness of best practices to all employees is a proactive way to help comply with OSHA regulation 29 CFR 1926.451.
Hazard Communication Standard, General Requirements (29 CFR 1910.1200)
This standard addresses chemical hazards, both those chemicals produced in the workplace and those brought into the workplace. It also governs the communication of those hazards to workers.There were 1,947 hazard communication violations in 2021. Proper hazard communication in construction environments can save lives. Consider utilizing the variety of hazard communication resources in the Risk Management Center like online courses for both employees and management along with video training specific to hazard communication in construction environments and a sample Hazard Communication Program template.
Rancho Mesa knows these top five citations can be avoided by reviewing safety programs often and ensuring they are effective. Clients can take advantage of the RM365 Advantage Safety Star™ Program that specifically addresses some of the most common citations.
To discuss your safety program, workers’ compensation or other insurance needs, contact me at (619) 937-0167 or sclayton@ranchomesa.com.
Cal/OSHA Adopts Revised ETS Through April 2022
Author, Alyssa Burley, Media Communications and Client Services Manager, Rancho Mesa Insurance Services, Inc.
On Thursday, December 16, 2021, the Cal/OSHA Standards Board voted in favor, 6 to 1, of adopting the revised COVID-19 Prevention Emergency Temporary Standard (ETS). This is the third iteration of the ETS since it originally went into effect in November 2020 and it happens to be the second and final re-adoption that’s allowed.
Author, Alyssa Burley, Media Communications and Client Services Manager, Rancho Mesa Insurance Services, Inc.
On Thursday, December 16, 2021, the Cal/OSHA Standards Board voted in favor, 6 to 1, of adopting the revised COVID-19 Prevention Emergency Temporary Standard (ETS). This is the third iteration of the ETS since it originally went into effect in November 2020 and it happens to be the second and final re-adoption that’s allowed.
The newly adopted revised ETS goes into effect on January 14, 2022 when the current ETS expires, and it will be in effect until April 14, 2022, at which time the temporary standard must expire or Cal/OSHA has to adopt a permanent standard in order to keep some sort of COVID-related standard in place.
Based on the discussions at the Cal/OSHA Standards Board’s December 16th meeting, it looks like Cal/OSHA is moving forward with proposing a permanent COVID-19 standard in March or April 2022. So, we’ll keep an eye on that.
Changes to Cal/OSHA’s COVID-19 Prevention Emergency Temporary Standard:
COVID-19 TEST
Starting January 14, 2022, there is a new definition for what is considered a “COVID-19 test” to account for over-the-counter tests that are now readily available. The new definition specifically says if you’re using an over-the-counter test, it cannot be both self-administered and self-read unless observed by the employer or an authorized telehealth proctor.
So, if an employee wants to use an over-the-counter COVID-19 rapid antigen test, they’ll need to either have the employer or an authorized telehealth proctor witness the test being performed and the results generated. This is really to prevent employees from providing false results to employers.
FACE COVERINGS
The new ETS also provides more details about what types of face coverings are now allowed and what’s not. Acceptable face coverings include surgical masks, a medical procedure mask, a respirator worn voluntarily, or a tightly woven fabric or non-woven material of at least two layers that does not let light pass through when held up to a light source. There are exceptions for clear face coverings when worn strictly for accommodations purposes. Coverings must be secured to the head with ties, ear loops or elastic bands that go behind the head.
This means many of the cloth masks that are currently being used by employees will no longer be acceptable under this new standard. Scarfs, ski masks, bandanas and other make-shift face coverings will not be permitted.
FULLY VACCCINATED
The definition of “fully vaccinated” has changed a bit. The new language recognizes those who may have gotten their first dose of a two-dose vaccine series from one manufacturer and the second dose from another manufacturer.
WORKSITE
Another change is the definition of “worksite.” The new ETS clarifies that a worksite does not include locations where the employee does not have exposure to other employees.
For example, if the employee is working from their home office, it would not be considered a worksite for ETS noticing purposes, nor would an office where the employee works by themselves and never is exposed to other employees.
TESTNG AFTER WORKSITE COVID-19 EXPOSURE
There are new requirements for testing employees after a COVID-19 exposure in the workplace. Regardless of vaccination status, employers must now offer testing to all employees who have had a close contact with a COVID-19 case in the workplace, regardless of their vaccination status.
Prior to the revised ETS, employers did not have to offer testing to vaccinated employees who were exposed. This change is a result of break through cases in those who are fully vaccinated. The only exception for not offering close contacts testing, is for those who have recovered from COVID-19 within the past 90 days and do not have symptoms.
RETURN TO WORK
Another change for vaccinated employees includes wearing a face covering in the workplace in lieu of a quarantine. While those employees who are vaccinated do not need to quarantine if they have had a close contact with a COVID-19 case, as long as they are asymptomatic and test negative, they can return to the workplace, but must wear a face covering and social distance for 14 days following the last date of close contact. This rule also applies to those who have recovered from COVID-19 within the last 90 days and are asymptomatic.
For those who are unvaccinated and have had a close contact with a COVID-19 case, as long as they test negative and are asymptomatic, they can return to the workplace after a 10-day quarantine, however, they must social distance and wear a face covering for 14 days.
There is a 7-day quarantine option for unvaccinated employees that are asymptomatic if they test negative at least five days after the close contact. In this situation, the employee must maintain social distancing and wear a face covering.
TESTING DURING AN OUTBREAK
As for changes to how to handle testing as a result of an outbreak, vaccinated employees can no longer be excluded from being offered testing if there are three or more employee COVID-19 cases within an exposed group. So, employers just need to make sure they’re offering testing to both vaccinated and unvaccinated employees if they’ve had a close contact or were in an exposed group during an outbreak.
One last thing to consider, while Cal/OSHA’s revised ETS does not take into consideration the federal vaccination or weekly testing mandates, nor other state and local requirements, we recommend that you consult your local and state health departments for additional requirements.
Rancho Mesa will make available an updated COVID-19 Prevention Program template that incorporates the modifications, as soon as possible.
Visit www.RanchoMesa.com/covid-19 for all our COVID-related articles, podcast episodes, sample COVID-19 Prevention Program Templates, and links to insurance carriers, the CDC and other agencies.
Top Five Workers’ Compensation Claims That Impact a MEP’s Bottom Line
Author, Amber Webb, Account Executive, Rancho Mesa Insurance Services, Inc.
If you are an MEP contractor who wants to impact both your productivity and profitably, then the following is crucial for your success. Our MEP Group at Rancho Mesa understands the importance of identifying the top five workers’ compensation claims that impact your industry while providing pertinent resources to help mitigate that risk.
Author, Amber Webb, Account Executive, Rancho Mesa Insurance Services, Inc.
If you are a Mechanical, Electrical & Plumbing (MEP) contractor who wants to impact both your productivity and profitably, then the following is crucial for your success. Our MEP Group at Rancho Mesa understands the importance of identifying the top five workers’ compensation claims that impact your industry while providing pertinent resources to help mitigate that risk. By working with leading workers’ compensation carriers and the Occupational Safety and Health Administration (OSHA), we identified the top 5 workers’ compensation claims affecting the MEP industry:
Cut/Puncture/Scrape/Lacerations
Slip/Falls from both same level and ladders/scaffolding
Strains from lifting/handling/pushing/pulling
Struck by object/Foreign Body in Eye
Motor Vehicle Accident (injured employee)
With employee safety at the forefront of your operations, understanding where the claims are likely to come from and then having the support and tools in place to address those concerns is vital to your long term success. When injuries occur on the job, it impacts not only the life of the injured worker and their family but will directly impact the productivity and profitability of the project.
For our clients to proactively mitigate these exposures, we provide them with access to specific trainings related to these top MEP claims and OSHA citations from our Risk Management Center Library. Our Client Services team then works closely with our clients to customize their trainings while meeting their specific risk management needs.
If you are not already a Rancho Mesa client, and would like a free trial of our Risk Management Center, please complete the form or contact Amber Webb at (619) 486-6562 or awebb@ranchomesa.com.
OSHA Issues ETS Addressing Mandatory COVID-19 Vaccination or Testing
Author, Sam Clayton, Vice President, Construction Group, Rancho Mesa Insurance Services, Inc.
Last week, the U.S. Department of Labor’s Occupational Safety and Health Administration (OSHA) announced a new emergency temporary standard (ETS) to protect more than 84 million workers from the spread of the coronavirus on the job.
Author, Sam Clayton, Vice President, Construction Group, Rancho Mesa Insurance Services, Inc.
Update: November 16, 2021 - Since the original publication of this article, OSHA announced it “has suspended activities related to the implementation and enforcement of the ETS pending future developments in the litigation.”
Recently, the U.S. Department of Labor’s Occupational Safety and Health Administration (OSHA) announced a new Emergency Temporary Standard (ETS) to protect more than 84 million workers from the spread of the coronavirus on the job.
Under the ETS standard, employers must develop, implement and enforce a mandatory COVID-19 vaccination policy, unless they adopt a policy requiring employees to be either vaccinated or undergo weekly COVID-19 testing and wear a face covering at work.
The emergency temporary standard covers employers with 100 or more employees and provides options for compliance. The standard also requires employers to provide paid time to workers to get vaccinated and to allow paid leave to recover from any side effects from the vaccination.
The ETS requires employers to:
Determine the vaccination status of employees, obtain acceptable proof of vaccination and maintain records and a roster of each employee’s vaccination status.
Require employees to provide prompt notice when they test positive for COVID-19 or receive a COVID-19 diagnosis. Employers must then remove the employee from the workplace, regardless of vaccination status. Employers must not allow them to return to work until they meet required criteria.
Ensure each worker who is not fully vaccinated is tested for COVID-19 at least weekly (if the employee is in the workplace at least once a week) or within 7 days before returning to work (if the employee is away from the workplace for a week or longer).
Ensure that each employee who has not been fully vaccinated wears a face covering when indoors or when occupying a vehicle with another person for work purposes.
The ETS does not require employers to pay for testing. However, employers may be required to pay for testing to comply with other laws, regulations, collective bargaining agreements. So, check with state and local jurisdictions for requirements.
The ETS is effective immediately upon its publication in the Federal Register, which took place on Friday, November 5, 2021. Employers must comply with most requirements within 30 days of publication and with testing requirements within 60 days of publication, or January 4th of 2022.
While more than half of the states are challenging the legality of federal OSHA’s ability to enforce the new ETS requirements, it is likely that individual states with their own OSHA State Plans (i.e., Alaska, Arizona, California, Hawaii, Indiana, Iowa, Kentucky, Maryland, Michigan, Minnesota, Nevada, New Mexico, North Carolina, Oregon, South Carolina, Tennessee, Utah, Vermont, Virginia, Washington, and Wyoming) will eventually adopt the new ETS as their own with or without modifications.
California’s State Plan (Cal/OSHA) implemented the most stringent COVID-19 ETS in the country months before federal OSHA released its original COVID-19 ETS that only applied to the health care industry.
Employers of all sizes should pay close attention to not only what federal OSHA’s ETS requires, but also requirements issued by state and local municipalities. Once your state adopts a COVID-19 ETS, be sure to also check your local ordinances, as some counties and cities are requiring additional measures.
If your state has not yet adopted the new federal OSHA ETS, which applies to our California clients, we recommend you start thinking about a game plan and maybe an alternate plan depending on whether your State Plan decides to adopt the ETS as it has been published or if they decide to adopt a more stringent ETS. You will want to consider the following:
Will you, as the employer, require all employees to be vaccinated?
Who will manage the vaccination records and the ongoing paperwork?
If testing is offered as an alternative to a vaccine, who will pay for testing (the employer or employee)?
If testing is offered as an alternative to a vaccine, will the company specify which type of test will be acceptable (PCR or Antigen)? Either is allowed, but the antigen tests must be proctored by a medical professional (virtually is allowed) or witnessed by the employer (for the over-the-counter home test). Who will administer the weekly tests?
As we learn more, Rancho Mesa will provide guidance and resources to mitigate risk in the workplace.
For questions about mitigating your risks, contact me at (619) 937-0167 or sclayton@ranchomesa.com.
How Janitorial Firms Can Avoid OSHA Fines
Author, Jeremy Hoolihan, Account Executive, Rancho Mesa Insurance Services, Inc.
Avoiding government standards in the janitorial industry can be costly in the event of an unexpected OSHA visit or after a serious injury. In an industry that generally has lean profit margins, OSHA fines could be detrimental to the stability of the business. Knowing the most common OSHA violations and protecting your business from them can help insulate your organization from costly fines while also keeping your company safe. Here are five of the most common OSHA violations in the janitorial industry and strategies to avoid potential fines.
Author, Jeremy Hoolihan, Account Executive, Rancho Mesa Insurance Services, Inc.
Avoiding government standards in the janitorial industry can be costly in the event of an unexpected OSHA visit or after a serious injury. In an industry that generally has lean profit margins, OSHA fines could be detrimental to the stability of the business. Knowing the most common OSHA violations and protecting your business from them can help insulate your organization from costly fines while also keeping your company safe. Here are five of the most common OSHA violations in the janitorial industry and strategies to avoid potential fines.
Hazard Communication Standard:
A hazard communication standard requires that all cleaning businesses provide written information to their employees about hazardous chemicals used in the course of business and stored on site. The employer is required to label all chemicals with information relating to its hazard classification, and the employer must maintain safety data sheets (SDS) at each jobsite. In addition to having this information available, the employer is also responsible for training the employees on the proper handling of each chemical before they begin using it. Having a hazard communication standard in place can help you avoid an OSHA fine while also creating a safe work environment.
Proper Use of Personal Protective Equipment (PPE):
It is critical that all janitorial staff is trained on the proper use of PPE. PPE can help protect employees against harmful exposures that occur while performing their normal duties. Examples of PPE include gloves, masks, safety glasses, and back braces. Proper training on the use of PPE should be done with each employee and documented in their employee file. Supervisors should monitor the use of PPE by employees to ensure consistent use. If employees are seen not wearing the proper PPE for the task at hand, this should be addressed verbally, and in writing to minimize future injuries. Serious injuries and OSHA fines are avoidable if the proper use of PPE is taught and monitored.
Slip, Trips, and Falls:
One of the most common injuries in the janitorial industry comes from slips and falls. Some falls can result in serious injuries, workers’ compensation claims, lawsuits, and OSHA fines. The most common slip and fall hazard is from wet floors, typically while mopping. These wet floors not only pose a problem for janitors, they are also a huge concern for the general public. Common ways to avoid these types of injuries include using caution cones to alert people of the wet surfaces, closing off areas that are being cleaned, and mopping areas after hours when there is less foot traffic. Using caution cones and proper signage can warn others of wet surfaces to avoid serious injuries and OSHA fines.
Bloodborne Pathogen Standard:
For those janitorial businesses that work within a healthcare setting, it is imperative that they follow the Bloodborne Pathogen Standard. This policy establishes an easy and safe way to handle blood and other bodily fluids. If you work in a setting where blood contact is common, it is important that you have the proper training. Otherwise, it could result in an OSHA citation.
Record Keeping:
Proper record keeping is critical if and when your firm is presented with an unexpected OSHA visit. Keeping updated records such as your injury & illness protection program, safety data sheets, documented employee training, and employee handbooks can help avoid common administrative fines.
Organizing and implementing these strategies can be overwhelming for many janitorial companies that may not have the resources for full-time human resources directors and/or safety coordinators. Through the Risk Management Center, Rancho Mesa and MaintenanceOne™ offers clients the tools and programs that can proactively manage these risks and the documentation required to be prepared when OSHA knocks on your door. Reach out Jeremy Hoolihan at jhoolihan@ranchomesa.com or 619-937-0174 to learn more about how we can assist you.
Top Five OSHA Citations the Tree Care Industry Should Avoid
Author, Rory Anderson, Account Executive, Rancho Mesa Insurance Services, Inc.
Every year, Federal OSHA conducts hundreds of inspections and issues costly citations to tree care companies. Although the Occupational Health OSHA citations can be issued for many reasons, there are five specific citations that continually plague the tree care industry every year.
Author, Rory Anderson, Account Executive, Rancho Mesa Insurance Services, Inc.
Every year, Federal OSHA conducts hundreds of inspections and issues costly citations to tree care companies. Although the Occupational Health OSHA citations can be issued for many reasons, there are five specific citations that continually plague the tree care industry every year.
1. Violation of standard 1910.132, PPE General Requirements
Employers of tree care companies can be cited for a violation if they fail to assess the workplace hazards, don’t provide personal protective equipment and fail to train employees on when and how to use it.
Average penalty: $1,300
2. Violation of standard 1910.1200, Hazard Communication
This citation is served if the employer lacks a hazard communication program for hazardous substances such as gas or hydraulic fluid periodically encountered in the tree care workplace.
Average penalty: $454
3. Violation of standard 5(a)(1), OSHA General Duty Paragraph
This is when an employer fails to provide a workplace free of recognized hazards. OSHA did not have a standard to describe the hazards specifically encountered in the tree care industry, but general duty citations usually cite passages from the ANSI Z133 standard.
Average penalty: $2,992
4.Violation of standard 1910.67, Vehicle-mounted Elevating and Rotating Work Platforms (e.g., bucket trucks and aerial lifts).
This citation can be issued if the employer fails to provide fall protection for the lift operator or fails to properly inspect the lift.
Average penalty: $3,325
5. Violation of standard 1910.135, Head Protection
This citation occurs when the employer fails to ensure that employees wear hard hats when required.
Average penalty: $1,262
As a tree care company, it is important that employee trainings routinely cover these five topics. While the standard safety training topics for the tree care industry are impactful (e.g., fall protection, chainsaw safety, etc.) and vital to your company’s safety success, these top five OSHA citations should be considered a high priority for regular review.
Access these specific trainings from our Risk Management Center library. If you’re not a Rancho Mesa client, please contact me at (619) 486-6437 or randerson@ranchomesa.com for a free Risk Management Center trial.
ANSI Releases New Mobile Elevating Work Platforms Standards
Author, Casey Craig, Account Executive, Rancho Mesa Insurance Services, Inc.
Last year, the American National Standards Institute (ANSI) updated their aerial lift standard, starting with renaming it Mobile Elevating Work Platforms (MEWP). This has been in the works since 2018 and is designed to align training, certifications, and equipment used on a more universal standard. According to the Center for Construction Research and Training (CPWR), roughly 26 people die from MEWP each year. This prompted the Occupational Safety and Health Administration (OSHA) to increase training requirements to keep accidents to a minimum. Obviously, MEWP are essential for completing a wide variety of construction jobs. So, what should you, as a business owner, be doing to ensure your employees are safe and in compliance when OSHA comes by your jobsites?
Author, Casey Craig, Account Executive, Rancho Mesa Insurance Services, Inc.
Last year, the American National Standards Institute (ANSI) updated their aerial lift standard, starting with renaming it Mobile Elevating Work Platforms (MEWP). This has been in the works since 2018 and is designed to align training, certifications, and equipment used on a more universal standard. According to the Center for Construction Research and Training (CPWR), roughly 26 people die from MEWP each year. This prompted the Occupational Safety and Health Administration (OSHA) to increase training requirements to keep accidents to a minimum. Obviously, MEWP are essential for completing a wide variety of construction jobs. So, what should you, as a business owner, be doing to ensure your employees are safe and in compliance when OSHA comes by your jobsites?
MEWP are prone to tipping over on uneven ground and in inclement weather conditions, if equipment is extended out. The most common cause of the MEWP tipping over is driving it over uneven surfaces. Understandably, many contractors rush to complete projects but moving extended lifts can be the easiest way to have a serious accident. Alternatively, taking proper time to lower a lift before moving it leads to fewer serious accidents.
Identifying exposures and objects that conflict with a lift’s surroundings is also of great concern for lift operators. A very common occurrence involves employees being pinned between the lift and an object. It is easy to become fixated on either the ground or the direction the lift is moving and ”miss” objects that could be hazardous as you are raising and lowering the lift. Allowing for time to plan ahead and move the machinery safely is immensely important.
Many of these new requirements are focused on teaching proper equipment use and creating an awareness of the changes to new equipment in the marketplace. Inherently, these machines are dangerous but necessary. So, maintaining a respect for them and understanding how to properly use them is vital. Lift use trainings, techniques, and protocol are available through our Risk Management Center and are compliant with the new ANSI/SAIA A92.20, A92.22, and A92.24 standards that were just released, last year.
Please reach out to me at ccraig@ranchomesa.com or call at 619-937-0164 for more information, or for help assigning the trainings.
Californians Wait for Revised COVID-19 Prevention Emergency Temporary Standards
Author, Alyssa Burley, Media Communications and Client Services Manager, Rancho Mesa Insurance Services, Inc.
Over the past few weeks, Californians have eagerly awaited news from the State’s Occupational Safety and Health Standards Board (Standards Board) on revisions to Cal/OSHA’s COVID-19 Prevention Emergency Temporary Standards after the Centers for Disease Control (CDC) released its latest guidance that ease mask wearing for those who are fully vaccinated.
Author, Alyssa Burley, Media Communications and Client Services Manager, Rancho Mesa Insurance Services, Inc.
Over the past few weeks, Californians have eagerly awaited news from the State’s Occupational Safety and Health Standards Board (Standards Board) on revisions to Cal/OSHA’s COVID-19 Prevention Emergency Temporary Standards after the Centers for Disease Control (CDC) released its latest guidance that ease mask wearing for those who are fully vaccinated.
On June 3, 2021, the seven-member Standards Board first voted to deny a revised set of standards that would place additional requirements on business owners and most notably prevent fully vaccinated employees from being able to take off their masks in the workplace if everyone in the room was not vaccinated. However, in the same meeting, the Standards Board voted a second time which led to the approval of the revised standards which were set to go into effect no later than June 15, 2021 when the State is scheduled to fully reopen.
With pressure from businesses, community groups and California Governor Gavin Newsom, the Standards Board held an emergency meeting on June 9, 2021, where they unanimously voted to rescind the proposed standards previously approved on June 3, 2021.
If all of this sounds confusing, you are not alone.
As of the publication of this article on June 15, 2021, business owners should be following the COVID-19 Prevention Emergency Temporary Standards that were adopted in November 2020 and May 3, 2021’s Executive Order N-84-20 which allows for fully vaccinated people who have been exposed to a COVID-19 case, but show no symptoms, to remain in the workplace. Rancho Mesa has created a COVID-19 Prevention Plan template based on those requirements. It is available for download.
The Standards Board is scheduled to meet on June 17, 2021 where it is expected they will propose new standards that are more in line with the CDC’s masking recommendations. The agenda provides information on how to attend the virtual meeting.
When changes are made to the COVID-19 Prevention Emergency Temporary Standards, Rancho Mesa will update its COVID-19 Prevention Plan template and make it available to the public.
Stay up to date on this issue and others that affect California businesses by subscribing to our weekly Risk Management Newsletter and podcast.