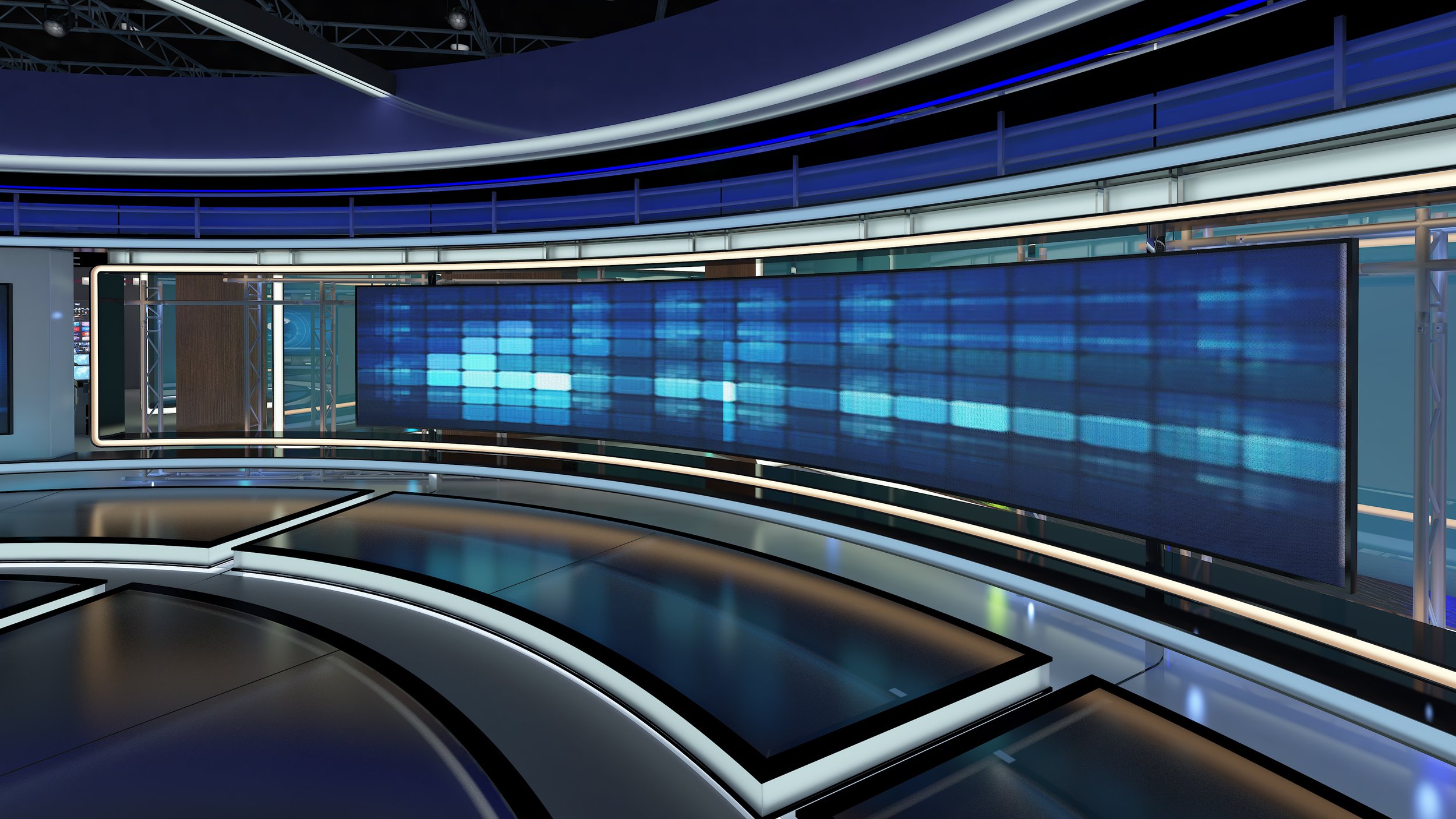
Industry News
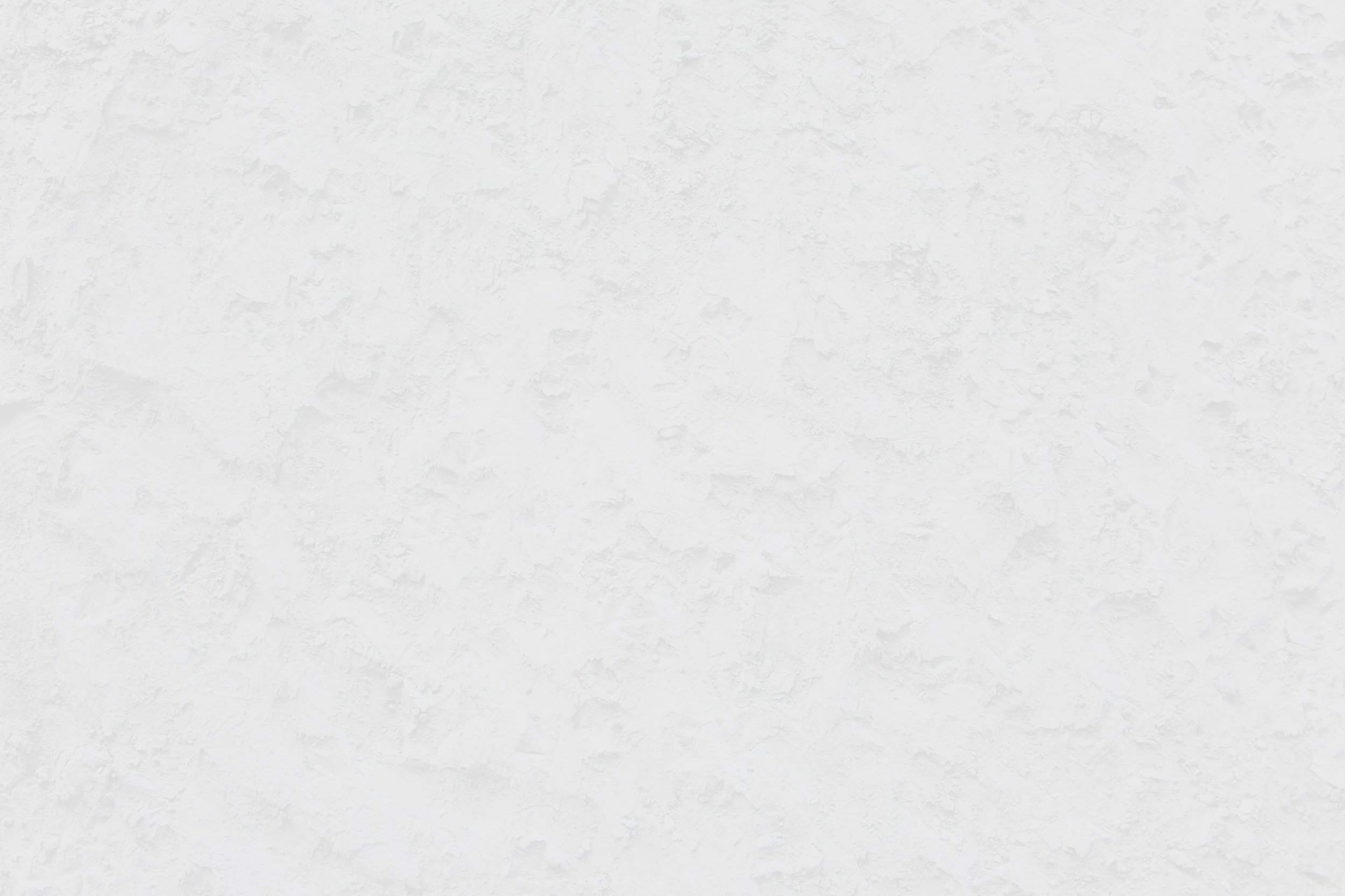
OSHA Tips to Protect Workers During the Holiday Season
Author, Jadyn Brandt, Client Communications Coordinator, Rancho Mesa Insurance Services, Inc.
As the holiday season approaches, many businesses will experience an increase in demand that can put an extra strain on a workplace and its employees. The surge in work often means more safety challenges for an employer. To deal with the additional strain, employers may be hiring new or seasonal employees, bringing in additional volunteers, and/or expanding their hours. Despite these changes, safety should still remain a top priority.
Author, Jadyn Brandt, Client Communications Coordinator, Rancho Mesa Insurance Services, Inc.
As the holiday season approaches, many businesses will experience an increase in demand that can put an extra strain on a workplace and its employees. The surge in work often means more safety challenges for an employer.
To deal with the additional strain, employers may be hiring new or seasonal employees, bringing in additional volunteers, and/or expanding their hours. Despite these changes, safety should still remain a top priority. Employers must work to train and prepare their employees and volunteers to recognize and prevent job hazards and enact safe work practices.
The Occupational Safety and Health Administration (OSHA) has shared a list of nine safety tips that employers should implement for the holiday season. Here’s what they recommend:
1. Train workers on safe practices in a language they speak and understand
It’s important that all workers are aware of necessary safety practices, rules and regulations. This can include basic safety policies or industry-specific safety trainings. Communicating these policies clearly and effectively is equally as important. Employers should regularly remind employees of safe practices in meetings and give trainings when needed.
2. Provide hands-on training for young and new workers on properly using equipment
New or seasonal workers should be given thorough explanations on all tasks they will perform. This is especially important if a worker will be operating equipment in a warehouse or will be sent out on deliveries. Encourage workers to look out for one another and assist newer hires if needed.
3. Delivery services and warehouse workers should wear bright, visible clothing
Longer hours could mean more workers will work late nights or early mornings. For some workers, that could mean part or all of their shifts are done in the dark. Be sure all workers are wearing the proper clothing and safety gear in order to be sure they are visible in all conditions.
4. Prevent injuries by properly stacking materials and making sure workers stand clear when doors are opened for unloading
Stocking inventory or loading and unloading delivery trucks can be dangerous if workers are unaware of proper lifting and handling techniques. Workers should be trained on these proper techniques before handling heavy items. Remind workers to stand clear of opening doors when unloading delivery trucks, to prevent any materials that may have shifted around in transit from falling on and injuring a person.
5. Create a detailed and flexible staffing plan to help reduce workplace stress
Accommodating everyone’s time-off requests during the holidays can be difficult. And workers may experience heightened stress due to the increased workloads and tight deadlines. Be mindful of each person’s wellbeing, and avoid overworking them during the holidays. Encourage taking regular breaks, and provide access to mental health resources. Keeping a detailed schedule will also help avoid any confusion on busy or unusual days.
6. When large crowds are expected, prepare an emergency plan
The holiday season means many businesses—especially in the retail or community services industry—may experience an increase in visitors. Whether you are a landscaper at a shopping mall or providing meals and health services to the community, larger crowds bring unique safety hazards, from crowd control to fire or medical emergencies. It is important to have a clear and well-communicated emergency plan in place to deal with these situations.
7. Make sure entrance and exit location signs are visible
Employers should ensure that all workers are familiar with emergency exits and evacuation routes. An evacuation plan should also account for disabled individuals, so that everyone can leave safely if necessary. Use clear signage to mark first aid stations, entrances, and exits. A communication system—like an intercom—should also be put in place to quickly convey information in place of emergency.
8. Encourage workers to report any safety and health concerns
Foster a workplace culture that is open to the reporting of any workplace accidents or health concerns. Create a clear and accessible reporting process, and be sure all workers are made aware of that process at the start of their employment. Make it clear to workers that they will not suffer retaliation if they do report an issue. If an issue is reported, act on it promptly and effectively. Staying aware of and prepared for any potential hazards or health problems can be a huge benefit to you and your team in the long run.
9. Remember: Seasonal workers have the same rights as full-time workers
During this time, many businesses may hire seasonal employees to meet increased demand. But it is important to remember that seasonal workers are entitled to the same rights and protections as permanent employees. Seasonal workers should not be excluded from safety trainings or benefits, and should be treated the same as full-time workers.
By following OSHA’s nine tips for holiday worker safety, businesses can help keep employees safe, healthy, and organized through the holiday season. Proper safety training, emergency preparedness and fostering a climate of safety can help keep a business running smoothly through the holidays. More safety resources and trainings can be found on Rancho Mesa’s SafetyOne™ Platform.
California Enacts Strict Updates to Lead Exposure Regulations
Author, Megan Lockhart, Client Communications Coordinator, Rancho Mesa Insurance Services, Inc.
Recently, the Cal/OSHA Standards board approved stricter standards for occupational lead exposure in both the construction industry and general industry.
Author, Megan Lockhart, Client Communications Coordinator, Rancho Mesa Insurance Services, Inc.
Recently, the Cal/OSHA Standards board approved stricter standards for occupational lead exposure in both the construction industry and general industry.
Effective January 1, 2025, the standards lowered the Permissible Exposure Limit (PEL) by 80% and the Action Limit (AL) by 93%, a vastly stringent policy compared to previous regulations.
The Permissible Exposure Limit is the legal limit that an employee can be exposed to a chemical substance or physical agent. The previous PEL for lead was 50 micrograms per cubic meter of air, and has now been reduced to 10 micrograms per cubic meter of air.
The Action Limit is the maximum value that can be reached before an action is needed to correct the issue. The previous lead level AL was 30 micrograms per cubic meter of air and is now only 2 micrograms per cubic meter of air.
With these limits reduced, employers must make changes in order to comply, such as updating their written program, conducting further exposure monitoring, and providing medical surveillance.
Employers must give workers exposure assessments to determine lead exposure in the blood. If employers do not perform these assessments, they are required to provide respiratory protection, protective work clothing and equipment, medical surveillance, training and posted warning signs.
If employee exposure reaches the new Action Limit, companies are required to implement a medical surveillance program. This includes medical examinations and procedures at no cost to the employees.
Employees who have been exposed to lead levels at or above the Action Level must be temporarily removed from work. These employees will have “medical removal protection benefits,” and will not lose earnings, seniority and other employment rights.
In addition to these requirements, exceeding Action Levels of exposure requires employers to provide employees respirators and protective work clothing and equipment, enact hygiene and housekeeping practices, offer lead exposure prevention training, and maintain monitoring and medical records of exposed employees for a minimum of 40 years.
To prepare for these new standards effective next year, clients should conduct new air monitoring tests and exposure assessments soon to ensure they are still compliant with the new exposure limits. If results exceed the new PEL and AL, they have until the end of the year to reduce exposure and remain in compliance.
For more information regarding these changes, clients can visit the Cal/OSHA website.
OSHA Form Submission Time: A Refresh
Author, Megan Lockhart, Client Communications Coordinator, Rancho Mesa Insurance Services, Inc.
It's that time of the year again, when employers review their work-related injuries and illnesses from the past year and fill out their OSHA 300A Form. Companies in designated industries must electronically submit the 300A Form to OSHA by March 2nd, 2024. As this deadline swiftly approaches, let’s review further details of these requirements.
Author, Megan Lockhart, Client Communications Coordinator, Rancho Mesa Insurance Services, Inc.
It's that time of the year again, when employers review their work-related injuries and illnesses from the past year and fill out their OSHA 300A Form. Companies in designated industries must electronically submit the 300A Form to OSHA by March 2nd, 2024. As this deadline swiftly approaches, let’s review further details of these requirements.
In addition to the 300A, companies with 100 or more employees in high-hazard industries must also submit information from their form 300-Log of Work-Related Injuries and Illnesses and Form 301-Injury and Illness Incident Report to OSHA annually.
Furthermore, the 300A Form must also be posted in the workplace, visible to employees, from February 1st to April 30th. The Form 300A does not include personal information such as employee names for confidentiality.
Rancho Mesa clients can utilize the RM365 HRAdvantage™ portal to track their incidents and generate their OSHA 300A Summary along with generate a .csv file that can be used to upload their incident information to OSHA’s Injury Tracking Application (ITA).
Employers can electronically submit their injury and illness information via OSHA’s ITA. OSHA changed their login format as of January 2023, so those who have not logged in last year will need to create a new Login.gov account, using their same email address, to access the application.
The forms 300A, 300-Log of Work-Related Injuries and Illnesses and 301-Injury and Illness Incident Report, as well as instructions on how to fill them out can be found in the OSHA Forms for Recording Work-Related Injuries and Illnesses document.
For additional information and detailed instructions on creating a new account, please visit OSHA’s Injury and Reporting webpage.
The Final Chapter: Addressing Training, Access and Recordkeeping in the IIPP
Author, Jack Marrs, Associate Account Executive, Rancho Mesa Insurance Services, Inc.
In this third installment of exploring an Injury and Illness Prevention Program (IIPP), we will be taking a closer look at: Providing employee training and instruction, procedures to allow employee access to the program, and recordkeeping and documentation.
Author, Jack Marrs, Associate Account Executive, Rancho Mesa Insurance Services, Inc.
In this third installment of exploring an Injury and Illness Prevention Program (IIPP), we will be taking a closer look at: Providing employee training and instruction, procedures to allow employee access to the program, and recordkeeping and documentation.
Providing Employee Training and Instruction
Providing clear and effective training for both employees and supervisors is essential for the success of an IIPP. All employees are required to be fully aware of the workplace hazards they may face. Comprehensive and well-conducted trainings can help reduce the likelihood of work-related injuries and illnesses. An article from The State Fund suggests “If you are unable to conduct your own required trainings, you should reach out to an outside consultant, Cal/OSHA consultation, vendors, your insurance carrier, and/or broker for assistance.” The more knowledgeable and prepared employees are, the safer the work environment becomes.
Take a look at the training resources that are available to your organization. Rancho Mesa clients can access the online safety training courses in the SafetyOne™ platform.
Procedures to Access the IIPP
All employees are required to have access to the written IIPP. This will ensure that all employees are fully aware of the safety protocols and hazard prevention strategies used to minimize workplace accidents and illnesses and thus, maintain a safe workplace.
According to Cal/OSHA, employers can meet this requirement by:
1. Unobstructed access through a company server or website, which allows employees to review, print, or email a copy of the IIPP
2. When requested, provide a printed copy of the IIPP (unless the employee agrees to receive an electronic copy)
The IIPP can be made accessible to users of the SafetyOne mobile app. It allows organizations to upload digital files into a file cabinet that is available only to their users. For employees who aren’t SafetyOne app users, they could scan a QR code or complete a webform to request the IIPP from their administrator. However your organization decides to distribute the IIPP, it should be easy for employees to access or request.
Recordkeeping and Documentation
Recordkeeping and proper documentation are crucial components of the IIPP. By maintaining accurate records, employers can learn from past incidents and identify injury and illness trends. This knowledge allows for necessary corrections and improvements in future operations, which will improve overall workplace safety. There are 5 steps required by the OSHA for a compliant recordkeeping system:
Each employer (unless exempt by size or industry) must record each fatality, injury, or illness that is work-related, is a new case, or meets one or more of the general recording criteria specified in Title 8, Section 14300.
Record each injury or illness on the Cal/OSHA Log of Occupational Work Related Injuries and Illnesses (Form 300) according to its instructions.
Prepare an Injury and Illness Incident Report (Form 301), or equivalent.
Annually review and certify the Cal/OSHA Form 300 and post the Summary of Work-Related Injuries and Illnesses (Form 300A) no later than February 1 and keep it posted where employees can see it until April 30.
Maintain the last five years of these records in your files.
A simple way to collect the incident information required for the OSHA logs (Form 300, 300A and 301) can be obtained by utilizing SafetyOne’s mobile forms. Either through the mobile app or via a QR Code or web link, employees can complete accident investigation forms and witness statements digitally. Then, the person responsible for documenting and maintaining the OSHA logs, can review the reports that came in through the mobile app and document the OSHA logs in the RM365 HRAdvantage Portal.
Rancho Mesa will host several webinars in the coming months to assist clients with understanding the best practices for completing their OSHA logs using SafetyOne™ and the RM365 HRAdvantage Portal.
Cal/OSHA has a Guide to Developing Your Workplace Injury and Illness Prevention Program that is helpful for organizations that need some assistance with getting started.
Rancho Mesa also has a 6-page Sample Injury and Illness Prevention Overview for California Employers available through our RM365 HRAdvantage Portal.
Following these steps is a proactive approach to building a safer working environment for all employees. The bottom line, it’s all about mitigating accidents before they happen and building a safe work environment.
Please contact me with any questions regarding the IIPP at (619)-486-6569 or via email at jmarrs@ranchomesa.com.
Safety Evolution: General Contractors Begin Requiring Safety Helmets Over Hard Hats
Author, Megan Lockhart, Client Communications Coordinator, Rancho Mesa Insurance Services, Inc.
The hard hat has long been a staple for construction-site safety. However, a new contender has entered the industry in 2023 as more and more general contractors are requiring safety helmets.
Author, Megan Lockhart, Client Communications Coordinator, Rancho Mesa Insurance Services, Inc.
The hard hat has long been a staple for construction-site safety. However, a new contender has entered the industry in 2023 as more and more general contractors are requiring safety helmets.
The safety helmet, while similar in form to the normal hard hat, includes added protection such as chin strap, face shield, and ear muffs. These new features allow for the helmet to sit more securely on the head while also protecting the ears from dangerously high noise levels and the eyes from possible debris.
“Since we made the switch to the new style hard hat, our employees don’t want to go back to the old-style hard hat,” Gilbane Building Company said. “This technology successfully removes the hazard of the hard hat falling off during a task, and wearing the face shield eliminates the possibility of forgetting to wear eye protection.”
While OSHA does not officially require the switch from hard hats to safety helmets, the topic was brought up at the Nation Association of Home Builders (NAHB) Spring Leadership Meeting in June 2023 in which director of OSHA’s Office of the Directorate of Construction, Scott Ketcham, granted insight on OSHA’s plans to improve jobsite safety with elevated standards for Personal Protective Equipment (PPE) in the near future.
“One initiative shared at the meeting is a pilot program for safety helmets meant to eventually replace hardhats as the preferred head protection in construction,” NAHB’s article about the meeting said. “Ketcham noted that 20% of head injuries in construction are the result of slips, trips, and falls and that hardhats do not protect against such injuries while helmets with chinstraps may stay on the head during a fall and offer protection.”
As PPE continues to evolve in the construction industry, it's important for subcontractors to be aware of what might be required of them on their job sites. Although no current laws require safety helmets over hard hats, Rancho Mesa will continue to offer updates as standards change.
SB 553: Governor Signs New Law for Workplace Violence Prevention Requirements
Author, Megan Lockhart, Client Communications Coordinator, Rancho Mesa Insurance Services, Inc.
On September 30, 2023 Governor Newsom signed into law new standards for California companies regarding workplace violence. Effective July 1, 2024, Senate Bill 553 (SB 553) will expand requirements for recordkeeping, injury and illness prevention programs, and employee training.
Author, Megan Lockhart, Client Communications Coordinator, Rancho Mesa Insurance Services, Inc.
On September 30, 2023 Governor Newsom signed into law new standards for California companies regarding workplace violence. Effective July 1, 2024, Senate Bill 553 (SB 553) will expand requirements for recordkeeping, injury and illness prevention programs, and employee training.
What do these new regulations define as “workplace violence?” Workplace violence is any act or threat of violence that occurs in a place of employment. The law applies to both verbal and written threats of violence and incidents involving use of a dangerous weapon regardless of whether an employee sustains an injury.
“The threat or use of physical force against an employee that results in, or has a high likelihood of resulting in, injury, psychological trauma, or stress, regardless of whether the employee sustains an injury,” Section (4).(a).(6).(B).(i) writes.
Recordkeeping
While companies are already required to report work-related injuries, now employers also must record every workplace violence incident in a violent incident log. The log includes information about each incident such as the date, time, and location, a detailed description, the people involved, the type of violence, and the consequences of the incident. The log must be retained for five years.
IIPP
Companies must include a written workplace violence prevention plan in addition to their Incident and Injury Prevention Program (IIPP).
The plan must include procedures for the following:
The employees responsible for creating and implementing the plan
The procedures the company will follow in the event of a violent incident, depending on its type
Enforcing procedure compliance for both employees and supervisors
Communicating to employees post-incident recordkeeping and investigation results
Identifying hazards and corrective procedures
Investigating and responding after the incident occurred
Annually evaluating the plans effectiveness and make necessary edits
Methods for implementing the training and procedures outlined in the plan
Training
SB 553 requires employers to provide workplace violence training to their employees. Training should inform employees of their company’s procedure for handling workplace violence and how they can access the written workplace violence prevention plan.
The training topics should also cover how to report workplace violence, how to respond and seek help in the event of an incident, strategies to avoid physical harm, implementing corrective measures, and information about accessing the violent incident log.
Workplace violence training is required for employees annually, and employers but retain training records for at least one year.
“Training records shall be created and maintained for a minimum of one year and include training dates, contents or a summary of the training sessions, names and qualifications of persons conducting the training, and names and job titles of all persons attending the training sessions,” Section 4.(f).(2) states.
Both the SafetyOne™ platform and the HR Portal offers a range of training related to SB 553’s required topics such as preventing workplace violence, security in the workplace, and workplace stress.
While the Cal/OSHA Standards Board is required to adopt the new standards no later than December 31, 2025, the law becomes enforceable on July 1, 2024. Exemptions to the new requirements are workplaces who are not open to the public and that have less than 10 employees working at one time as well as employees working from a remote location or in healthcare facilities.
SB 553 contains quite a lot of new requirements that might feel overwhelming for employers. Cal/OSHA is expected to release a model program for the standards including a workplace violence prevention plan in addition to the IIPP and training requirements.
Rancho Mesa will continue to keep clients informed as more resources are released. For any questions regarding this topic, contact your client technology coordinator.
OSHA Officially Rules for Expanded Recordkeeping Requirements for High-Hazard Industries
Author, Megan Lockhart, Client Communications Coordinator, Rancho Mesa Insurance Services, Inc.
Recently, the Occupational Safety and Health Administration (OSHA) made its final ruling to expand recordkeeping requirements for high-hazard industries, such as construction. The new requirements will take effect January 1, 2024 and will expand on what injury and illness information is needed to be electronically submitted to OSHA.
Author, Megan Lockhart, Client Communications Coordinator, Rancho Mesa Insurance Services, Inc.
Recently, the Occupational Safety and Health Administration (OSHA) made its final ruling to expand recordkeeping requirements for high-hazard industries, such as construction. The new requirements will take effect January 1, 2024 and will expand on what injury and illness information is needed to be electronically submitted to OSHA.
The requirements state that businesses with 100 or more employees in certain high-hazard industries must now electronically submit information from their Form 300-Log of Work-Related Injuries and Illnesses, as well as Form 301-Injury and Illness Incident Report to OSHA annually. This is in addition to Form 300A-Summary of Work-Related Injuries and Illnesses, which is already required.
Additionally, establishments are required to include their legal company name when making these submissions to OSHA from their injury and illness records.
Companies in high-hazard industries are already required to keep records of their work-related injuries and illnesses; however, this data is now to be submitted to OSHA, and the information gathered will be published on the OSHA website.
“OSHA will use these data to intervene through strategic outreach and enforcement to reduce worker injuries and illnesses in high-hazard industries,” Doug Parker, Assistant Secretary for Occupational Safety and Health, said in OSHA’s press release. “The safety and health community will benefit from the insights this information will provide at the industry level, while workers and employers will be able to make more informed decisions about their workplace's safety and health."
California businesses currently submit their recordkeeping information directly to Federal OSHA. Although the Cal/OSHA board has yet to release information regarding these new requirements, they must choose to uphold the standards set by Fed/OSHA or create stricter requirements. We will keep clients informed as further guidelines are announced.
Random Acts of Violence: Are They OSHA Recordable?
Author, Megan Lockhart, Client Communications Coordinator, Rancho Mesa Insurance Services, Inc.
Are random acts of violence OSHA recordable? This is a question many companies, particularly those that are required to report to OSHA annually, may ask. Whether the incident involves construction workers building in a high-crime area, or employees encountering hostile customers, determining if violent injuries are work-related is not always a black and white decision.
Author, Megan Lockhart, Client Communications Coordinator, Rancho Mesa Insurance Services, Inc.
Are random acts of violence OSHA recordable? This is a question many companies, particularly those that are required to report to OSHA annually, may ask. Whether the incident involves construction workers building in a high-crime area, or employees encountering hostile customers, determining if violent injuries are work-related is not always a black and white decision.
A letter submitted to OSHA this year requested interpretation for a scenario that fell into this recordkeeping gray-area. An employee was driving a company vehicle on a public road on his way to a client. When he approached an accident on the road, the individual who caused the accident shot the employee and stole the vehicle. OSHA determined that the employee’s injuries were work-related and was thus recordable because he was acting in the interest of the employer.
This scenario is pivotal to further defining a work-related incident. However, OSHA also acknowledged some cases that would be exceptions to these standards.
“Some cases involving violent acts might be included within one of the exceptions listed in section 1904.5(b)(2),” the OSHA board wrote. “For example, if an employee arrives at work early to use a company conference room for a civic club meeting and is injured by some violent act, the case would not be work-related…”
Incidents in workplaces such as construction sites that are among the public could also be OSHA recordable. In the past, clients have expressed concerns for the safety of their workers dealing with hostile individuals possibly entering the jobsite and putting their employees at risk.
It's best to assume a violent incident involving an employee is recordable, rather than omitting it from reporting and risk financial penalties.
Rancho Mesa offers several newly-added online training courses in the SafetyOne™ platform related to handling and preventing workplace violence. For any questions regarding accessing these trainings for your employees, contact your client technology coordinator.
OSHA Issues Heat Hazard Alert: Preparing for the Heat Wave
Author, Megan Lockhart, Media Communications and Client Services Coordinator, Rancho Mesa Insurance Services, Inc.
California can experience high heat in the late Summer and early Fall months, which increases the risk of heat illness for employees working outside.
Author, Megan Lockhart, Media Communications and Client Services Coordinator, Rancho Mesa Insurance Services, Inc.
California can experience high heat in the late Summer and early Fall months, which increases the risk of heat illness for employees working outside.
OSHA has issued a heat hazard alert, reminding companies of their responsibility to protect employees from heat illness this time of year. The U.S. Department of Labor also announced stricter enforcement for heat-related violations and increasing inspections in the construction and landscape industries.
To help employers prepare for this, we've added more dates to our Heat Illness Prevention webinar to help keep employees safe. Register for one of the webinars in the coming months to learn how to best protect employees and reduce the risk of claims.
Additionally, clients can view SafetyOne™’s Extreme Heat Checklist that covers best practices to follow before and during heat exposure, as well as protocol for heat illness incidents.
Identifying Proper Procedures for the Injury and Illness Prevention Program
Author, Jack Marrs, Associate Account Executive, Rancho Mesa Insurance Services, Inc.
In this second installment of exploring an Injury and Illness Prevention Program (IIPP) we will be taking a closer look at the procedures for identifying and evaluating workplace hazards, investigating occupational injury or illnesses, and correcting unsafe or unhealthy conditions, work practices and procedures.
Author, Jack Marrs, Associate Account Executive, Rancho Mesa Insurance Services, Inc.
In this second installment of exploring an Injury and Illness Prevention Program (IIPP) we will be taking a closer look at the procedures for identifying and evaluating workplace hazards, investigating occupational injury or illnesses, and correcting unsafe or unhealthy conditions, work practices and procedures.
Identifying and Evaluating Workplace Hazards
Employers need to have proper measures in place to identify potential health and safety risks like unsafe conditions and practices within the workplace. These measures involve conducting regular inspections to identify any areas of the workplace that may be hazardous. Also, conducting interviews with employees is a great way to identify any potential workplace hazards. During this process it is important to document any identified hazards and create a plan of action to fix them.
According to California’s State Fund “Inspections should be conducted by personnel who, through experience or training, are able to identify actual and potential hazards and understand safe work practices. They should be knowledgeable in the Cal/OSHA safety orders that apply to your workplace to better help you identify potential hazards.”
Investigating Occupational Injuries or Illnesses
Referring now to the investigation that should take place after an accident or near miss has occurred. The investigation should be done by a trained employee who is able to identify the cause of the accident and understands what solutions need to be put in place to prevent a similar incident from happening in the future. When doing an investigation, it is crucial to fill out an investigation report containing the details about what happened. This information is used to not only identify root causes but much of the data that is collected will need to be documented on the OSHA logs. CAL/OSHA lists five important steps for proper recordkeeping:
Each employer (unless exempt by size or industry) must record each fatality, injury, or illness that is work-related, is a new case, or meets one or more of the general recording criteria specified by OSHA.
Record each injury or illness on the OSHA Form 300, according to its instructions.
Prepare an Injury and Illness Incident Report known as Form 301, or its equivalent.
Annually review and certify the OSHA Form 300 and post the Summary of Work-Related Injuries and Illnesses known as the Form 300A no later than February 1 and keep it posted where employees can see it until April 30.
Maintain the last five years of these records in your files.
Lastly, building an inventory of investigation reports can lead to a stronger ability to identify developing trends and root causes that could lead to additional incidents, if not corrected.
Correcting Unsafe or Unhealthy Conditions, Work Practices and Procedures
Once your safety team becomes aware of a hazard, it is imperative to take immediate action. If the hazard is not easily fixable, employees should vacate the work area until a solution is implemented. Once the solution is in place, only trained staff members should enter the hazardous area to address the issue. This approach ensures effective hazard management while minimizing the risks associated with its correction.
By implementing an effective Injury and Illness Prevention Program, workplaces will begin to fulfill their regulatory obligation of maintaining a safe workplace, but also create a culture of safety and accountability.
Our next installment will cover the last 3 critical components of the IIPP: providing employee training and instruction, procedures to allow employee access to the program, and recordkeeping and documentation.
Please contact me with any questions about managing your risk at (619) 486-6569 or via email at jmarrs@ranchomesa.com.
Cal/OSHA to Enact ETS for Silica Exposure in Artificial Stone Industry
Author, Megan Lockhart, Media Communications and Client Services Coordinator, Rancho Mesa Insurance Services, Inc.
On July 20, 2023, the Cal/OSHA board approved a petition that requested an emergency temporary standard for respirable crystalline silica, a byproduct of manufacturing and cutting artificial stone material.
Author, Megan Lockhart, Media Communications and Client Services Coordinator, Rancho Mesa Insurance Services, Inc.
On July 20, 2023, the Cal/OSHA board approved a petition that requested an emergency temporary standard for respirable crystalline silica, a byproduct of manufacturing and cutting artificial stone material.
The petition was submitted to Cal/OSHA by the Western Occupational and Environmental Medical Association (WOEMA). It argued that the recent increase in advanced silicosis cases documented in California hospitals made heightened silica regulations necessary.
The permissible exposure limit (PEL) at which current silica safety requirements apply, is 50 micrograms per cubic meter of air over the course of an 8-hour shift. Employees whose interactions with respirable crystalline silica surpass this limit are required to implement control measures and wear personal professional equipment (PPE) in order to reduce exposure.
WOEMA advised that workplaces using engineered stone with a silica content greater than 50% should put in place the following ETS standards.
Regulated areas to limit employee access to spaces where artificial stone is fabricated.
Restrictions on fabrication without the use of water to suppress dust.
The use of airline respirators or power air-purifying respirators (PAPRs) for all work involving fabrication of artificial stone.
Annual reporting letters from employers to the Cal/OSHA Occupational Carcinogen Control Unit on the use of silica.
Strengthened penalty structure so that violations of the ETS result in citations classified as serious.
Updated information on CT exams and other diagnostic studies, prepared by Cal/OSHA.
Requirements that physicians or other licensed health care professionals report moderate to severe silicosis diagnosis to Cal/OSHA.
The Cal/OSHA staff’s evaluation concluded that most of the petition’s requested requirements were already part of the current standard for silica in construction environments. It therefore advised the board to deny adopting an ETS and instead, update the current permanent standards where needed.
However, in a contested decision, the board ultimately went against their staff’s recommendation, and approved the request to enact an ETS.
Cal/OSHA is expected to draw up the new emergency temporary standards within the next couple months. Silica exposure occurs in industries that manufacture stone countertops, brick, concrete blocks, or ceramic products. This motion may affect construction clients who frequently work with these materials.
Further information regarding the current safety regulations for respirable crystalline silica can be found in Cal/OSHA’s Code of Regulations.
Properly Utilizing Tailgate Meetings
Author, Casey Craig, Account Executive, Rancho Mesa Insurance Services, Inc.
For many foremen and superintendents, weekly tailgate meetings can feel like a task that just needs to be checked off the list. However, while the purpose of these meetings is critical for the health and well-being of fellow field employees, the time required and repetitive nature of them can create challenges. To maximize the benefits of these meetings, construction firms must be proactive and thoughtful as they develop an inventory of topics.
Author, Casey Craig, Account Executive, Rancho Mesa Insurance Services, Inc.
For many foremen and superintendents, weekly tailgate meetings can feel like a task that just needs to be checked off the list. However, while the purpose of these meetings is critical for the health and well-being of fellow field employees, the time required and repetitive nature of them can create challenges. To maximize the benefits of these meetings, construction firms must be proactive and thoughtful as they develop an inventory of topics.
Identifying Tailgate Meeting Topics
Take ample time with your sales team to understand the scope of your backlog to see where hazards may appear within these projects. Plan training topics with an eye on the weather, paying close attention to historically warm or cold months. Consider connecting with your insurance broker as well on recent injury trends that you can address with the crew.
This will be pertinent as your company approaches their renewal window with underwriters looking at claims history. They commonly ask, “what has the insured done to make sure these claims don’t happen again?” Learning from your past is key to being proactive. Knowing you will have certain exposures coming up and addressing those with preventative training topics begins to build a Best Practice Safety Program.
Accessing Content for Training
Locating “Toolbox” trainings can be time consuming and, in some cases, costly. And very often, the trainings may not be applicable to your operation and/or the trends you may need to focus on. With an eye to the future, Rancho Mesa has recently introduced a proprietary SafetyOne™ App. Safety managers will be able to document safety inspections from their mobile device and assign required fixes to employees, while also tracking when they have been completed. Meeting content can also be distributed to supervisors through their mobile device all with a focus of making safety meetings more efficient and effective. These same supervisors can now access a vast library that can be customized to their operation.
Reach out to me to learn more about the SafetyOne™ App and how Rancho Mesa can partner with you and your team moving forward. You can reach me at (619) 438-6900 or email me at ccraig@ranchomesa.com
Employers Prepare to Submit OSHA Form 300A
Author, Lauren Stumpf, Media Communications & Client Services Specialist, Rancho Mesa Insurance Services, Inc.
The time is here for you submit your company’s OSHA 300A Form. The OSHA 300A Form is a company’s summary of work-related injuries and illnesses within a given year. Employers must electronically submit their 2022 OSHA Form 300A data to Federal OSHA by March 2, 2023.
Author, Lauren Stumpf, Media Communications & Client Services Specialist, Rancho Mesa Insurance Services, Inc.
The time is here for you to submit your company’s OSHA 300A Form. The OSHA 300A Form is a company’s summary of work-related injuries and illnesses within a given year. Employers must electronically submit their 2022 OSHA Form 300A data to Federal OSHA by March 2, 2023.
Along with electronically submitting the data, the form must also be posted in the workplace, in a place visible to employees from February 1st to April 30th. To ensure employee confidentiality, the Form 300A does not include personal information such as employee names.
According to OSHA, establishments with 20 to 249 employees in designated industries are required to submit the 300A data. Establishments with 250 or more employees that are required to keep OSHA injury and illness records must also submit the data.
Companies under Federal OSHA jurisdiction can use the ITA Coverage Application to determine if they are required to electronically report their injury and illness information to OSHA. Establishments under State Plan jurisdiction should contact their State Plan.
There are three options for injury and illness data submissions. You can manually enter your data, upload a CSV file to add multiple establishments at the same time, or transmit data electronically via an API (application programming interface).
OSHA’s Injury Tracking Application (ITA) is using a new login format for submitting the Form 300A data. Those who have used the old login in previous years will need to make a new Login.gov account using their same email address in order to access the application for the 2023 collection of Calendar Year 2022 Form 300A data.
For additional information and detailed instructions on creating a new account, please visit OSHA’s Injury and Reporting webpage.
If Rancho Mesa clients have entered their 2022 incidents in the Risk Management Center, they will be able to generate their 300A Summary along with the .CSV file to upload to the Federal OSHA’s Injury Tracking Application website. Please refer to our video for instructions on how to do this.
Cal/OSHA Adopts New Non-Emergency COVID-19 Regulations
Author, Lauren Stumpf, Media Communications & Client Services Specialist, Rancho Mesa Insurance Services, Inc.
On Thursday, December 15, 2022 the California Occupational Safety & Health Standards Board (Cal/OSHA) voted on newly proposed COVID-19 regulations during a public forum meeting. With a 6 to 1 vote, the Non-Emergency COVID-19 Prevention Regulations were passed and adopted.
Author, Lauren Stumpf, Media Communications & Client Services Specialist, Rancho Mesa Insurance Services, Inc.
On Thursday, December 15, 2022 the California Occupational Safety & Health Standards Board (Cal/OSHA) voted on newly proposed COVID-19 regulations during a public forum meeting. With a 6 to 1 vote, the Non-Emergency COVID-19 Prevention Regulations were passed and adopted. The regulations will take effect once they are approved by the Office of Administrative Law in January 2023. They remain in effect for 2 years thereafter. However, the recordkeeping subsections will remain in effect for 3 years.
Previously, the proposed standards had the word “permanent” in the title despite it having the two and three year expiration dates. Cal/OSHA is now referring to the regulations as the “COVID-19 Prevention Non-Emergency Regulations.”
These new regulations include some of the same requirements found in the current COVID-19 Prevention Emergency Temporary Standards (ETS), but there are some new provisions.
First, let’s begin with pointing out some key requirements that are staying the same.
With the new regulations employers will still need to make COVID-19 testing available at no cost to the employee and during paid time to employees after a close contact.
Employers will still need to provide their employees with face coverings and respirators upon request.
Employers must still report information about employee deaths, serious injuries, and serious occupational illnesses to Cal/OSHA.
Some key difference between the current ETS and the new regulations include:
Employers are no longer required to maintain a standalone COVID-19 Prevention Plan, as long as COVID-19 requirements are addressed within a section of their Injury and Illness Prevention Program (IIPP).
Employers must now report major outbreaks to Cal/OSHA.
Exclusion pay for employees has been removed from the new regulations. This means employers will no longer be required to pay employees while they are excluded from work due to COVID-19. Instead the employer would only need to provide employees with information on the benefits they would be entitled to under state, federal, and local laws.
There are also some definition changes to what is considered “close contact” and “exposed group.” “Close contact” is now defined by looking at the size of the workplace in which the exposure took place. For indoor airspaces of 400,000 or fewer cubic feet, “close contact” is now defined as sharing the same indoor airspace with a COVID-19 case for a cumulative total of 15 minutes or more over a 24-hour period during the COVID-19 case’s infectious period. For indoor airspaces of greater than 400,000 cubic feet, “close contact” is defined as being within six feet of a COVID-19 case for a cumulative total of 15 minutes or more over a 24-hour period during the COVID-19 case’s infectious period. The term “exposed group” was clarified to include employer-provided transportation and employees residing within employer-provided housing that are covered by the COVID-19 Prevention standards.
Information provided by Cal/OSHA. For a full and detailed list of regulations please refer to Cal/OSHA’s Title 8 Proposed State Standard.
In order to be best prepared for these changes, it is recommended employers review the California Department of Public Health (CDHP) and Cal/OSHA guidance on requirements for things such as the use of face masks. Employers must also develop, implement, and maintain effective methods to prevent COVID-19 transmission by improving ventilation. It’s important to review CDPH and Cal/OSHA Interim Guidance for Ventilation, Filtration, and Air Quality in Indoor Environments.
Construction Death Rate Not Decreasing as Expected
Author, Casey Craig, Account Executive, Rancho Mesa Insurance Services, Inc.
With the heightened safety regulations and OSHA guidelines over the past decade, many would think we are working in a much safer environment with fewer fatalities. Despite the rising number of employees and using a standard based off deaths per 100,000 employees, the data is showing that the number of fatalities are the same as they were a decade ago.
Author, Casey Craig, Account Executive, Rancho Mesa Insurance Services, Inc.
With the heightened safety regulations and OSHA guidelines over the past decade, many would think we are working in a much safer environment with fewer fatalities. Despite the rising number of employees and using a standard based off deaths per 100,000 employees, the data is showing that the number of fatalities are the same as they were a decade ago.
With a much larger workforce, OSHA is severely understaffed compared to the previous decade. The agency does not have enough inspectors to visit nearly enough jobsites. They have been more reactive in the sense that they are imposing fines on companies after they have had losses. These fines represent a fraction of what it would take to motivate construction companies to revamp their respective safety programs. Employers have factored these fines into the cost of business to a certain extent.
OSHA is now contemplating whether it is worth doubling the jobsite inspections annually and/or increase fines drastically. There is no solid data to link an increase in jobsite inspections to fewer fatalities, so the logical answer would be heavier fines and a push for more negligent death claims to be criminally prosecuted.
Either of these options will lead to more oversite or more fines for the construction industry as a whole. One critical approach you can take is to prepare yourself as a business owner. Be proactive. Consider working with the consultation branch of OSHA to visit your operation and jobsites. This division within OSHA does not issue fines or violations. They do, however, offer recommendations and advice on how to make your operation safer. With the potential of OSHA’s fines increasing, it is time to make sure that your company is on the forefront of safety. A great first step is reaching out to your insurance broker to help you meet requirements and push you to exceed. With a potential recession looming, it is important to make sure you have insulated your company from risk, so you have the best chance at thriving.
If you have any urgent questions on this topic, you can reach me directly at (619) 438-6900 or email me at ccraig@ranchomesa.com.
Cal/OSHA Proposes Permanent COVID-19 Standards
Author, Lauren Stumpf, Media Communications & Client Services Specialist, Rancho Mesa Insurance Services, Inc.
With the COVID-19 Emergency Temporary Standards (ETS) scheduled to expire at the end of the year, Cal/OSHA has proposed new permanent standards.
Author, Lauren Stumpf, Media Communications & Client Services Specialist, Rancho Mesa Insurance Services, Inc.
With the COVID-19 Emergency Temporary Standards (ETS) scheduled to expire at the end of the year, Cal/OSHA has proposed new permanent standards.
The proposed permanent COVID-19 standards will be voted on during the December 15, 2022 Occupational Safety and Health Standards Board meeting. If passed, despite the word “permanent” being in the title, the standard will be in effect for the following two years. However, the record keeping requirements of the standard will apply for the following three years. So, with an effective date of January 1, 2023, the COVID-19 requirements can be expected to lift on January 1, 2025 and the recordkeeping requirements expected to lift on January 1, 2026.
Some proposed changes within the permanent COVID-19 standards include:
Employer Notice Requirements - The proposed permanent standards edits what information employers need to include in exposure notices to employees and the acceptable ways in which employers must distribute those notices.
Definition Changes - There are definition changes to what is considered a “close contact,” an “exposed group,” an “infectious period,” an “outbreak,” a “returned case,” and more.
Removal of the Exclusion Pay Policy - Under the current ETS, employers have to provide exclusion pay before requiring employees to exhaust other forms of potential paid leave. With the new proposed standards this is eliminated and employers would only need to provide their employees with information about local and federal COVID-19 benefits.
Reporting and Recordkeeping Requirements - Employers will no longer need to keep a record of close contacts and will no longer have to report information about workplace cases and outbreaks to their local health department. However, in a major outbreak setting, employers must report the outbreak to Cal/OSHA. That being said, employers still need to be aware of their local health department’s requirements.
For a detailed look at the proposed changes please refer to Cal/OSHA’s formal proposal document.
While there appears to be few differences between the current temporary standards and the new proposed permanent standards, it is recommended for businesses to locate and review their COVID-19 Prevention Program to ensure it can be readily updated. The new proposed permanent standards removes the requirement for employers to keep a separate COVID-19 Prevention Program, as long as their Injury and Illness Prevention Program (IIPP), includes COVID-19 policies. So even if you decide to only have an IIPP, it will still need to be updated with the latest COVID-19 procedures. Rancho Mesa has a COVID-19 Prevention Program template, that can be downloaded here.
Rancho Mesa will update its clients and readers with the status of the final rule once Cal/OSHA votes on December 15, 2022.
OSHA Proposes to Expand Electronic Form Submission Requirements
Author, Lauren Stumpf, Media Communications & Client Services Specialist, Rancho Mesa Insurance Services, Inc.
The Occupational Safety and Health Administration (OSHA) recently released a proposed rule that would increase electronic reporting requirements for businesses summiting OSHA logs.
Author, Lauren Stumpf, Media Communications & Client Services Specialist, Rancho Mesa Insurance Services, Inc.
The Occupational Safety and Health Administration (OSHA) recently released a proposed rule that would increase electronic reporting requirements for businesses summiting OSHA logs.
Currently, establishments with 250 or more employees, regardless of classification, and establishments with 20-249 employees, classified in certain high hazard industries, must electronically submit their Form 300A Summary to OSHA, annually.
The proposed rule changes would declare that only those in the classified high-hazard industries with 100 or more employees will be required to submit their Form 300A Summary electronically to OSHA. It would also require that Forms 300 and 301 be submitted electronically by these companies, when previously these two forms were to be kept confidential and only available to OSHA upon request.
Classified high hazard establishments with 20-99 employees would still only be required to submit the 300A Summary electronically to OSHA and would not need to electronically submit the 300 and 301 forms.
Under the proposed rule, OSHA would update the industries that are classified as high hazard and need to submit the data electronically.
OSHA has also proposed that company names be included on the electronic submissions. This, along with the injury and employee information that is included on the 300 and 301 forms, raises privacy concerns because this information would be available for public view via the Freedom of Information Act (FOIA).
The comment period for the public to voice their concerns ends on May 31, 2022. Information on how to submit comments on the proposed rule can be on the Federal Register.
Cal/OSHA Releases Final COVID-19 ETS
Author, Alyssa Burley, Media Communications and Client Services Manager, Rancho Mesa Insurance Services, Inc.
On Wednesday, April 6, 2022, Cal/OSHA released its third and final version of its COVID-19 Emergency Temporary Standard (ETS) that was approved by the Standards Board at its April 21, 2022 meeting. The revised standard is expected to remain in effect from May 6, 2022 through December 31, 2022.
Author, Alyssa Burley, Media Communications and Client Services Manager, Rancho Mesa Insurance Services, Inc.
On Wednesday, April 6, 2022, Cal/OSHA released its third and final version of its COVID-19 Emergency Temporary Standard (ETS) that was approved by the Standards Board at its April 21, 2022 meeting. The revised standard is expected to remain in effect from May 6, 2022 through December 31, 2022.
The third revision removes some language and requirements. Most notably:
Requirements of the ETS are the same for vaccinated and unvaccinated employees, and the definition for “fully vaccinated” has been removed.
California Department of Public Health's (CDPH) guidance governs exclusion and return-to-work criteria for those with a close contact, and when face coverings are required.
The “light test” for face coverings has been removed.
Self-administered and self-read testing is now acceptable to return to work when it includes independent verification like time-stamped photography.
A new definition for “returned case” has been added to identify those who have returned to work per the requirements in the ETS and did not develop COVID-19 symptoms.
Cleaning and disinfection procedures have been removed.
Requirements for physical distancing (except when there is a major outbreak) and barriers have been removed.
Cal/OSHA has revised several documents that may be helpful for employers:
What Employers and Workers Need to Know About COVID-19 Isolation and Quarantine
Revisions to the COVID-19 Prevention Emergency Temporary Standards
Rancho Mesa has revised its COVID-19 Prevention Program template based on the April 6, 2022 proposed revised ETS language. Download a copy of the template from within the Risk Management Center, or from the link below.
Preventing Stress Claims
Author, Jack Marrs, Associate Account Executive, Human Services Group, Rancho Mesa Insurance Services, Inc.
Specializing in non-profit insurance has opened my eyes to how difficult it is for some non-profit employees to deal with the stress related to their jobs. It’s the nature of the work. Helping people through difficult situations can be rewarding for an employee, but it can also be emotionally draining when they become invested in their clients to the point where it can lead to burnout.
Author, Jack Marrs, Associate Account Executive, Human Services Group, Rancho Mesa Insurance Services, Inc.
Specializing in non-profit insurance has opened my eyes to how difficult it is for some non-profit employees to deal with the stress related to their jobs. It’s the nature of the work. Helping people through difficult situations can be rewarding for an employee, but it can also be emotionally draining when they become invested in their clients to the point where it can lead to burnout.
Employees can suffer from emotional and mental illness as a result of their working environments, which can lead them to file workers’ compensation claims. Depending on the nature of the non-profit’s mission, employees may witness a variety of disturbing realities that the general public isn’t used to experiencing.
Since psychiatric injuries are based on an employees' personal experience, it’s much more difficult for physicians to verify these types of claims. Plus, these conditions can also develop from multiple stressors in an employee’s professional and personal life like when they are dealing with a death, going through a divorce, or filing for bankruptcy. So, it’s hard to determine what percentage of the claim is work-related and what percentage is caused by outside factors.
Workplace stress can trigger mental and physical illnesses and injuries, so identifying and correcting stressful situations early, can prevent costly health care costs and workers’ compensation claims.
Managers should periodically check in with their employees to see how they are doing with regards to their workload, relationships with clients, co-workers and vendors, etc., but also their personal lives. If there is an issue in the workplace, it can be addressed quickly before it causes extreme stress to the employee. If something is happening at home, it could be affecting their productivity and performance on the job. And, the employer may be able to refer their employee to resources to assist them as they deal with whatever stressors are in their personal lives. This also helps to establish if the stress felt by the employee is work-related or personal.
Employers can reduce workplace stress by ensuring effective communication from supervisors to employees. Whether the communication is about job duties and expectations, career growth within the organization, or a traumatic event and relevant resources to help employees cope, being transparent with employees can relieve some stress caused by not knowing what’s to come.
Stress claims take a tremendous toll on both employees working for non-profits and the organizations themselves. Rancho Mesa provides an extensive library of training offered through our Risk Management Center and the RM365 HRAdvantage™ Portal. These trainings can be easily accessed and allow for our non-profit clients to be proactive in mitigating the severe impact of stress claims.
Contact me at jmarrs@ranchomesa.com or (619) 486-6569 to learn more about these options.
Understanding the DART and TCIR Calculations
Author, Lauren Stumpf, Media Communications and Client Services Specialist, Rancho Mesa Insurance Services, Inc.
When a project owner asks you to provide the company’s DART or TCIR rate, it may seem a little overwhelming at first. But, the two numbers are really a score that can be used to compare contractors’ safety history. These numbers can be important during the bidding process when comparing multiple bids and could be a determining factor for who is awarded the contract.
Author, Lauren Stumpf, Media Communications and Client Services Specialist, Rancho Mesa Insurance Services, Inc.
When a project owner asks you to provide the company’s DART or TCIR rate, it may seem a little overwhelming at first. But, the two numbers are really a score that can be used to compare contractors’ safety history. These numbers can be important during the bidding process when comparing multiple bids and could be a determining factor for who is awarded the contract.
DART stands for days away, restricted, or transferred. A DART rate is used to track any OSHA recordable workplace injury or illness that result in days away from work, restricted duty, or transfer of duties.
On the other hand, the TCIR is the total case incident rate (also known as the Total Recordable Incident Rate or sometimes referred to as the OSHA Incident Rate). It measures a company's past safety performance based on their incident rate. A TCIR is found by looking at the number of work-related injuries per 100 full-time workers during a one-year period.
The TCIR will likely be higher than the DART because it includes all incidents, not just the ones that results in lost time.
Project owners are increasingly requesting these numbers along with the project bid. Not only do they want to see how much it’s going to cost them to build the project, but they want to know how safe their contractor is on the jobsite. These numbers show that.
OSHA also uses these calculations to monitor high-risk industries.
Rancho Mesa’s Risk Management Center features a tool that helps contractors generate their DARTs and TCIRs. Contractors can use the Incident Track application to enter and track an incident’s details. Once that incident has been saved, the system will allow them to generate OSHA logs based on that data and generate the DART and TCIR.
“It’s an easy-to-use tool that ensures the numbers are accurate and available whenever they’re needed,” said Alyssa Burley, Media Communications and Client Services Manager with Rancho Mesa Insurance Services, Inc.
To learn more about the Risk Management Center’s capabilities, sign up for an upcoming webinar at www.ranchomesa.com/workshops-and-webinars.