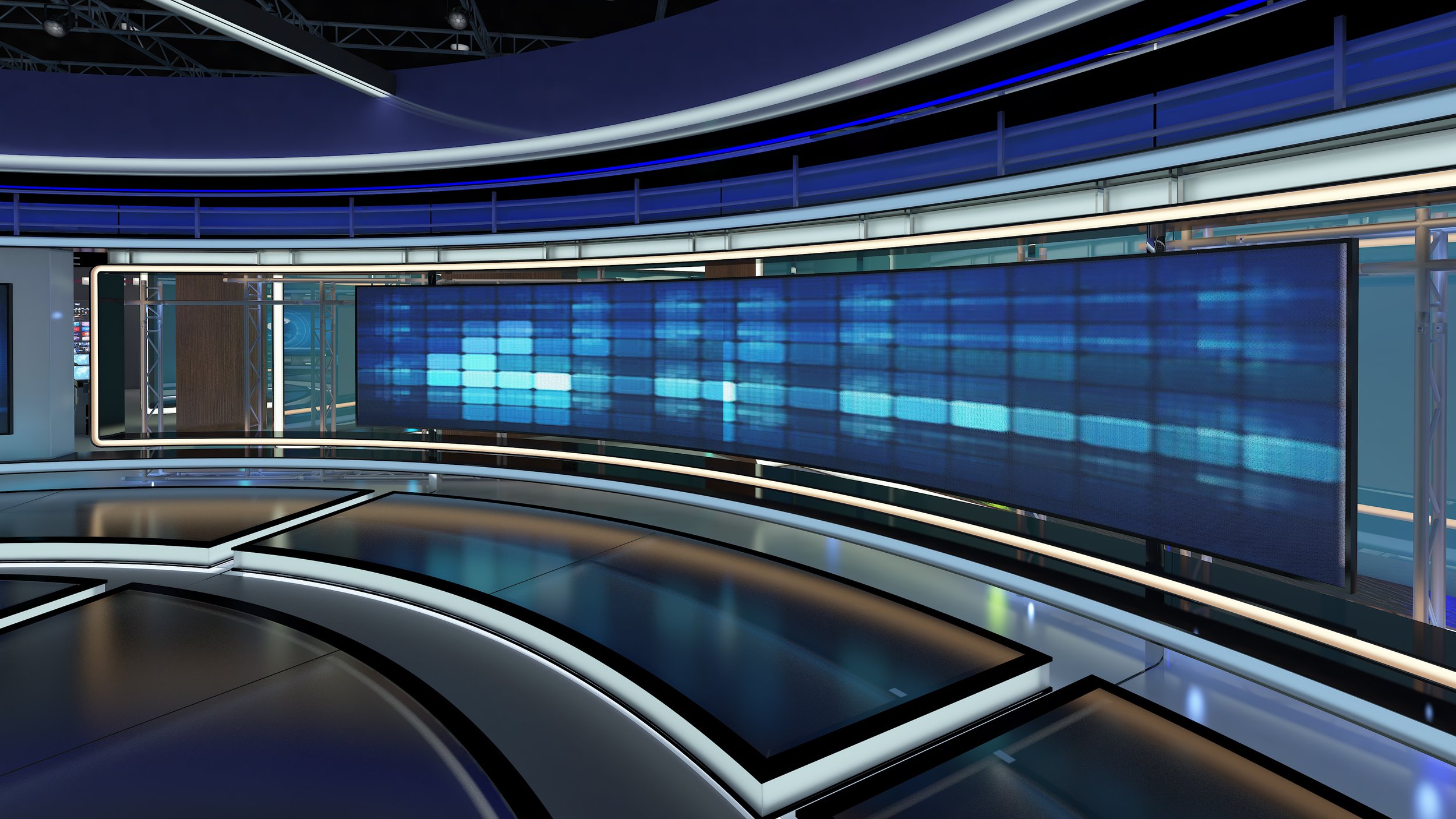
Industry News
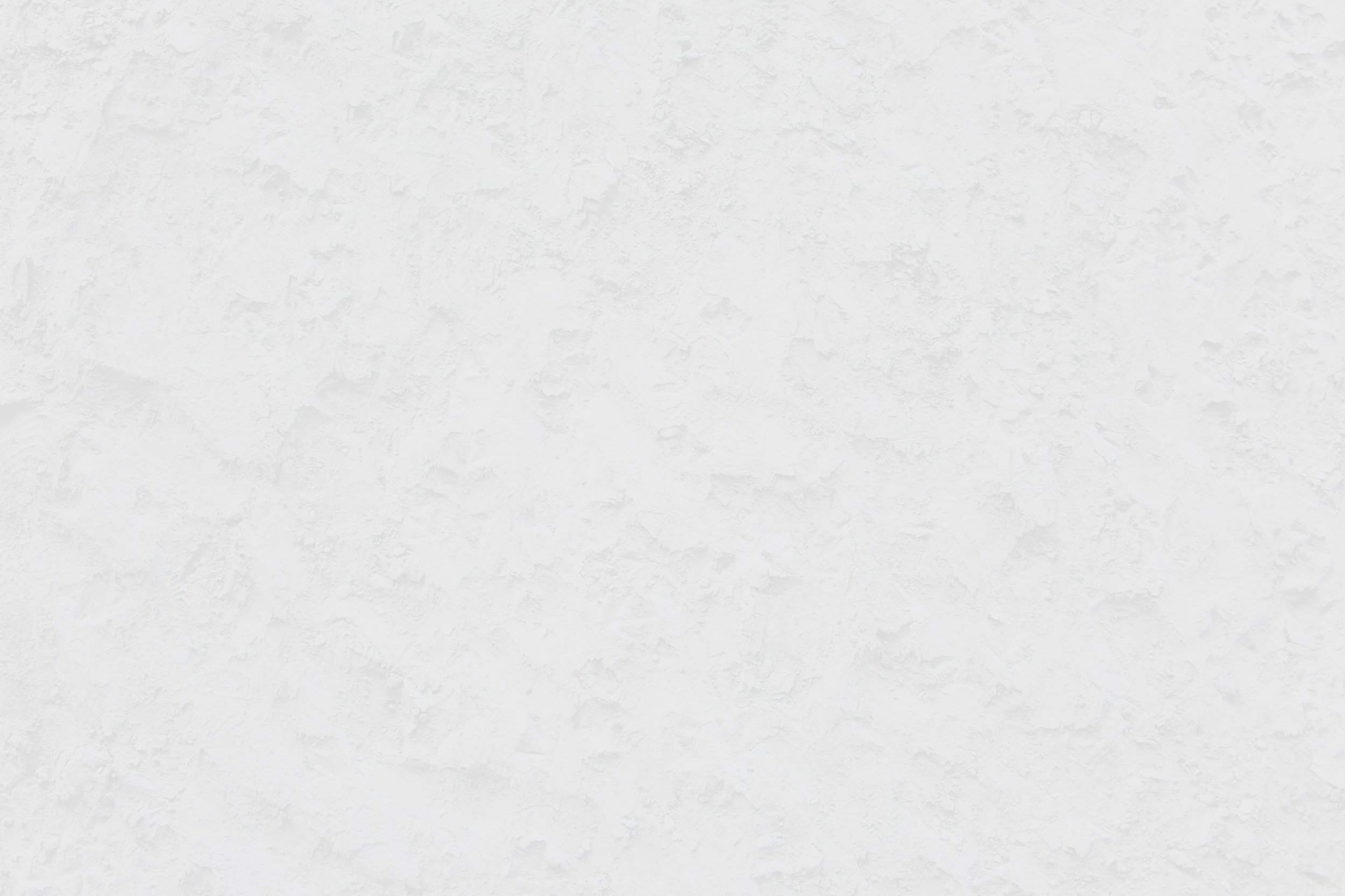
Understanding the Impact of MEP Contractors’ Dual Wage & Total Temporary Disability
Author, Sam Clayton, Vice President, Construction Group, Rancho Mesa Insurance Services, Inc.
What is a dual wage threshold? According to the Workers’ Compensation Insurance Rating Bureau (WCIRB), in California there are sixteen (16) construction operations that are divided into two separate classifications based on the hourly wage of the employee. There are different advisory pure premium rates for the low wage employee and the high wage employee.
Author, Sam Clayton, Vice President, Construction Group, Rancho Mesa Insurance Services, Inc.
What is a dual wage threshold? According to the Workers’ Compensation Insurance Rating Bureau (WCIRB), in California there are sixteen (16) construction operations that are divided into two separate classifications based on the hourly wage of the employee. There are different advisory pure premium rates for the low wage employee and the high wage employee. For mechanical, electrical and plumbing (MEP) contractors, the class codes used are all included in the recently approved increase which will go into effect September 1, 2022. The table below outlines the changes for the MEP class codes by year.
Classifications | 9/1/2021 - Current | 9/1/2022 - Proposed |
5140/5190 | $32 | $34 |
5183/5187 | $28 | $31 |
5538/5542 | $27 | $29 |
© 2021 Workers' Compensation Insurance Rating Bureau of California. All Rights Reserved.
Why does this matter to MEP contractors? The higher wage employee’s workers’ compensation rate is significantly less (on average 46% less) than the lower wage employee. Therefore, if a company has any employees that are currently just barley in the high wage classification, this would drop those employees into the low wage classification and the employer would pay the higher workers’ compensation rate on those individuals. Depending on how many employees an employer has in this situation, it may be advantageous for the employer to calculate if it makes more sense to give those impacted employees a raise to push them back up into the high wage classification or keep them in the new low wage classification. It should be noted and understood that this change will not impact the employer until their next renewal after September 1, 2022. So while most employers will have time to evaluate the impact, it is crucial to begin the evaluation sooner rather than later.
As with any form of wage inflation, an increase in wages, to keep an employee in the higher wage category will increase the claim costs of a total temporary disability claim if they are injured on the job. While increases in wages are necessary, they will also impact the total cost of the claim, which then can increase the company’s experience modification rating (XMOD).
To mitigate this increase and reduce the likelihood of a lost time claim, employers can take several actions:
Review and update their existing safety programs.
Revisit their hiring practices.
Develop a sustainable return-to-work program.
What should employers do next?
Work with your trusted insurance advisor and run a needs/benefit analysis on increasing employee wages.
Understand your numbers.
What is your primary threshold and why does it matter?
What is my claim cost per point of XMOD?
How does my frequency of claims compare to the MEP industry?
How does my lost time claim average compare to other MEP contractors?
If you would like assistance understanding how these and other data points impact your company, request a proprietary Key Performance Indicator (KPI) dashboard that puts this information at your fingertips.
You still have time to be proactive, do not let these critical changes catch you by surprise!
Artisans Captive – Risk Control Workshop Recap
Author, Amber Webb, Account Executive, Rancho Mesa Insurance Services, Inc.
On January 20th and 21st of 2022, Captive Resources hosted the Artisans Captive Risk Control Workshop at The US Grant in San Diego, CA. The workshop was intended for all Artisans’ risk and/or safety mangers, human resources, claims managers, supervisors, owners, brokers and any others who wished to attend.
Author, Amber Webb, Account Executive, Rancho Mesa Insurance Services, Inc.
On January 20th and 21st of 2022, Captive Resources hosted the Artisans Captive Risk Control Workshop at The US Grant in San Diego, CA. The workshop was intended for all Artisans’ risk and/or safety mangers, human resources, claims managers, supervisors, owners, brokers and any others who wished to attend.
The workshop began with a brief introduction to the members of Captive Resources and Zurich Insurance Group, along with quick summaries of each of their responsibilities. Then, immediately following was an overview of how the captive is operated and how each member company can earn points which ultimately contribute towards the calculation of their year-end dividend. The group was able to hear from Rich McElhaney from The Real Cost of Safety, as the keynote speaker on the 20th. His story was captivating and eye opening to just how quick something can go wrong on a jobsite without the proper safety protocols in place. He stressed the importance of getting supervisors and employees to report their near misses. Each time a near miss is reported, it gives the company an opportunity to do a training and possibly make changes to their safety policies and procedures to avoid future incidents. Reporting near misses also gives companies a chance to look at areas where trends are taking place and make the appropriate adjustments.
The first day of the workshop ended with dinner and a tour of the USS Midway. This was a great time for member companies to network and chat about what each other are doing with regard to their risk control and safety programs.
The second day of the workshop on the 21st, we all met early for breakfast which also allowed for more networking and learning about different member companies. Immediately after breakfast, we all broke out into our different session groups to learn about specific topics. The first session focused on the, “Do’s & Don’ts of Accident Investigation.” In this session, we went over a twelve-step process for what to do when there is an accident on the job. We were given several great tips for what to do and what not to do. One recommendation was to take pictures of all four corners of your vehicle, then all four sides and repeat for all other vehicles at the scene. The presenter also encouraged not using the phrase, “no comment” if the media becomes involved. Instead, showing empathy and compassion while still not commenting can lead to a better outcome while the investigation is still ongoing. Another takeaway from this session was the importance of reviewing all of your policies to ensure they do not stress productivity over safety. Then, make sure to train your employees to understand that their wellbeing is top of mind, while actually enforcing a safety culture.
The second session we attended was “Driver Safety: Lucky vs. Good” where we learned that the highest auto expenses result from rear end accidents. Also, according to the Bureau of Labor Statistics’ national census of fatal injuries released in December of 2021, transportation incidents have the most workplace fatalities, followed by falls and struck by objects. We also learned with new vehicle technology, such as high-intensity headlights, forward automatic braking, forward collision alert, lane departure warning and rear vision cameras, employers can help reduce vehicle crashes. The speaker went on to explain the importance of utilizing the data given by fleet analytics to help with reducing collision and use as a tool for focusing on trends happening within your fleet.
The final keynote speaker was Sean Bott and he spoke on the “Safety Dance: Creating the Courage to Connect on Site through Three Simple Steps.” His session was not only comedic, but also entertaining. He was able to teach us the 3 steps of meaningful connection; 1) Interrupting, 2) Introducing and 3) Inquiring. We have to start by interrupting people’s defenses and fears and can do this simply by a genuine compliment, a smile, a wave, etc. Then, once the walls are down, we are able to introduce ourselves while slowly saying our name with a pause between our first and last name, all while using the triple nod technique. He also encouraged us to smile and even throw in a wave during this process of introduction. Finally, we were taught to inquire in a clear and meaningful way to get to know the other person on a deeper level. He related these skills back to how employers interact with their employees on all levels, but specifically when it comes to safety. He suggested that we all combine these three skills to make others feel seen, heard, felt and valued. He displayed the value in bringing the human element to safety and reminding the group that the ultimate goal is to make sure all employees go home safely.
Overall, this workshop was very informative with some fun mixed in and ample time for networking to get to know the other companies involved in the Captive. As a Rancho Mesa broker attending with several of our clients, it allowed us to see the value of not only this workshop, but the additional benefits of being a member of the Artisans Captive and what it offers.
For those interested in learning more about Captives and their potential place within your organization, we will be hosting an informational Captive workshop for the Artisans Captive on April the 28th. Register online, today.
If you have any questions or would like to discuss this option further, you can contact me at awebb@ranchomesa.com or call me at (619) 486-6562.
Top Five Workers’ Compensation Claims That Impact a MEP’s Bottom Line
Author, Amber Webb, Account Executive, Rancho Mesa Insurance Services, Inc.
If you are an MEP contractor who wants to impact both your productivity and profitably, then the following is crucial for your success. Our MEP Group at Rancho Mesa understands the importance of identifying the top five workers’ compensation claims that impact your industry while providing pertinent resources to help mitigate that risk.
Author, Amber Webb, Account Executive, Rancho Mesa Insurance Services, Inc.
If you are a Mechanical, Electrical & Plumbing (MEP) contractor who wants to impact both your productivity and profitably, then the following is crucial for your success. Our MEP Group at Rancho Mesa understands the importance of identifying the top five workers’ compensation claims that impact your industry while providing pertinent resources to help mitigate that risk. By working with leading workers’ compensation carriers and the Occupational Safety and Health Administration (OSHA), we identified the top 5 workers’ compensation claims affecting the MEP industry:
Cut/Puncture/Scrape/Lacerations
Slip/Falls from both same level and ladders/scaffolding
Strains from lifting/handling/pushing/pulling
Struck by object/Foreign Body in Eye
Motor Vehicle Accident (injured employee)
With employee safety at the forefront of your operations, understanding where the claims are likely to come from and then having the support and tools in place to address those concerns is vital to your long term success. When injuries occur on the job, it impacts not only the life of the injured worker and their family but will directly impact the productivity and profitability of the project.
For our clients to proactively mitigate these exposures, we provide them with access to specific trainings related to these top MEP claims and OSHA citations from our Risk Management Center Library. Our Client Services team then works closely with our clients to customize their trainings while meeting their specific risk management needs.
If you are not already a Rancho Mesa client, and would like a free trial of our Risk Management Center, please complete the form or contact Amber Webb at (619) 486-6562 or awebb@ranchomesa.com.