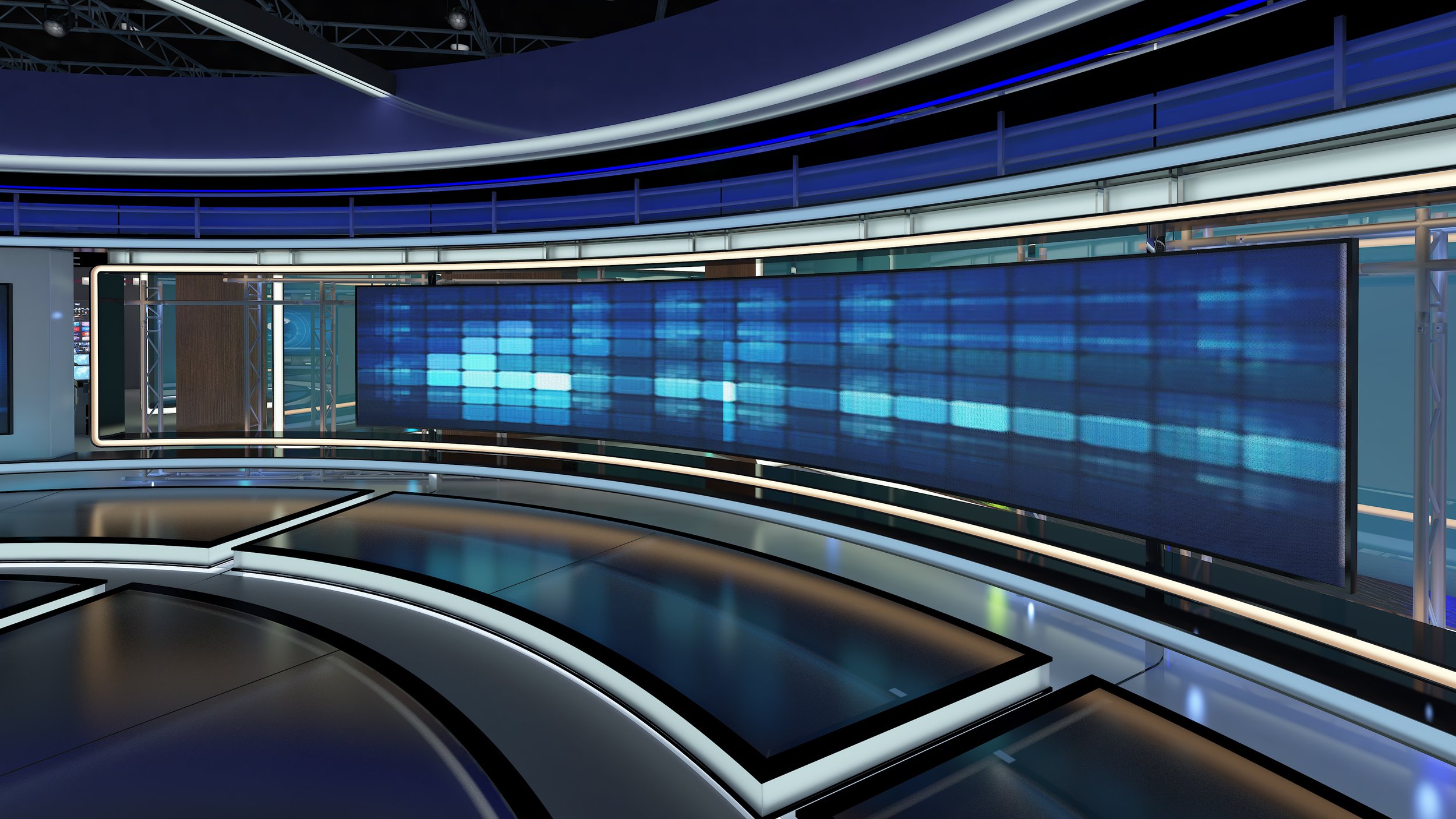
Industry News
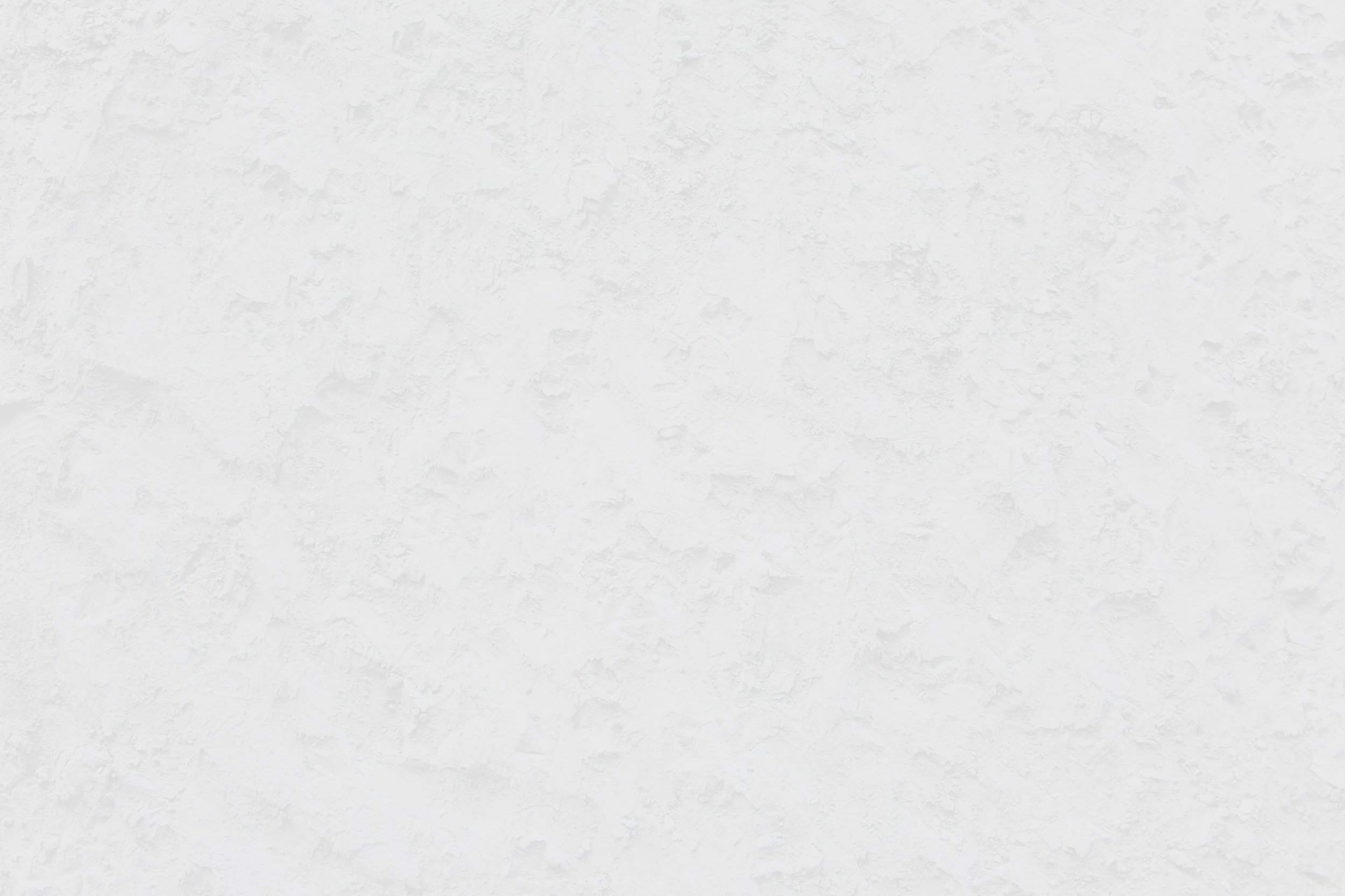
California’s Indoor Heat Illness Prevention Standard Approved: What You Need to Know
Author, Megan Lockhart, Client Communications Coordinator, Rancho Mesa Insurance Services, Inc.
Recently, the Cal/OSHA Standards Board approved new requirements for California businesses, heat illness prevention for indoor work spaces. The new Section 3396 addition to the California Labor Code will go into effect as early as August 1, 2024.
Author, Megan Lockhart, Client Communications Coordinator, Rancho Mesa Insurance Services, Inc.
Recently, the Cal/OSHA Standards Board approved new requirements for California businesses, heat illness prevention for indoor work spaces. The new Section 3396 addition to the California Labor Code will go into effect as early as August 1, 2024.
The law states that requirements apply to “all indoor work areas where the temperature equals or exceeds 82 degrees Fahrenheit when employees are present.”
For work environments such as warehouses, restaurants, and manufacturing plants, temperatures can rise dangerously high, putting employees at risk for heat illness. Let’s take a look into the new requirements for employers.
Provide access to cool-down areas, and encourage employees to take cool-down rests.
Provide access to potable water that is fresh, suitably cool, free of charge, and located as close as possible to indoor cool-down area.
Monitor employee symptoms and provide appropriate first aid and emergency response if they exhibit or report signs of heat illness.
Closely observe new employees for the first 14 days of employment as they acclimatize.
Provide employees and supervisors with training on topics such as heat risk factors, symptoms of heat illness, water consumption, and emergency procedures.
Establish, implement and maintain a written Heat Illness Prevention plan for the work environment.
Some additional requirements also apply when the temperature or heat index reaches or exceeds 87 degrees while employers are present, or the temperature reaches or exceeds 82 degrees and employees wear clothing that restricts heat removal or they work in a high radiant heat area.
In these cases, employers need to maintain records of their indoor temperature or heat index. They also must initiate engineering, administrative, and personal control measures to reduce the indoor working environment and maintain it below 87 degrees.
As temperatures continue to soar in many parts of California, employers with employees working indoors in high heat conditions should evaluate their current heat policies to ensure they comply with these impending labor law changes.
For further information about indoor heat illness prevention compliance, clients should refer to the Cal/OSHA website, which offers resources employers can utilize, including a Sample Written Heat Illness Prevention Plan for Indoor and Outdoor Places of Employment (Model Program).
Resources and Tools for Completing Your Workplace Violence Prevention Plan
Author, Megan Lockhart, Client Communications Coordinator, Rancho Mesa Insurance Services, Inc.
As July 1st quickly approaches, California businesses are working hard to prepare their Workplace Violence Prevention plans before the deadline. In our aim to serve the needs of our clients, Rancho Mesa has outlined resources we offer to supplement your specific company’s training and plan.
Author, Megan Lockhart, Client Communications Coordinator, Rancho Mesa Insurance Services, Inc.
As July 1st quickly approaches, California businesses are working hard to prepare their Workplace Violence Prevention plans before the deadline. In our aim to serve the needs of our clients, Rancho Mesa has outlined resources we offer to supplement your specific company’s training and plan.
The SafetyOne™ platform and the RM365 HRAdvantage™ portal has the online training topics and recordkeeping tools available for workplace violence prevention.
HR Portal Course
Preventing Workplace Violence Training for Employees
SafetyOne Courses
Active Shooter: Surviving an Attack
Workplace Security
Workplace Violence
Workplace Violence in Construction Environments
Workplace Violence in Food Processing and Handling Environments
Workplace Violence in Healthcare Facilities
Workplace Violence in Office Environments
Clients can utilize SafetyOne’s incident report forms or create their own custom forms to collect workplace violence incident data on the job. The information collected in these forms are stored in the SafetyOne administrator website. Forms such as Accident Investigation, Incident Investigation, Incident Witness Statement, and Witness Statement can support clients’ Workplace Violence Prevention plan.
Online training can be used as a tool towards creating a complete Workplace Violence Prevention Plan. However, employers must also train their employees on the specific hazards of their company’s location, and address these in their written Workplace Violence Prevention Plan.
For questions regarding accessing Rancho Mesa resources, clients can contact their client technology coordinator.
Four Weeks of Safety: Important Resources for National Safety Month
Author, Megan Lockhart, Client Communications Coordinator, Rancho Mesa Insurance Services, Inc.
As we hit the halfway mark on the 2024 year, we’ve explored plenty of important topics related to health and safety each month. The month of June is National Safety Month by the National Safety Council (NSC), in partnership with the Center for Disease Control and Prevention (CDC).
Author, Megan Lockhart, Client Communications Coordinator, Rancho Mesa Insurance Services, Inc.
As we hit the halfway mark on the 2024 year, we’ve explored plenty of important topics related to health and safety each month. The month of June is National Safety Month by the National Safety Council (NSC), in partnership with the Center for Disease Control and Prevention (CDC).
This month brings attention to safety issues as a whole and highlights important topics each week. So whether our clients are construction leaders or human services professionals, June is an opportunity to evaluate the safety practices of yourself and your workers.
Week 1: Safety Engagement
One of the foundational aspects of cultivating a safe workplace is through intentional participation in safety practices.
“Both employers and employees must be engaged in safety. Working together, employers and employees can develop policies and procedures to identify, monitor, mitigate, and eliminate work-related hazards,” NSC states.
One way Rancho Mesa encourages clients to engage in safety is by offering tools to help best equip them for the task. The SafetyOne™ platform offers weekly toolbox talks that employers can administer to workers on the job. SafetyOne also offers a library of online training courses to encourage safety engagement. The videos and quizzes are taken individually via a web browser.
The more relevant the employer’s lessons are to the current safety hazards and job tasks, the more valuable the training will be to employees.
Week 2: Roadway Safety
The Bureau of Labor Statistics states that the leading cause of work-related deaths in the nation are motor vehicle crashes and either the first or second leading cause of death in each major industry. That’s why the NSC has dedicated this week to driving safety.
Rancho Mesa offers a library of driver trainings, both in the form of toolbox talks and online trainings:
Toolbox Talks
Defensive Driving
Driving in Wet Conditions
Like Oil and Water, Drinking And Driving Do Not Mix
Do Cellular Phones Cause More Vehicle Accidents?
Motor Vehicles – A Form of Locking Out
Motor Vehicles – Seat Belts
No Vehicle Accidents on This Site
Safety While Refueling Vehicles and Equipment
Vehicle and Equipment Parking Safety for Landscape Contractors
Online Training
Driver Safety: The Basics
Driving Safety
Driving Defensively
Distracted Driving
Commercial Drivers License (CDL) Defensive Driver Training
Rancho Mesa also recently hosted its Fleet Safety Workshop, presented by Travelers Insurance. The recording is now available.
Week 3: Risk Reduction
The best ways to keep employees safe and prevent workplace incidents is by identifying the environmental hazards and addressing them immediately.
According to NSC’s Injury Facts, there were a total of 4,695 preventable workplace deaths and 4.53 million medically consulted injuries in 2022.
Foreseeing potential injuries before they happen mitigates risk. A pivotal part of this process for companies is through observing their work environment. The SafetyOne app offers the Observation tool clients can use to perform safety observations or inspections via a phone or tablet. An issue identified in an observation can be assigned to other employees or emailed to third parties. Once completed, they are automatically documented in the platform.
Additionally, employers create and maintain a written Injury and Illness Prevention Program (IIPP) and a copy must be made available in the workplace. This week is a good opportunity to revisit your company’s IIPP and make sure it is up to date and covers all job hazards. The Cal/OSHA website offers a model IIPP for both high hazard and non-high hazard industries.
Week 4: Slips, Trips and Falls
As the final topic of the month, slips, trips, and falls are a prevalent hazard across most industries. Whether missing a step down a slippery ladder, losing balance on an aerial lift, or slipping on wet flooring, falls can happen anywhere in the workplace. The best way to prevent these common incidents is to eliminate the hazard initially and make sure employees are trained in the correct safety procedures.
Rancho Mesa offers toolbox talks and online training that covers slip, trip, and fall prevention:
Toolbox Talks
Slips, Trips and Falls
Fall Prevention and Guardrails
Slip and Fall Prevention for Landscape Contractors
Watch Your Step! Don't Slip & Fall
Fall Protection
Avoiding Falls
Let's Prevent Slips, Trips and Falls
Online Training
Slips, Trips, and Falls
Slips, Trips and Falls in Construction Environments
Slips, Trips, and Falls in Food Processing and Food Handling Environments
Slips, Trips, and Falls in Healthcare Environments
Slips, Trips, and Falls in Office Environments
Fall Protection in Industrial and Construction Environments
As we continue to make our way through National Safety Month, it's a good idea for clients to evaluate any holes in their safety practices. The opportunities employers take to keep workers trained will impact their hazard prevention, and ultimately their incident rate, the rest of the year.
Rancho Mesa is committed to offering the necessary tools to help.
For questions about accessing resources in SafetyOne, clients can reach out to their client technology coordinator.
National Electrical Safety Month: Preventing Hazards in the Construction Industry
Author, Megan Lockhart, Client Communications Coordinator, Rancho Mesa Insurance Services, Inc.
We’ve just started the month of May, National Electrical Safety month. The Electrical Safety Foundation International (ESFI) dedicates this month annually to help reduce electrical-related fatalities, injuries, and property loss.
Author, Megan Lockhart, Client Communications Coordinator, Rancho Mesa Insurance Services, Inc.
We’ve just started the month of May, National Electrical Safety month. The Electrical Safety Foundation International (ESFI) dedicates this month annually to help reduce electrical-related fatalities, injuries, and property loss.
Many Rancho Mesa construction clients not only work with electricity, but specialize in some form of it. So, it's a great opportunity to reevaluate workplace safety and ensure any hazards to shock or fire are addressed.
One of ESFI’s missions is to spread awareness to specific industries that work with and around electricity. Accidents involving electricity can lead to electrocution and flash fire, and the construction industry stands the most risk. The Center for Construction Research and Training found that construction workers account for almost half of all workplace electrocution deaths in the nation.
As we continue through the month of May, it's a good idea to make sure your workers are handling electrical tools and hazards safely. Rancho Mesa offers training resources in the SafetyOne™ app with several online courses relating to electrical safety as well as various toolbox talks.
For more information about the resources Rancho Mesa offers, clients can reach out to their Client Technology Coordinator.
Distracted Driving Awareness Month: Prevent Fleet Accidents Through Training
Author, Megan Lockhart, Client Communications Coordinator, Rancho Mesa Insurance Services, Inc.
April is Distracted Driving Awareness Month across the nation. The month is dedicated to preventing distractions while driving as well as spreading awareness of these dangers on the road.
Author, Megan Lockhart, Client Communications Coordinator, Rancho Mesa Insurance Services, Inc.
April is Distracted Driving Awareness Month across the nation. The month is dedicated to preventing distractions while driving as well as spreading awareness of these dangers on the road.
The National Highway Traffic Safety Administration reports more than 3,500 people in the United States were killed due to distracted driving in 2021. The most common forms of distraction are phone use such as texting, scrolling apps, or phone calls. When it comes to fleet and construction vehicles, it's important to make sure your employees are driving safely.
One vital way to prevent accidents on the road is through driver training. The SafetyOne™ platform offers a library of online driver training topics to ensure your drivers are safe on the road.
Driver Safety: The Basics
Driving Safety
Driving Defensively
Distracted Driving
Commercial Driver’s License (CDL) Defensive Driver Training
Additionally, clients can register for Rancho Mesa’s in-person Fleet Safety workshop on Friday, May 17, 2024 at the Mission Valley Library.
To learn more about the training offered in SafetyOne, contact your client technology coordinator.
Safety Evolution: General Contractors Begin Requiring Safety Helmets Over Hard Hats
Author, Megan Lockhart, Client Communications Coordinator, Rancho Mesa Insurance Services, Inc.
The hard hat has long been a staple for construction-site safety. However, a new contender has entered the industry in 2023 as more and more general contractors are requiring safety helmets.
Author, Megan Lockhart, Client Communications Coordinator, Rancho Mesa Insurance Services, Inc.
The hard hat has long been a staple for construction-site safety. However, a new contender has entered the industry in 2023 as more and more general contractors are requiring safety helmets.
The safety helmet, while similar in form to the normal hard hat, includes added protection such as chin strap, face shield, and ear muffs. These new features allow for the helmet to sit more securely on the head while also protecting the ears from dangerously high noise levels and the eyes from possible debris.
“Since we made the switch to the new style hard hat, our employees don’t want to go back to the old-style hard hat,” Gilbane Building Company said. “This technology successfully removes the hazard of the hard hat falling off during a task, and wearing the face shield eliminates the possibility of forgetting to wear eye protection.”
While OSHA does not officially require the switch from hard hats to safety helmets, the topic was brought up at the Nation Association of Home Builders (NAHB) Spring Leadership Meeting in June 2023 in which director of OSHA’s Office of the Directorate of Construction, Scott Ketcham, granted insight on OSHA’s plans to improve jobsite safety with elevated standards for Personal Protective Equipment (PPE) in the near future.
“One initiative shared at the meeting is a pilot program for safety helmets meant to eventually replace hardhats as the preferred head protection in construction,” NAHB’s article about the meeting said. “Ketcham noted that 20% of head injuries in construction are the result of slips, trips, and falls and that hardhats do not protect against such injuries while helmets with chinstraps may stay on the head during a fall and offer protection.”
As PPE continues to evolve in the construction industry, it's important for subcontractors to be aware of what might be required of them on their job sites. Although no current laws require safety helmets over hard hats, Rancho Mesa will continue to offer updates as standards change.
SB 553: Governor Signs New Law for Workplace Violence Prevention Requirements
Author, Megan Lockhart, Client Communications Coordinator, Rancho Mesa Insurance Services, Inc.
On September 30, 2023 Governor Newsom signed into law new standards for California companies regarding workplace violence. Effective July 1, 2024, Senate Bill 553 (SB 553) will expand requirements for recordkeeping, injury and illness prevention programs, and employee training.
Author, Megan Lockhart, Client Communications Coordinator, Rancho Mesa Insurance Services, Inc.
On September 30, 2023 Governor Newsom signed into law new standards for California companies regarding workplace violence. Effective July 1, 2024, Senate Bill 553 (SB 553) will expand requirements for recordkeeping, injury and illness prevention programs, and employee training.
What do these new regulations define as “workplace violence?” Workplace violence is any act or threat of violence that occurs in a place of employment. The law applies to both verbal and written threats of violence and incidents involving use of a dangerous weapon regardless of whether an employee sustains an injury.
“The threat or use of physical force against an employee that results in, or has a high likelihood of resulting in, injury, psychological trauma, or stress, regardless of whether the employee sustains an injury,” Section (4).(a).(6).(B).(i) writes.
Recordkeeping
While companies are already required to report work-related injuries, now employers also must record every workplace violence incident in a violent incident log. The log includes information about each incident such as the date, time, and location, a detailed description, the people involved, the type of violence, and the consequences of the incident. The log must be retained for five years.
IIPP
Companies must include a written workplace violence prevention plan in addition to their Incident and Injury Prevention Program (IIPP).
The plan must include procedures for the following:
The employees responsible for creating and implementing the plan
The procedures the company will follow in the event of a violent incident, depending on its type
Enforcing procedure compliance for both employees and supervisors
Communicating to employees post-incident recordkeeping and investigation results
Identifying hazards and corrective procedures
Investigating and responding after the incident occurred
Annually evaluating the plans effectiveness and make necessary edits
Methods for implementing the training and procedures outlined in the plan
Training
SB 553 requires employers to provide workplace violence training to their employees. Training should inform employees of their company’s procedure for handling workplace violence and how they can access the written workplace violence prevention plan.
The training topics should also cover how to report workplace violence, how to respond and seek help in the event of an incident, strategies to avoid physical harm, implementing corrective measures, and information about accessing the violent incident log.
Workplace violence training is required for employees annually, and employers but retain training records for at least one year.
“Training records shall be created and maintained for a minimum of one year and include training dates, contents or a summary of the training sessions, names and qualifications of persons conducting the training, and names and job titles of all persons attending the training sessions,” Section 4.(f).(2) states.
Both the SafetyOne™ platform and the HR Portal offers a range of training related to SB 553’s required topics such as preventing workplace violence, security in the workplace, and workplace stress.
While the Cal/OSHA Standards Board is required to adopt the new standards no later than December 31, 2025, the law becomes enforceable on July 1, 2024. Exemptions to the new requirements are workplaces who are not open to the public and that have less than 10 employees working at one time as well as employees working from a remote location or in healthcare facilities.
SB 553 contains quite a lot of new requirements that might feel overwhelming for employers. Cal/OSHA is expected to release a model program for the standards including a workplace violence prevention plan in addition to the IIPP and training requirements.
Rancho Mesa will continue to keep clients informed as more resources are released. For any questions regarding this topic, contact your client technology coordinator.
Heat Illness Awareness Vital for California's Construction Companies
Author, Kevin Howard, Account Executive, Rancho Mesa Insurance Services, Inc.
California faces a critical need to prioritize heat illness awareness among its workforce. The combination of Southern California's recent above average rainfall and the anticipated heatwave resulting from El Niño has created the possibility of an extremely warm summer. Construction companies must remain vigilant and adaptable, implementing appropriate measures to address these changing weather dynamics and ensuring the safety of their workers. By staying informed about weather forecasts and implementing flexible work schedules and site preparations, companies can effectively navigate these challenging conditions and prioritize the well-being of their employees. By understanding the significance of heat illness awareness, companies can ensure the safety and well-being of their workers while fostering productivity, minimizing downtime, and improving overall project efficiency.
Author, Kevin Howard, Account Executive, Rancho Mesa Insurance Services, Inc.
California faces a critical need to prioritize heat illness awareness among its workforce. The combination of Southern California's recent above-average rainfall and the anticipated heatwave resulting from El Niño has created the possibility of an extremely warm summer. Construction companies must remain vigilant and adaptable, implementing appropriate measures to address these changing weather dynamics and ensuring the safety of their workers. By staying informed about weather forecasts and implementing flexible work schedules and site preparations, companies can effectively navigate these challenging conditions and prioritize the well-being of their employees. By understanding the significance of heat illness awareness, companies can ensure the safety and well-being of their workers while fostering productivity, minimizing downtime, and improving overall project efficiency.
Recognizing the Risks
The construction industry in California is particularly vulnerable to heat-related illnesses and fatalities due to the physically demanding nature of the work and prolonged exposure to high temperatures. Heat stress, heat exhaustion, and heat stroke are severe conditions that can result in significant health complications. By acknowledging the risks associated with working in high temperatures, construction companies can proactively take measures to mitigate potential hazards.
Cultivating a Culture of Safety
Establishing a culture of safety is crucial for construction companies in California to create an environment where employee well-being is the top priority. Employers should develop comprehensive programs focused on preventing heat-related illnesses. These initiatives should include employee training, hazard assessments, access to shade and water, acclimatization procedures, and adjusted work schedules. Regular safety meetings and open lines of communication should be encouraged to address concerns, share information, and ensure that everyone is aware of the potential risks associated with working in high heat.
Implementing Worksite Modifications
Modifying the worksite environment can reduce the impact of heat-related illnesses. Construction companies should establish shaded rest areas where workers can take breaks, cool down, and hydrate. Access to potable water should be readily available to prevent dehydration, and regular hydration breaks should be scheduled throughout the day. Additionally, adjusting work schedules to avoid the hottest periods, utilizing cooling fans or misting systems, and implementing rotational job assignments can help reduce heat stress and improve worker safety.
Monitoring and Supervision
Supervisors and management play an important role in ensuring heat illness awareness on construction sites. Regular monitoring of weather conditions and temperature provides valuable information for determining appropriate work practices and scheduling. Close supervision enables the early detection of signs of heat-related illness and allows for immediate intervention. Encouraging workers to prioritize their own well-being and empowering them to report any symptoms promptly is equally important.
Heat illness awareness is vital for construction companies operating in California. By prioritizing worker safety and implementing comprehensive programs to prevent heat-related illnesses, employers can safeguard their employees from the risks associated with high temperatures. Moreover, such initiatives enhance productivity, avoid worker’s compensation claims, reduce downtime due to illness or injuries, and improve overall project efficiency. By cultivating a safety culture, providing necessary PPE, implementing worksite modifications, and maintaining close supervision, construction companies can establish a healthy and safe working environment that ensures the well-being of their workers.
Rancho Mesa’s Upcoming Heat Illness Prevention Workshop
Lastly, Rancho Mesa Insurance is hosting our annual Heat Illness Prevention workshop on June 2nd at the Mission Valley library from 10:00 AM to 11:30 AM. This workshop will provide valuable insights, best practices, and resources to help construction companies and their employees effectively address and prevent heat-related illnesses. Be sure to join this workshop to stay informed and proactive in ensuring the health and safety of your workforce.
Implementing Best Practices when Hiring in the Construction Industry
Author, Casey Craig, Account Executive, Rancho Mesa Insurance Services, Inc.
With unemployment rates settling near 4 percent, it is becoming increasingly difficult to find the right employees to help grow your construction company. With most able-bodied workers having secure employment, this leads to having either apprentice-type employees that come with unique challenges or pulling from an aging workforce that can bring cumulative injuries and risks. Navigating these issues can be complex and there is not a perfect solution, but employer’s hiring practices need to change in order to keep up with the current state of the industry.
Author, Casey Craig, Account Executive, Rancho Mesa Insurance Services, Inc.
With unemployment rates settling near 4%, it is becoming increasingly difficult to find the right employees to help grow your construction company. With most able-bodied workers having secure employment, this leads to having either apprentice-type employees that come with unique challenges or pulling from an aging workforce that can bring cumulative injuries and risks. Navigating these issues can be complex and there is not a perfect solution, but employer’s hiring practices need to change in order to keep up with the current state of the industry.
When hiring new employees, consider:
Pre-hire drug testing
Pre-hire physicals
Targeted job postings with accurate description of daily work
Multiple levels of interviews
Simulating work at your office that potential new hires would be performing in the field
The US saw a unique shift in the workplace as a result of COVID-19 where employees felt their value skyrocket as fewer people were willing to work in-person. Employers were forced to increase wages to get bodies on jobsites. In prior years, it may have been enough to just rely on word of mouth and referrals to get new hires. Too often now, we are seeing new hires suffer “ghost injuries” that are quickly followed with letters of representation. These and similar types of cumulative trauma claims can have long term impacts on your experience rating (EMR). While these situations are difficult to prevent, using best practices and conducting thorough interviews with your prospective employees will allow you to make educated decisions which typically lead to better hires.
Taking advantage of the best practices listed above can help insulate your company from poor hiring decisions. Obviously, we would love for new hires to turn into long term employees, as onboarding and proper training can be a costly expense in both other employee’s time and payroll. In a recent survey conducted by Traveler’s Insurance, it was shown that 34% of workplace injuries occurred during the worker’s first year on the job. This can be from a combination of inexperience, overexertion, and/or lack of safety knowledge.
Consider these hiring and onboarding processes to assist in mitigating the glaring number of claims that are emanating from newer employees or employees that have limited experience on jobsites. The financial impact they can have on your company will impact your balance sheet for years and can be potentially avoided with implementing some of our recommended techniques
To learn more about improving your hiring practices or how Rancho Mesa can help to improve your process, reach out at (619) 438-6900 or ccraig@ranchomesa.com.
Guidance for Developing an Effective Injury and Illness Prevention Program
Author, Sam Brown, Account Executive, Rancho Mesa Insurance Services, Inc.
As some company leaders may recall, since 1991, all California employers are required to maintain a written Injury and Illness Prevention Program (IIPP). An IIPP is an understandable and accessible safety program tailored to a business’ operations. An effective IIPP will help an employer establish and maintain a safe workplace while setting expectations and protocols for all employees.
Author, Sam Brown, Account Executive, Rancho Mesa Insurance Services, Inc.
As some company leaders may recall, since 1991, all California employers are required to maintain a written Injury and Illness Prevention Program (IIPP). An IIPP is an understandable and accessible safety program tailored to a business’ operations. An effective IIPP will help an employer establish and maintain a safe workplace while setting expectations and protocols for all employees.
The information below outlines the necessary elements of a written and effective IIPP, while recommending a resource to use when creating or updating the plan.
Cal/OSHA requires all Injury and Illness Prevention Programs to contain nine critical components:
A person (or persons) with authority and responsibility for implementing the program is identified.
A system for ensuring employees comply with safe and health work practices.
A system for communicating with employees in a form readily understandable by all affected.
Procedures for identifying and evaluating work place hazards.
Procedures to investigate occupational injury or illness.
Procedures for correcting unsafe or unhealthy conditions, work practices and procedures.
Provide employee training and instruction.
Procedures to allow employee access to the Program.
Recordkeeping and documentation.
California employers looking for guidance on the Cal/OSHA required Injury & Illness Prevention Program can often feel overwhelmed when addressing all required elements, while also abiding by the best practices of updating the plan, annually. Fortunately, California’s State Compensation Insurance Fund offers a free IIPP builder to all employers.
The State Fund’s IIPP Builder will help an employer create an IIPP from scratch, but can also help improve an existing program to make it more effective and compliant. An employer is first asked to answer a series of questions about safety practices. The answers will help build a safety program and tailor it to the business. The IIPP builder will also guide an employer through the required elements of the written IIPP.
Once finished, an employer can save the IIPP to their computer and upload it into their SafetyOne™ mobile app. They can also print and keep a hard copy at all locations. Lastly, to make it a truly effective program, the employers should share details of the IIPP with their employees.
Rancho Mesa wants clients to feel comfortable and confident when creating, updating, and sharing details of their Injury and Illness Prevention Program. To learn more about an effective IIPP and the State Fund’s IIPP BuilderSM, please contact me at sbrown@ranchomesa.com or (619) 937-0175.
Insurance Benefits of GPS Systems in Commercial Vehicles
Author, Kevin Howard, Account Executive, Rancho Mesa Insurance Services, Inc.
For businesses that rely on a fleet of commercial vehicles, insurance costs can be a significant expense. Insurance carriers calculate premiums based on a variety of factors, including the age and condition of the vehicles, driver experience and record, and the frequency and distance of trips. One factor that can positively impact insurance costs is the use of global positioning systems (GPS) in commercial vehicles. Below, we will explore some of the insurance benefits of installing GPS systems in commercial vehicles.
Author, Kevin Howard, Account Executive, Rancho Mesa Insurance Services, Inc.
For businesses that rely on a fleet of commercial vehicles, insurance costs can be a significant expense. Insurance carriers calculate premiums based on a variety of factors, including the age and condition of the vehicles, driver experience and record, and the frequency and distance of trips. One factor that can positively impact insurance costs is the use of global positioning systems (GPS) in commercial vehicles. Below, we will explore some of the insurance benefits of installing GPS systems in commercial vehicles.
Improved Safety
GPS systems in commercial vehicles can help improve safety by providing real-time tracking of vehicles and drivers. This can help businesses identify and address unsafe driving behaviors such as speeding, sudden braking, and hard cornering. By addressing these behaviors, businesses can reduce the risk of accidents and insurance claims which can result in lower insurance premiums.
Reduced Theft Risk
GPS systems can also help reduce the risk of vehicle theft. If a commercial vehicle is stolen, GPS tracking can help businesses locate the vehicle quickly and notify law enforcement. This can help reduce the risk of property loss and insurance claims related to vehicle theft.
Faster Claims Processing
In the event of an accident or other incidents involving a commercial vehicle, GPS systems can provide valuable data to insurance carriers. This can include information on the location, speed, and direction of travel of the vehicle at the time of the incident. This data can help insurance carriers process claims more quickly and accurately, which can help reduce costs and improve the overall claims experience for businesses.
Lower Insurance Premiums
GPS in vehicles can lower the loss ratio which is a key factor that underwriters use. Furthermore, the disclosure to insurance underwriters that GPS is installed and properly utilized could help insurance brokers negotiate lower premiums based on this added safety feature.
Improved Business Operations
In addition to insurance benefits, GPS systems can also help businesses improve their operations. Real-time tracking and reporting can help businesses optimize their routes, reduce fuel costs, and improve overall efficiency. By improving operations, businesses can reduce costs and improve profitability, which can have a positive impact on insurance costs and premiums.
GPS Systems have a multitude of benefits. These systems can save lives because drivers pay more attention to detail when GPS is on the vehicle. They can lower insurance premiums which can improve the return on investment. Lastly, the ability to track a stolen vehicle is a control that creates major benefits knowing that the cost of vehicles and the time needed to locate a replacement is at an all-time high.
To learn more about how GPS on your commercial vehicles can be implemented as part of your risk management plan, contact me at (619)438-6874 or khoward@ranchomesa.com.
Properly Utilizing Tailgate Meetings
Author, Casey Craig, Account Executive, Rancho Mesa Insurance Services, Inc.
For many foremen and superintendents, weekly tailgate meetings can feel like a task that just needs to be checked off the list. However, while the purpose of these meetings is critical for the health and well-being of fellow field employees, the time required and repetitive nature of them can create challenges. To maximize the benefits of these meetings, construction firms must be proactive and thoughtful as they develop an inventory of topics.
Author, Casey Craig, Account Executive, Rancho Mesa Insurance Services, Inc.
For many foremen and superintendents, weekly tailgate meetings can feel like a task that just needs to be checked off the list. However, while the purpose of these meetings is critical for the health and well-being of fellow field employees, the time required and repetitive nature of them can create challenges. To maximize the benefits of these meetings, construction firms must be proactive and thoughtful as they develop an inventory of topics.
Identifying Tailgate Meeting Topics
Take ample time with your sales team to understand the scope of your backlog to see where hazards may appear within these projects. Plan training topics with an eye on the weather, paying close attention to historically warm or cold months. Consider connecting with your insurance broker as well on recent injury trends that you can address with the crew.
This will be pertinent as your company approaches their renewal window with underwriters looking at claims history. They commonly ask, “what has the insured done to make sure these claims don’t happen again?” Learning from your past is key to being proactive. Knowing you will have certain exposures coming up and addressing those with preventative training topics begins to build a Best Practice Safety Program.
Accessing Content for Training
Locating “Toolbox” trainings can be time consuming and, in some cases, costly. And very often, the trainings may not be applicable to your operation and/or the trends you may need to focus on. With an eye to the future, Rancho Mesa has recently introduced a proprietary SafetyOne™ App. Safety managers will be able to document safety inspections from their mobile device and assign required fixes to employees, while also tracking when they have been completed. Meeting content can also be distributed to supervisors through their mobile device all with a focus of making safety meetings more efficient and effective. These same supervisors can now access a vast library that can be customized to their operation.
Reach out to me to learn more about the SafetyOne™ App and how Rancho Mesa can partner with you and your team moving forward. You can reach me at (619) 438-6900 or email me at ccraig@ranchomesa.com
Inflation Increases Cost of Workers’ Compensation Claims
Author, Sam Brown, Account Executive, Rancho Mesa Insurance Services, Inc.
As non-profits and leaders of human service organizations navigate important business decisions in the face of inflation, it’s important to consider measures that can reduce inflation’s impact to an organization’s operating budget. Today, we look at inflation’s effect on workers’ compensation insurance and strategies to reduce future costs.
Author, Sam Brown, Account Executive, Rancho Mesa Insurance Services, Inc.
As non-profits and leaders of human service organizations navigate important business decisions in the face of inflation, it’s important to consider measures that can reduce inflation’s impact to an organization’s operating budget. Today, we look at inflation’s effect on workers’ compensation insurance and strategies to reduce future costs.
In August 2022, the U.S. Bureau of Labor Statistics published data reflecting an 8.3% increase to the Consumer Price Index for All Urban Consumers over the previous 12 months. If medical costs are the largest expenditure in workers’ compensation claims, how is the recent inflationary trends affecting worker’s compensation medical and claim costs?
Medical costs per workers’ compensation claim increased almost 18% between 2012 and 2021 according to a study by the National Council on Compensation Insurance (NCCI). Moving forward, the Office of the Actuary at the Centers for Medicare and Medicaid Services projects an index closely related to medical costs in worker’s compensation will increase 2.5% to 3% beyond 2022. Inflation has impacted many segments of the economy, including workers’ compensation insurance.
Strategies to reduce inflation’s impact to workers’ compensation insurance premiums, include:
Offer modified duty to all injured workers.
Offering modified duty to employees with work restrictions is widely known to reduce the likelihood of workers’ compensation litigation and reduces the overall cost and duration of the claim. In addition, if an injured employee rejects the offer, then the individual can no longer receive temporary disability benefits. These positive outcomes may help explain why at least one insurance company offers a 10% rate discount to employers that offer modified duty to all injured workers.
Consider on-call medical technician and telephonic nurse triage services.
Rancho Mesa has published articles about the benefits of on-site medical evaluations and nurse-triage services, but they deserve a fresh look. Both services can advise the injured workers on proper self-care, thereby providing the employee with helpful treatment options while avoiding a costly workers’ compensation claim. The employer will also avoid paying the injured worker’s wages while they travel to and wait inside a medical provider’s office.
The nurse-triage service will continue to manage the injury and help the employee determine if further medical care is necessary. Of course, employers should always report the incident to the workers’ compensation carrier.
Consider an alternative workers’ compensation plan to gain more control over claim and insurance premiums.
It’s true that self-insured worker’s compensation plans are typically reserved for very large organizations, but options exist that replicate some of the most beneficial features. The available options depend on the size of the employer.
Small to medium sized employers can explore self-insured groups (SIG) to potentially split payroll between class codes and receive dividends. SIGs are very motivated to help members avoid workers’ compensation claims, but also closely manage open claims. A member vote is typically required after a review of an applicant’s safety plan, safety record, and operations.
Medium to large organizations may consider loss-sensitive plans. The policy will typically offer reduced annual premium if the employer can control claim frequency and claim costs. There may also be an opportunity to share in the underwriting profit following a plan year. Of course, the insured may also need to share in the claim costs in a poor performing year.
Another alternative, workers’ compensation deductible plans, can also offer a premium savings if the employer is willing to pay a deductible on each claim. Deductibles can range from $10,000 to $100,000 or more, depending on the employer’s risk tolerance.
Looking at alternative workers’ compensation strategies and plans can help employers navigate the current pattern of inflation. The information above can reduce claim frequency, claim cost, and also inform nonprofit and human service leaders about potential insurance premium savings available.
To discuss your organization’s options, contact me at (619) 937-0175 or sbrown@ranchomesa.com.
Construction Death Rate Not Decreasing as Expected
Author, Casey Craig, Account Executive, Rancho Mesa Insurance Services, Inc.
With the heightened safety regulations and OSHA guidelines over the past decade, many would think we are working in a much safer environment with fewer fatalities. Despite the rising number of employees and using a standard based off deaths per 100,000 employees, the data is showing that the number of fatalities are the same as they were a decade ago.
Author, Casey Craig, Account Executive, Rancho Mesa Insurance Services, Inc.
With the heightened safety regulations and OSHA guidelines over the past decade, many would think we are working in a much safer environment with fewer fatalities. Despite the rising number of employees and using a standard based off deaths per 100,000 employees, the data is showing that the number of fatalities are the same as they were a decade ago.
With a much larger workforce, OSHA is severely understaffed compared to the previous decade. The agency does not have enough inspectors to visit nearly enough jobsites. They have been more reactive in the sense that they are imposing fines on companies after they have had losses. These fines represent a fraction of what it would take to motivate construction companies to revamp their respective safety programs. Employers have factored these fines into the cost of business to a certain extent.
OSHA is now contemplating whether it is worth doubling the jobsite inspections annually and/or increase fines drastically. There is no solid data to link an increase in jobsite inspections to fewer fatalities, so the logical answer would be heavier fines and a push for more negligent death claims to be criminally prosecuted.
Either of these options will lead to more oversite or more fines for the construction industry as a whole. One critical approach you can take is to prepare yourself as a business owner. Be proactive. Consider working with the consultation branch of OSHA to visit your operation and jobsites. This division within OSHA does not issue fines or violations. They do, however, offer recommendations and advice on how to make your operation safer. With the potential of OSHA’s fines increasing, it is time to make sure that your company is on the forefront of safety. A great first step is reaching out to your insurance broker to help you meet requirements and push you to exceed. With a potential recession looming, it is important to make sure you have insulated your company from risk, so you have the best chance at thriving.
If you have any urgent questions on this topic, you can reach me directly at (619) 438-6900 or email me at ccraig@ranchomesa.com.
Training Supervisors on Workplace Injury Protocol Can Improve Claim Outcomes
Author, Sam Brown, Account Executive, Rancho Mesa Insurance Services, Inc.
California employers work hard to maintain a safe workplace, but accidents and injuries can occur. While human resources professionals typically have an excellent understanding of the workers’ compensation claim process, proper supervisor training can improve workers’ compensation outcomes for employers and their injured workers.
Author, Sam Brown, Account Executive, Rancho Mesa Insurance Services, Inc.
California employers work hard to maintain a safe workplace, but accidents and injuries can occur. While human resources professionals typically have an excellent understanding of the workers’ compensation claim process, proper supervisor training can improve workers’ compensation outcomes for employers and their injured workers.
Supervisors are often the first to become aware of a workplace injury. Without proper training a supervisor may have the best of intentions, but can create problems by not following company protocols. Sound supervisor training may include:
How to Get the Injured Worker Medical Attention
Supervisors should know the designated medical provider or understand how and when to direct an employee to use telephonic nurse triage services. The supervisor should know what information the provider will need and, if necessary, how the injured worker should be transported to the medical provider’s physical location.
Internal Communication
Supervisors must know how to initiate documenting a workplace injury and how to notify the proper parties of the incident. What incident report should be used? Are witness statements important? Who needs to know of the incident as soon as possible? Whose responsibility is it to report the claim to the insurance company?
Effective Communication
A supervisor setting a tone of empathy immediately following a workplace injury can lead to positive outcomes and reduce the likelihood of litigation. Effective communication can even reduce claim frequency. A study by Shaw, et al., shows how four hours of supervisor training on communication skills and accommodation for workers reporting health concerns produced “a 47% reduction in new claims and an 18% reduction in active lost-time claims.”
Well-designed training can greatly improve workers’ compensation claim outcomes when supervisors follow company protocols, get injured workers medical care, and practice effective communication in the workplace.
Rancho Mesa has developed downloadable forms for the Supervisor’s Report of Employee Accident or Near Miss, and Witness’ Statement to help collect important information about an accident.
For more information on effective workers’ compensation programs, please contact me at sbrown@ranchomesa.com or (619) 937-0175.
Staying Safe While the Weather Heats Up
Author, Greg Garcia, Account Executive, Rancho Mesa Insurance Services, Inc.
As temperatures continue to rise across the country, it is important for landscape companies to take proper precautions while working in the heat of summer. Heat-related illnesses are very much preventable, if the proper safety steps are in place.
Author, Greg Garcia, Account Executive, Rancho Mesa Insurance Services, Inc.
As temperatures continue to rise across the country, it is important for landscape companies to take proper precautions while working in the heat of summer. Heat-related illnesses are very much preventable if the proper safety steps are in place.
First, companies must implement a heat illness prevention plan and comply with local, state and federal regulations to ensure employees remain safe while working in heat.
One of the most common symptoms of heat illness is dehydration. When employees are out working in hot conditions, it is imperative the crew leader or supervisor makes the crew take regular breaks to get properly hydrated. Even if employees say they are not thirsty, a supervisor needs to insist they have some water. By the time a person feels thirsty, they’re already dehydrated. Remembering to schedule breaks throughout the work day can have a positive impact on controlling heat-related illnesses.
Another way landscape companies are staying safe as the weather heats up is to make sure they are acclimatizing their employees. This is especially important for all new hires. The best way to acclimatize these employees is to gradually increase the amount of work they are doing over a 14-day period when temperatures start to heat up. By doing this, you are allowing employees’ bodies to get used to working in such hot conditions, and thus, lowering the chances of having any heat-related illnesses.
To beat the heat, landscape companies can implement alternative schedules that allow employees to start their work day earlier. If a crew normally gets out to a job site at 8 a.m., the alternative schedule would send the crew out an hour earlier, during the hot months. This allows more work to be done earlier in the morning when temperatures have not reached the daily high. This also allows crews to get done with work an hour earlier, thus getting employees off job sites when temperatures are at their highest.
These are just some examples of how landscape companies are doing their best to prevent heat-related illnesses.
Heat illness prevention is just one of the topics available in Rancho Mesa’s RM365 Advantage Safety Star™ Program . Clients are encouraged to complete the course and implement a Heat Illness Prevention Plan that complies with OSHA standards.
Automobile Rental Reimbursement for Tree Care Companies
Author, Rory Anderson, Account Executive, Rancho Mesa Insurance Services, Inc.
A tree care company’s auto fleet includes specialty vehicles like bucket and box trucks. These vehicles are important assets for the company and critical for completing jobs. Getting into an auto accident is already stressful, but what can add more grief is if the vehicle that gets damaged is vital for your business. In this case, you will be looking to rent a replacement vehicle during the repair window so that your business can maintain productivity and profitability. With this in mind, rental reimbursement coverage helps cover the rental cost incurred while your vehicle is repaired after a covered loss.
Author, Rory Anderson, Account Executive, Rancho Mesa Insurance Services, Inc.
A tree care company’s auto fleet includes specialty vehicles like bucket and box trucks. These vehicles are important assets for the company and critical for completing jobs. Getting into an auto accident is already stressful, but what can add more grief is if the vehicle that gets damaged is vital for your business. In this case, you will be looking to rent a replacement vehicle during the repair window so that your business can maintain productivity and profitability. With this in mind, rental reimbursement coverage helps cover the rental cost incurred while your vehicle is repaired after a covered loss.
In the tree care business, renting a specialty truck is no easy task. Rental bucket and box trucks are expensive and limited. Renting these specialty trucks can cost up to $600 per day. In addition to the cost, the COVID-19 pandemic continues to cause problems with the supply chain of products, including auto parts. So, not only is it expensive to rent these specialty trucks, but it is also taking longer than normal to get vehicles repaired.
The standard rental reimbursement coverage will offer between $50 and $100 per day for 30 days. With how costly the tree care specialty trucks are and with the amount of time it is taking to repair these trucks, you can see how you might find yourself in a sticky situation if one of these key trucks goes down. However, certain insurance carriers will offer to increase the per day amount as well as extend the period of rental reimbursement coverage, if needed.
Partnering with an insurance professional who specializes in the tree care industry is important to make sure that your bucket and box trucks have the correct rental reimbursement coverage in the case of an auto accident.
To discuss this potential gap within your current insurance program or any other commercial insurance for your tree care business, contact me at (619) 486-6437 or randerson@ranchomesa.com.
Three Changes to Your Routine That Increases Safety
Author, Greg Garcia, Account Executive, Landscape Group, Rancho Mesa Insurance Services, Inc.
Every landscape company wants to be safe. So, I want to discuss three ways to improve safety in your workplace starting today: routine equipment maintenance, personal protective equipment (PPE) checks, and finally, assessing job site hazards.
Author, Greg Garcia, Account Executive, Landscape Group, Rancho Mesa Insurance Services, Inc.
Every landscape company wants to be safe. So, I want to discuss three ways to improve safety in your workplace, starting today.
1) Routine Equipment Maintenance
Routine maintenance and cleaning of equipment is essential for any landscape company wanting to make sure all of their equipment is running properly and is ready for a day’s work. From a safety standpoint, we see the biggest risk comes from those companies who use sprayers to fertilize lawns and plants for their clients. By not cleaning the sprayers out daily, landscape companies are putting their employees at risk of being exposed to pesticides and herbicides, which can be detrimental to the employee’s heath. Therefore, routinely checking and cleaning pieces of equipment can not only improve your productivity and profitability by making sure equipment is ready for work, but can also lead to a much safer working environment for your employees.
2) personal protective equipment (PPE) checks
Personal protective equipment is one of the most important things landscape employees can use to protect themselves while they work. Whether it be thorny bushes to cut back, the use of loud chainsaws or mowers, or just the effects of being out in the sun, it is important to assess the job site hazards and make proper PPE choices. A few examples that landscape companies are doing to help their employees fight the effects of being exposed to the sun are: wearing long sleeve shirts, wearing sun hats that provide shade to the face and neck, and wearing proper sunglasses to help with the heavy glare. Always keeping up to date and staying informed on proper PPE will ensure that your landscape company is doing all they can to stay safe.
3) assessing job site hazards
Finally, addressing job site hazards is vital for companies in the landscape industry. The safety manager, supervisor or foreman need to get out to job sites and really see what hazards are out there. For example, look to see if there are any poisonous plants at the jobsite and/or any pieces of debris or puddles in the walk ways that could create a trip and fall hazard. All of these exposures need to be noted to ensure everyone is aware of potential risks. Every jobsite is different, so it is crucial that your team remain proactive and really hone in on the potential risks at each particular jobsite.
If equipment checks, PPE checks, and job site checks are not currently in your landscape company’s safety routine, I would strongly suggest starting that routine, today.
Subscribe to our weekly landscape-specific safety emails to ensure you are getting relevant training materials every week.
If you have questions about how to mitigate your company’s risk, reach out to Greg Garcia at (619) 438-6905 or ggarcia@ranchomesa.com.
Cal/OSHA Releases Final COVID-19 ETS
Author, Alyssa Burley, Media Communications and Client Services Manager, Rancho Mesa Insurance Services, Inc.
On Wednesday, April 6, 2022, Cal/OSHA released its third and final version of its COVID-19 Emergency Temporary Standard (ETS) that was approved by the Standards Board at its April 21, 2022 meeting. The revised standard is expected to remain in effect from May 6, 2022 through December 31, 2022.
Author, Alyssa Burley, Media Communications and Client Services Manager, Rancho Mesa Insurance Services, Inc.
On Wednesday, April 6, 2022, Cal/OSHA released its third and final version of its COVID-19 Emergency Temporary Standard (ETS) that was approved by the Standards Board at its April 21, 2022 meeting. The revised standard is expected to remain in effect from May 6, 2022 through December 31, 2022.
The third revision removes some language and requirements. Most notably:
Requirements of the ETS are the same for vaccinated and unvaccinated employees, and the definition for “fully vaccinated” has been removed.
California Department of Public Health's (CDPH) guidance governs exclusion and return-to-work criteria for those with a close contact, and when face coverings are required.
The “light test” for face coverings has been removed.
Self-administered and self-read testing is now acceptable to return to work when it includes independent verification like time-stamped photography.
A new definition for “returned case” has been added to identify those who have returned to work per the requirements in the ETS and did not develop COVID-19 symptoms.
Cleaning and disinfection procedures have been removed.
Requirements for physical distancing (except when there is a major outbreak) and barriers have been removed.
Cal/OSHA has revised several documents that may be helpful for employers:
What Employers and Workers Need to Know About COVID-19 Isolation and Quarantine
Revisions to the COVID-19 Prevention Emergency Temporary Standards
Rancho Mesa has revised its COVID-19 Prevention Program template based on the April 6, 2022 proposed revised ETS language. Download a copy of the template from within the Risk Management Center, or from the link below.
Wearable Technology Is the Future of Jobsite Safety
Author, Sam Clayton, Vice President, Construction Group, Rancho Mesa Insurance Services, Inc.
The future is here and construction companies are starting to adopt wearable technology for their workers to reduce and prevent injuries from occurring on their jobsites. Wearable technology can be defined as any device that construction workers wear on his/her body. Since the construction industry accounts for nearly half of all fatal work injuries, this new type of personal protective equipment (PPE) is going to look radically different in the years ahead and should reduce both fatal and non-fatal injuries on jobsites worldwide. Below is an overview of five technologies in use today or soon to be in use in the near future.
Author, Sam Clayton, Vice President, Construction Group, Rancho Mesa Insurance Services, Inc.
The future is here and construction companies are starting to adopt wearable technology for their workers to reduce and prevent injuries from occurring on their jobsites. Wearable technology can be defined as any device that construction workers wear on his/her body. Since the construction industry accounts for nearly half of all fatal work injuries, this new type of personal protective equipment (PPE) is going to look radically different in the years ahead and should reduce both fatal and non-fatal injuries on jobsites worldwide. Below is an overview of five technologies in use today or soon to be in use in the near future.
Smart Watches
Many people wear smart watches daily, but the powerful sensors in smart watches can provide significant benefit to the construction industry. These devises can monitor vital signs like heart rate and step counts to prevent overexertion. They can also detect falls, which is a leading cause of serious injury on a jobsite and provide an immediate alert to site and emergency personal. In addition, smart watches allow employees hands free communication.
Smart Hard Hats
Hard hats are a vital piece of PPE on every jobsite. But, these aren’t your fathers’ hard hat. By adding a sensor band around the inside of a hard hat, employers will be able to detect fatigue, prevent mircosleeps (when sudden moments of sleep occur in a fatigued individual) and proximity sensing. Proximity sensing will alert both workers and equipment operators of a potential collision and prevent serious injuries. In addition, the outside rim of the smart hard hat is equipped with a ring of LED lights that allow for visibility from a quarter mile away. This feature is especially useful for any contractors performing work at night.
Clip-Ons
Clip-ons are not part of the usual construction PPE but are proving to be very helpful. A clip-on can identify zone-based worker locations and detect free falls. With a direct line of communication, workers can immediately report injures by pushing a button.
Smart Boots
Steel toe boots are already an essential for construction workers, but in the next few years the soles in these boots will be capable of detecting shocks and falls sustained by workers, track the location of the workers more accurately and will recharge themselves by walking in them.
Smart Vests
Highly visible vests are a staple on jobsites. These new vests can track body temperature and will alert workers when a break in the shade or a drink of water is necessary to prevent heat-related illnesses. The built-in sensors can also alert workers when they are nearing or entering a hazardous area. If used in conjunction with GPS equipped equipment, they can detect nearby equipment and slow them down to avoid any safety issues.
The future of construction safety will include some form of smart device that alerts the wearer and/or the safety manager when it detects a hazard. While these wearables are not a replacement for traditional PPE and best practices, they can help prevent hazards created by human error. As they are deployed across jobsites, we’ll be able to prevent workplace injuries before they happen.
For questions about managing your jobsite risk, contact me at sclayton@ranchomesa.com or (619) 937-0167.