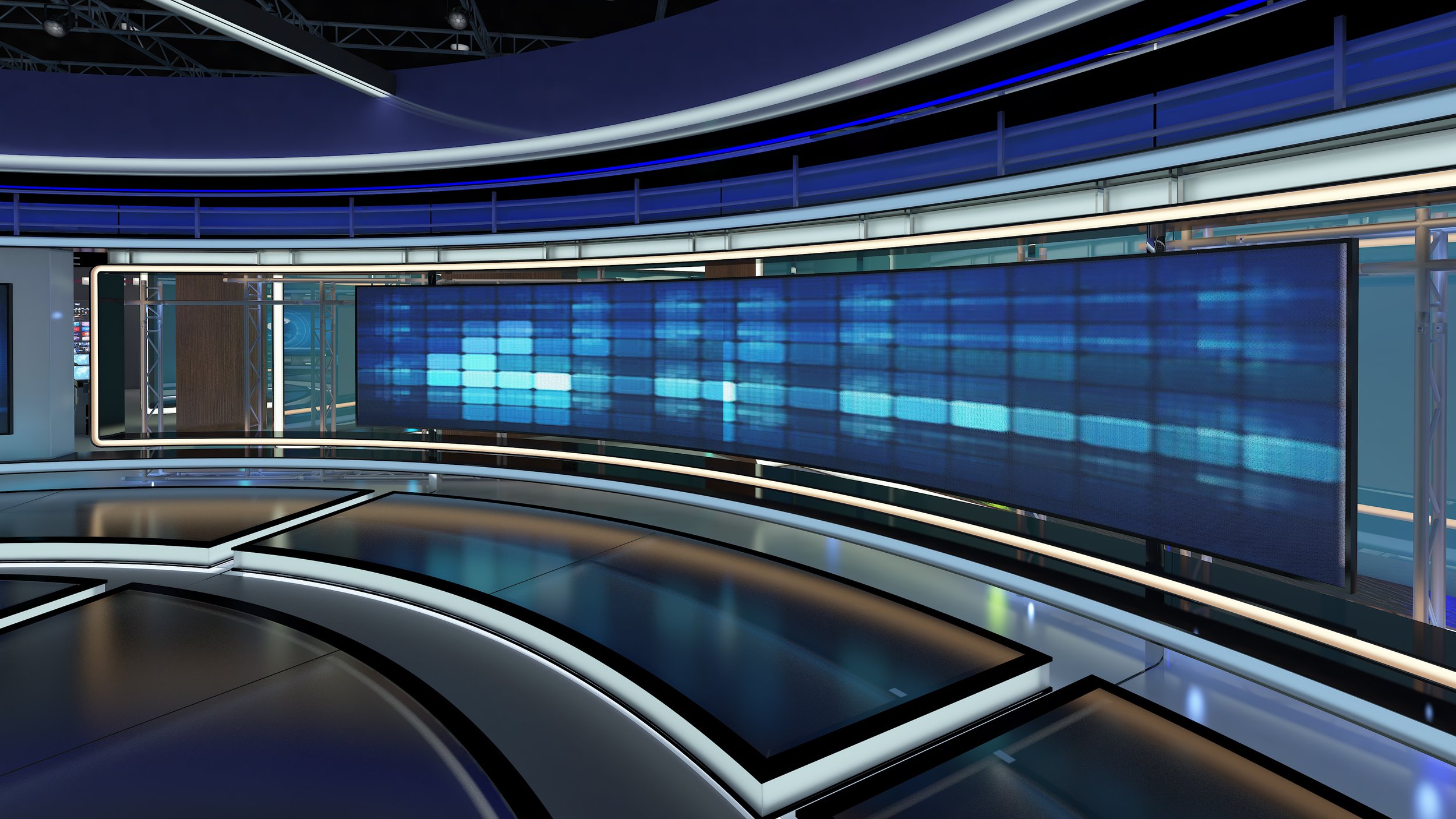
Industry News
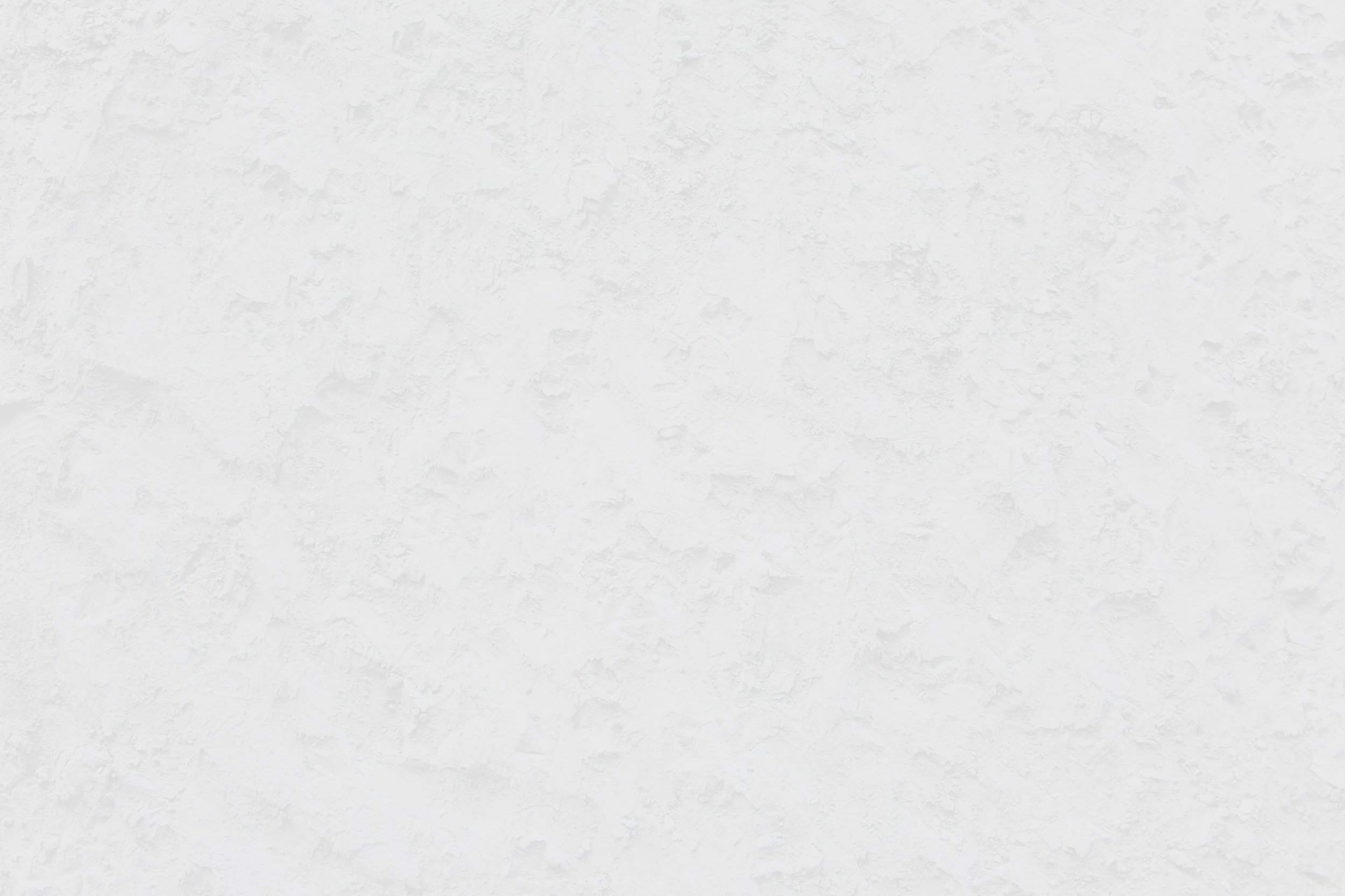
Safety Evolution: General Contractors Begin Requiring Safety Helmets Over Hard Hats
Author, Megan Lockhart, Client Communications Coordinator, Rancho Mesa Insurance Services, Inc.
The hard hat has long been a staple for construction-site safety. However, a new contender has entered the industry in 2023 as more and more general contractors are requiring safety helmets.
Author, Megan Lockhart, Client Communications Coordinator, Rancho Mesa Insurance Services, Inc.
The hard hat has long been a staple for construction-site safety. However, a new contender has entered the industry in 2023 as more and more general contractors are requiring safety helmets.
The safety helmet, while similar in form to the normal hard hat, includes added protection such as chin strap, face shield, and ear muffs. These new features allow for the helmet to sit more securely on the head while also protecting the ears from dangerously high noise levels and the eyes from possible debris.
“Since we made the switch to the new style hard hat, our employees don’t want to go back to the old-style hard hat,” Gilbane Building Company said. “This technology successfully removes the hazard of the hard hat falling off during a task, and wearing the face shield eliminates the possibility of forgetting to wear eye protection.”
While OSHA does not officially require the switch from hard hats to safety helmets, the topic was brought up at the Nation Association of Home Builders (NAHB) Spring Leadership Meeting in June 2023 in which director of OSHA’s Office of the Directorate of Construction, Scott Ketcham, granted insight on OSHA’s plans to improve jobsite safety with elevated standards for Personal Protective Equipment (PPE) in the near future.
“One initiative shared at the meeting is a pilot program for safety helmets meant to eventually replace hardhats as the preferred head protection in construction,” NAHB’s article about the meeting said. “Ketcham noted that 20% of head injuries in construction are the result of slips, trips, and falls and that hardhats do not protect against such injuries while helmets with chinstraps may stay on the head during a fall and offer protection.”
As PPE continues to evolve in the construction industry, it's important for subcontractors to be aware of what might be required of them on their job sites. Although no current laws require safety helmets over hard hats, Rancho Mesa will continue to offer updates as standards change.
Topics Your COVID-19 Training Should Cover
Author, Lauren Stumpf, Media Communications Coordinator, Rancho Mesa Insurance Services, Inc.
As states begin to lift COVID-19 restrictions and move into later phases of reopening plans, and companies begin to bring back their employees, it is important to take the necessary health and safety precautions in the workplace. Your staff should be well informed about safety precautions and resources to keep one another safe. When choosing a COVID-19 employee training, make sure it is comprehensive and includes all the necessary topics recommended by local, state and federal agencies.
Author, Lauren Stumpf, Media Communications Coordinator, Rancho Mesa Insurance Services, Inc.
As states begin to lift COVID-19 restrictions and move into later phases of reopening plans, and companies begin to bring back their employees, it is important to take the necessary health and safety precautions in the workplace. Your staff should be well informed about safety precautions and resources to keep one another safe. When choosing a COVID-19 employee training, make sure it is comprehensive and includes all the necessary topics recommended by local, state and federal agencies.
The Risk Management Center offers a 10-15 minute training designed to ensure compliance with COVID-19 safety guidelines. This general awareness course on COVID-19 covers tips on how to reduce the risk of contracting the virus by using best practices. In addition, the course covers COVID-19 characteristics and related health and safety concerns.
The COVID-19 General Awareness Online Training topics include:
COVID-19 Characteristics
CDC-Recommended Basic Precautions
Tips for Limiting Exposure
Proper Hand Washing
Social Distancing
Personal Protective Equipment (PPE)
Cross Contamination
Employer Responsibilities
Employee Temperature Checks
Face Masks
Importance of proper disinfecting and sanitation
Recommended Chemicals
What to Clean and Disinfect
Working-from-Home Ergonomics
Federal Assistance for COVID-19 Related Leave
Families First Coronavirus Response Act (FFCRA)
Paid Sick Leave
Family and Medical Leave Act (FMLA)
This online training is offered for free to Rancho Mesa clients. Contact the Client Services department at (619) 438-6869 to learn more about the COVID-19 General Awareness training.
For up-to-date COVID-19 information and HR resources please visit Rancho Mesa’s COVID-19 Information Page.
Don’t Trim Down Your Safety Procedures
Author, Rory Anderson, Account Executive, Landscape Group, Rancho Mesa Insurance Services, Inc.
Trees require regular maintenance to ensure their health and safety. Dead or diseased trees must be cut down in order to prevent injuries to people or damage to nearby structures. Maintaining trees through trimming is a dangerous task, even for experienced professionals. Unfortunately, accidents do occur. The three most common types of serious accidents experienced by tree trimmers are…
Author, Rory Anderson, Account Executive, Landscape Group, Rancho Mesa Insurance Services, Inc.
Trees require regular maintenance to ensure their health and safety. Dead or diseased trees must be cut down in order to prevent injuries to people or damage to nearby structures. Maintaining trees through trimming is a dangerous task, even for experienced professionals. Unfortunately, accidents do occur. The three most common types of serious accidents experienced by tree trimmers are falls, electrocution, and being struck by falling objects.
Falls
Falls are a common accident for tree trimmers. They can occur by slipping off of a ladder, falling from a roof, or falling out of a tree. The typical fall victim is unsecured or not properly secured. Using proper personal protective equipment is essential in preventing falls.
Electrocution
The risk of electrocution is very high when working around power lines. Some trees are planted near overhead power lines and there is a risk of electrocution to anyone trimming branches. The worker may accidentally touch the wires, or a falling branch could knock down the wires resulting in a tree trimmer touching the lines. The most common type of victim violates minimum approach distances and makes contact with the power lines through a conductive tool/object such as pruning shears. Training employees on minimum approach distances and proper trimming techniques when working around power lines can help prevent electrocution.
Falling Objects
According to the Centers for Disease Control, being struck by a falling object is the most reported tree trimming accident. A falling object is typically an entire tree or its branches/limbs, but it could also be loose equipment like a chain saw. Most victims are struck by a tree or tree limb after it falls in an unexpected direction; however, careless accidents do occur in specified drop zones. Communication between employees in the tree and on the ground is imperative to ensure the safety of all.
Tree trimming professionals face dangerous hazards on a daily basis and it is extremely important to take precautionary safety measures to make sure that they are doing everything they can to reduce risk. Safety training materials for tree trimmers are available through the Risk Management Center.
For information about Rancho Mesa's TreeOne™ program, contact Rory Anderson at (619) 937-0164.
Simple Steps to Developing a Personal Protective Equipment Program
Author, Jeremy Hoolihan, Account Executive, Rancho Mesa Insurance Services, Inc.
In the workplace, employees can be exposed to potentially harmful hazards. Identifying these hazards and using precautionary measures such as personal protective equipment (PPE) can mean the difference between a safe jobsite and an injury.
Author, Jeremy Hoolihan, Account Executive, Rancho Mesa Insurance Services, Inc.
In the workplace, employees can be exposed to potentially harmful hazards. Identifying these hazards and using precautionary measures such as personal protective equipment (PPE) can mean the difference between a safe jobsite and an injury.
PPE “is equipment worn to minimize exposure to a variety of hazards,” according to the Occupational Safety and Health Administration’s (OSHA) booklet on the subject. Examples of PPE include gloves, foot and eye protection, earplugs, hard hats, respirators and full body suites.
Implementing a PPE program can greatly reduce the chances of workplace injuries and increase a business’s productivity.
A PPE Program consists of three main components:
- An assessment of the workplace hazards and procedures, and determining what PPE will be used to protect employees.
- Employee training.
- Documentation of hazard assessment and employee training.
Conducting a Hazard Assessment
The OSHA Personal Protective Equipment Standard (29 CFR 1910.132-138) requires that employers ensure appropriate PPE is “provided, used, and maintained in a sanitary and reliable condition whenever it is necessary” to protect workers from hazards. Employers are required to assess the workplace to determine if hazards that require the use of personal protective equipment are present or are likely to be present. The following information will aid in the hazard assessment process:
- Develop a Hazard Assessment Checklist (a sample is available in the Risk Management Center) to identify exposures in the workplace that could injure a specific body part such as eyes, face, hand, arms, feet, legs, body, head, or hearing. Once you have identified the potential exposures, include the required PPE to minimize or eliminate the exposure.
- Conduct a walk-through survey of the workplace and complete the information on the Hazard Assessment Checklist. The purpose of the survey is to identify sources of hazards to workers such as chemical exposures, harmful dust, sharp objects, electrical hazards, etc.
- Select suitable PPE. Should an employer determine that PPE is necessary, they are then required to ensure that it is available and used. It is not enough to select PPE and witness its use, however. Employers must also make sure that the PPE is suitable for protection from the identified hazards, is properly fitted, and is not defective or damaged in any way.
Employee Training
Before doing work which requires PPE, employees must be trained to know the following:
- When PPE is necessary.
- The type of PPE that is necessary.
- How the PPE is properly worn.
- PPE's limitations.
- How to properly care, maintain, and disposal of the PPE.
Written Verification of Hazard Assessments and Employee Training
Employers are responsible for ensuring that employees are trained in the use of PPE and must provide written certification to that effect. Employers must also certify in writing that the employees understand the training. Also, in general, employers must provide required PPE at no cost to employees.
A large majority of workplace injuries are preventable through the implementation of a PPE Program. It is the employer’s responsibility to keep their employees adequately protected at all times. After all, it is certainly difficult to imagine a firefighter performing his or her duties without a helmet, boots, gloves and other necessary protective equipment.
Rancho Mesa Insurance Services has expertise in risk management for the construction industry. We can provide you with assistance in developing a PPE Program, as well as other risk management and insurance needs. Please contact me with any questions at (619) 937-0174 or jhoolihan@ranchomesa.com.