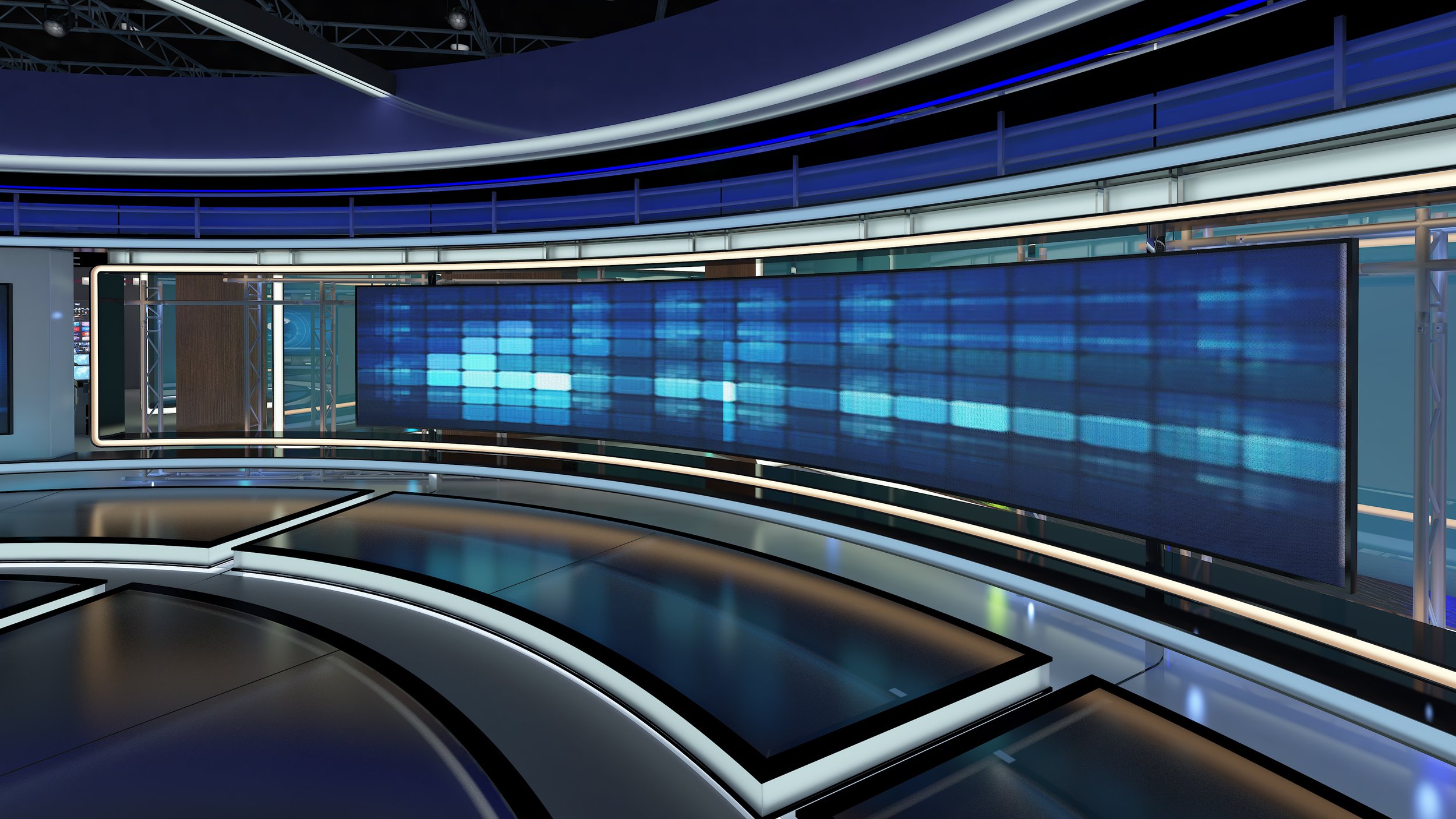
Industry News
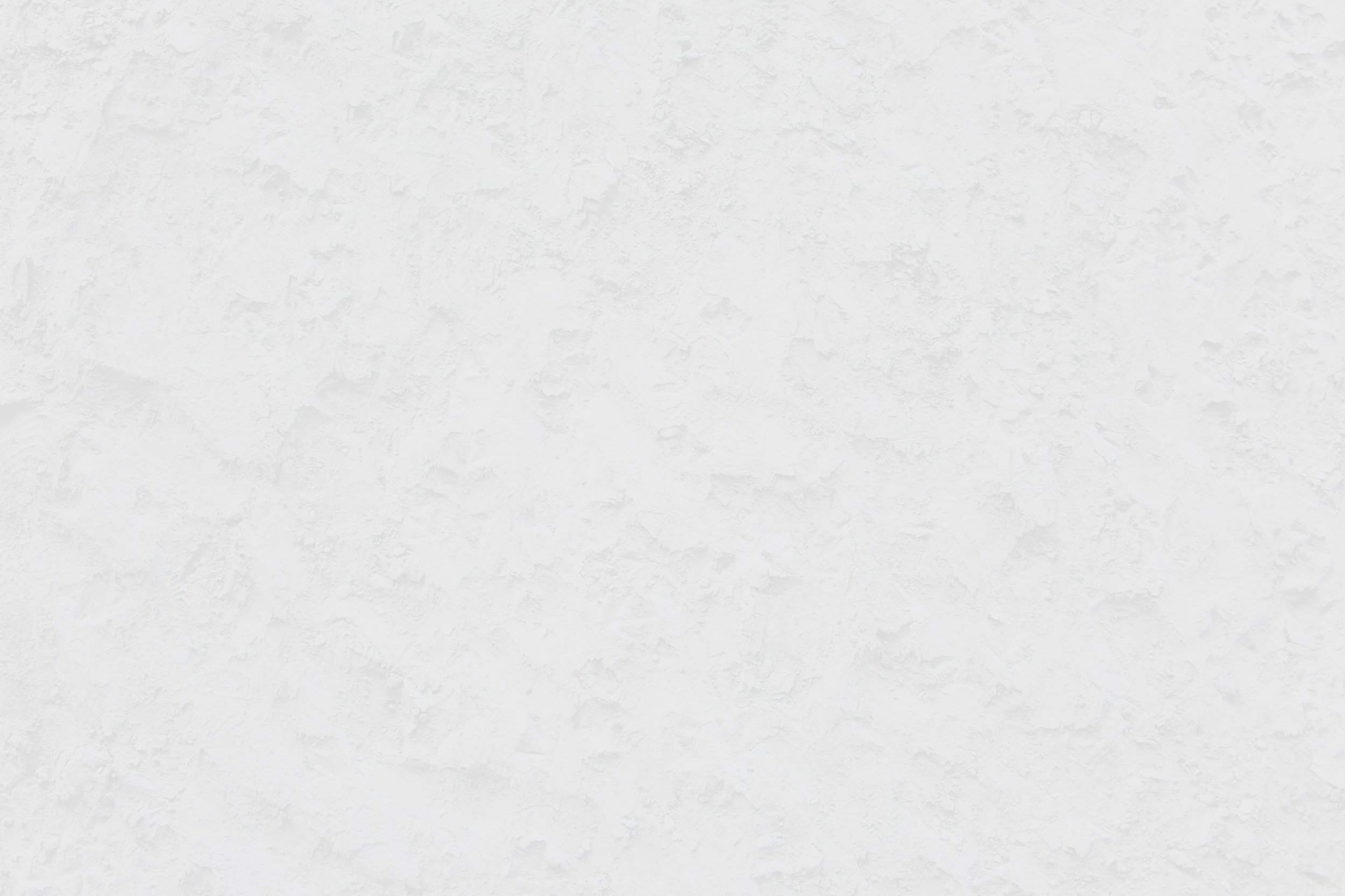
Best Practice Controls for Solar Contractors
Author, Kevin Howard, Account Executive, Rancho Mesa Insurance Services, Inc.
As we continually build broad and competitive insurance programs for solar contractors in southern California, we recently interviewed a Senior Underwriter from a national workers’ compensation carrier in an effort to learn best practice controls for these types of risks. To our delight, this underwriter provided the top five controls their team looks for while reviewing a submission to quote. Having these controls in place can show an underwriter that your company deserves the best possible pricing available in the insurance marketplace…
Author, Kevin Howard, Account Executive, Rancho Mesa Insurance Services, Inc.
As we continually build broad and competitive insurance programs for solar contractors in southern California, we recently interviewed a Senior Underwriter from a national workers’ compensation carrier in an effort to learn best practice controls for these types of risks. To our delight, this underwriter provided the top five controls their team looks for while reviewing a submission to quote. Having these controls in place can show an underwriter that your company deserves the best possible pricing available in the insurance marketplace:
1. Fall Protection
A written fall protection plan is in place and available for review
Employee training is documented
A competent person is able to assess fall hazards through a written hazard assessment prior to installation
There is familiarity with all fall arrest systems (e.g., yo-yos, ropes, lanyards, harnesses, and guardrails)
Rescue procedures and training on rescuing is in place
Assembly, maintenance, inspection, handling and storage of fall protection equipment is documented and organized
2. Responsive and Thorough Claim Reporting
Claims are reported same day
Claims are documented for future training opportunities
Witness statements from co-workers are documented
3. Outsourcing Delivery of Solar Panels to a Third Party
Minimizes the driving exposure to and from the jobsite
Lowers the material handling exposure
Reduces any potential lifting exposure while on a jobsite
4. Create a Smaller Radius of Work
Lessening of your company’s driving exposure, which in turn can lower the probability of any car accident leading to a claim
Company vehicles to return the same day which reduces any after-hours driving by employees
Allows for vehicles to be monitored more easily
5. Health Benefits are Provided
Lowers the probability of employees filing fraudulent claims
Increases overall employee wellness.
Some of these controls may be difficult or unrealistic to implement with your current business model. With workers’ compensation representing such a large line item on so many solar contractor’s profit and loss statements, engaging a forward-thinking insurance broker who can provide you additional resources and a clear renewal strategy is critical. At Rancho Mesa, we bring both of those tools to our relationships, utilizing our Risk Management Center to properly implement controls and our 20+ year history as leaders in the construction insurance marketplace.
To start a conversation about how we can assist your company, contact me at (619) 438-6874 or khoward@ranchomesa.com.
Implementing an Effective Fall Safety Program Can Have Serious Impacts
Author, Casey Craig, Account Executive, Rancho Mesa Insurance Services, Inc.
Year after year, falls are among the leading type of workers’ compensation claims and generate the highest claim costs. They account for multiple infractions on the top 10 most frequently cited standards, according to the Occupational Safety and Health Administration. How can you, as a business owner, control your exposure and keep your employees productive and healthy?
Author, Casey Craig, Account Executive, Rancho Mesa Insurance Services, Inc.
Year after year, falls are among the leading type of workers’ compensation claims and generate the highest claim costs. They account for multiple infractions on the top 10 most frequently cited standards, according to the Occupational Safety and Health Administration. How can you, as a business owner, control your exposure and keep your employees productive and healthy?
Prevention
According to the Centers for Disease Control, “27% of the 900,380 nonfatal work injuries resulting in days away from work in 2018 were related to slips, trips, and falls.” That’s a shockingly large number especially when 100% of falls are preventable if you take the time to plan, according to the National Safety Council (NSC). The NSC recommends:
Walking a job before employees get there to ensure proper set up is achievable with the equipment you are bringing for that job.
Pay attention to environmental conditions such as wind, rain, or excessive heat.
Check your equipment frequently to ensure nothing is worn down or damaged.
Make sure employees are wearing the proper foot wear and other Personal Protective Equipment (PPE) items required for the individual job needs.
Having employees working on ladders or scaffolding is essential for some jobs, and fortunately is a risk you can control. In addition to evaluating the work site, the equipment, the environmental factors, and PPE needed, you should also evaluate the health and fitness of all employees. Factors to consider should include the employee’s:
Experience
Fitness level
Age
Height Matters
A fatal fall can happen at almost any height. According to the NSC, only 16% of fatal falls in 2016 occurred as a result of a fall from over 30 feet; however, 53% of fatal falls that year resulted from below 20 feet. Given this data, best practices would dictate that construction companies should step back and reevaluate the safety procedures they have in place and determine if any changes need to be made, particularly for jobs that are considered the lower heights.
RM365 Advantage Safety Star™ Program
To get your employees properly trained, we recommend enrolling in our RM365 Advantage Safety Star™ program that includes Fall Prevention training. This program includes fundamental safety topics that allows your foreman or key management team to go through internet-based safety trainings and earn their Safety Star certification. This program has shown to improve safety while helping to reduce your workers’ compensation premiums. Register to start your RM365 Advantage Safety Star™ program, today.
Rancho Mesa understands the exposure our clients face on a daily basis and can help implement safety procedures to mitigate these risks. Underestimating a project’s risk or undertraining employees is an exposure you can address.
If you would like help in reviewing your safety protocols and procedures or if you have further questions, do not hesitate to reach out to me at (619) 438-6900 or email me at ccraig@ranchomesa.com.
Don’t Trim Down Your Safety Procedures
Author, Rory Anderson, Account Executive, Landscape Group, Rancho Mesa Insurance Services, Inc.
Trees require regular maintenance to ensure their health and safety. Dead or diseased trees must be cut down in order to prevent injuries to people or damage to nearby structures. Maintaining trees through trimming is a dangerous task, even for experienced professionals. Unfortunately, accidents do occur. The three most common types of serious accidents experienced by tree trimmers are…
Author, Rory Anderson, Account Executive, Landscape Group, Rancho Mesa Insurance Services, Inc.
Trees require regular maintenance to ensure their health and safety. Dead or diseased trees must be cut down in order to prevent injuries to people or damage to nearby structures. Maintaining trees through trimming is a dangerous task, even for experienced professionals. Unfortunately, accidents do occur. The three most common types of serious accidents experienced by tree trimmers are falls, electrocution, and being struck by falling objects.
Falls
Falls are a common accident for tree trimmers. They can occur by slipping off of a ladder, falling from a roof, or falling out of a tree. The typical fall victim is unsecured or not properly secured. Using proper personal protective equipment is essential in preventing falls.
Electrocution
The risk of electrocution is very high when working around power lines. Some trees are planted near overhead power lines and there is a risk of electrocution to anyone trimming branches. The worker may accidentally touch the wires, or a falling branch could knock down the wires resulting in a tree trimmer touching the lines. The most common type of victim violates minimum approach distances and makes contact with the power lines through a conductive tool/object such as pruning shears. Training employees on minimum approach distances and proper trimming techniques when working around power lines can help prevent electrocution.
Falling Objects
According to the Centers for Disease Control, being struck by a falling object is the most reported tree trimming accident. A falling object is typically an entire tree or its branches/limbs, but it could also be loose equipment like a chain saw. Most victims are struck by a tree or tree limb after it falls in an unexpected direction; however, careless accidents do occur in specified drop zones. Communication between employees in the tree and on the ground is imperative to ensure the safety of all.
Tree trimming professionals face dangerous hazards on a daily basis and it is extremely important to take precautionary safety measures to make sure that they are doing everything they can to reduce risk. Safety training materials for tree trimmers are available through the Risk Management Center.
For information about Rancho Mesa's TreeOne™ program, contact Rory Anderson at (619) 937-0164.
Building an Effective Fall Protection Program
Author, Daniel Frazee, Executive Vice President, Rancho Mesa Insurance Services, Inc.
In a Census summarizing fatal occupational injuries from 2016, those originating from falls continued a steady upward trend that began in 2011 and increased another 6% in 2016. More specifically, falls increased more than 25% for roofers, painters, carpenters, tree trimmers & pruners. Since 2013, fall protection citations have been #1 or #2 on OSHA’s most cited violations. Now, more than ever, it is essential for employers with personnel who work at heights to provide comprehensive fall protection.
Author, Daniel Frazee, Executive Vice President, Rancho Mesa Insurance Services, Inc.
In a Census, summarizing fatal occupational injuries from 2016, those originating from falls continued a steady upward trend that began in 2011 and increased another 6% in 2016. More specifically, falls increased more than 25% for roofers, painters, carpenters, tree trimmers & pruners. Since 2013, fall protection citations have been #1 or #2 on OSHA’s most cited violations. Now, more than ever, it is essential for employers with personnel who work at heights to provide comprehensive fall protection.
Job Hazard Analysis
While developing any type of new safety program, experts encourage breaking the process into steps. These steps must be designed for all construction sites where exposure to height exists. And the plan must be prepared by a competent (qualified) person, defined as someone with extensive knowledge and training on fall protection systems. The initial step requires a job hazard analysis to be performed at the location in advance of work commencing. The analysis can include determining the average & maximum height at which work will be performed, identifying the number of employees using the area, observing potential hazards that might compromise the work, and modifying work to reduce exposure. According to the American National Standards Institute (ANSI), “the most desirable form of protection is elimination of the need to work from height” (Z359.2, section 5.1).
Types of Fall-Arrest Systems
Assuming hazards cannot be eliminated and the need to work from height still exists, employers can implement both passive and active fall-arrest systems. Passive systems can include examples such as guardrails or ladder cages while the more technical active fall-restraint systems can use specialized lanyards and anchors to eliminate fall exposure. These require individualized training that is crucial for proper use and effectiveness.
Proper Implementation & Calculating Fall Clearance
Once you have identified the appropriate system for the jobsite, the implementation is critical to the success of the program. Using the more complex active fall-arrest system as an example, employers can track their progress with four steps:
- Anchorage-the secure point of attachment to the fall arrest system. The structure must be capable of supporting at least 5,000 pounds/worker or meet OSHA’s criteria of a 2:1 safety factor.
- Body Support-the connection point to the anchorage, commonly seen with a full body harness that distributes the forces of a fall over the chest, shoulders, pelvis & thighs.
- Connectors-examples include lanyards and self-retracting lifelines, devices that connect or link the harness to the anchorage.
- Descent & Rescue-all good fall protection programs must have a plan for rescue or retrieval of a fallen worker. Employees need to be raised or lowered to a safe location when needed.
As employers build out their fall-arrest system, calculating fall clearance and swing fall hazards represent key components to a successful program. In part, this can be achieved by determining sufficient clearance below the worker to stop the fall before he/she hits the ground or another object. It should include an awareness of the anchorage location, the connecting system, deceleration distance, the height of the suspended worker, etc.
Training, Training, Training
Formal, written training programs only become effective tools when employers combine classroom knowledge with practical, hands-on experience. Competent persons need to continually educate workers on industry regulations, proper equipment selection/use and ongoing maintenance standards. This must be emphasized on a consistent basis so that workers understand the importance of fall protection as it relates to their own safety and that of the company.
Improving Your Risk Profile
Without argument, the most important reason for introducing a Fall Protection program is the safety and well-being of your employees. Getting workers home safely at the end of every work day remains every employer’s ultimate goal. A second goal for consideration is that of improving your company’s risk profile to the insurance marketplace. If your construction firm performs work in excess of 2 stories, underwriters expect to see details on your Fall Protection program. While just one aspect of a Best Practices renewal strategy, providing a copy of your program with training examples and site specific layouts can give insurance company underwriters the comfort level they need to deliver more competitive quote proposals. Allowing your insurance broker these reference points can help them engage more options which can lead to better terms and pricing, and lower overall insurance costs for your company.
As your company builds out safety modules and looks to refresh or develop new a Fall Protection program, look to Rancho Mesa Insurance and their Risk Management Center (RMC) for assistance. The RMC contains endless content, program templates and resources for our construction partners. Additionally, the Agency’s monthly offerings of industry specific trainings and webinars provides the education our clients need to stay ahead of their competition.
For more information about fall protection, contact Rancho Mesa Insurance Services, Inc. at (619) 937-0164.
OSHA Announces Top 10 Cited Violations for FY 2017
Author, Sam Clayton, Vice President, Construction Group, Rancho Mesa Insurance Services, Inc.
The Occupational Safety and Health Administration (OSHA) released its preliminary top 10 citation list for fiscal year 2017 at the annual National Safety Council (NSC) Congress and Expo, held in late September 2017.
Author, Sam Clayton, Vice President, Construction Group, Rancho Mesa Insurance Services, Inc.
The Occupational Safety and Health Administration (OSHA) released its preliminary top 10 citation list for fiscal year 2017 at the annual National Safety Council (NSC) Congress and Expo, held in late September 2017.
“One thing I’ve said before in the past on this is, this list doesn’t change too much from year to year,” said Patrick Kapust, deputy director of OSHA’s Directorate of Enforcement and Programs, during the expo presentation. “These things are readily fixable. I encourage folks to use this list and look at your own workplace.”
OSHA compiled the list using data collected from incidents occurring from October 2016 through September 2017.
- Fall Protection in Construction: 6,072 violations.
Frequently violated requirements include unprotected edges and open sides in residential construction and failure to provide fall protection on low-slope roofs - Hazard Communication: 4,176 violations.
Not having a hazard communication program topped the violations, followed by not having or providing access to safety data sheets - Scaffolding: 3,288 violations.
Frequent violations include improper access to surfaces and lack of guardrails - Respiratory Protection: 3,097 violations.
Failure to establish a respiratory protections program topped these violations, followed by failure to provide medical evaluations - Lockout/Tagout: 2,877 violations.
Frequent violations were inadequate worker training and inspections not completed. - Ladders in Construction: 2,241 violations.
Frequent violations include improper use of ladders, damaged ladders and using the top step. - Powered Industrial Trucks: 2,162 violations.
Violations include inadequate worker training and refresher training. - Machine Guarding: 1,933 violations.
Exposure points of operation topped these violations. - Fall Protection-training requirements: 1,523 violations.
Common violations include failure to train workers in identifying fall hazards and proper use of fall protection equipment. - Electrical-wiring methods: 1,405 violations.
Violations of this standard were found in most general industry sectors, including food and beverage, retail and manufacturing
Training materials for each of the items on the OSHA list are available within the Risk Management Center. Contact Rancho Mesa Insurance Services, Inc. at (619) 937-0164, for more information.